Kella Knack
|  Creado: Septiembre 23, 2019
 | 
Actualizado: Septiembre 13, 2020
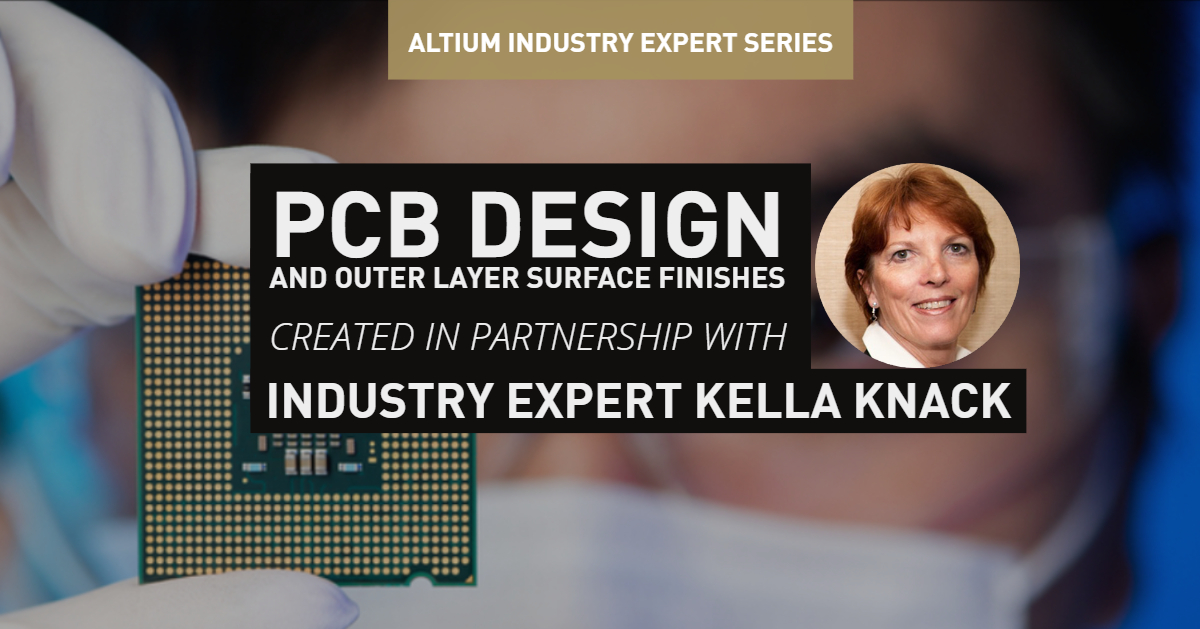
Aunque podría parecer prematuro en lo que respecta a las consideraciones generales de desarrollo del producto, determinar qué acabado superficial de la capa externa es el adecuado es algo que debe abordarse al principio del proceso de diseño de la PCB. Existen varios acabados superficiales de la capa externa y todos tienen sus propias ventajas y desventajas. El más adecuado para tu diseño concreto depende en gran medida de la aplicación final de tu producto. En este artículo se describen las distintas clases de superficies disponibles; su historia y evolución; las ventajas y desventajas de cada una de ellas; en qué lugar de la fabricación de una PCB se aplica una superficie concreta y el estado actual del sector.
Es justo plantearse la siguiente pregunta: «¿Qué tiene que ver el acabado superficial con mi diseño de alta velocidad?». Es posible que la respuesta sea «nada» pero, con el paso de los años, hemos visto cómo fallaban cientos de diseños de alta velocidad elegantemente ejecutados debido a unas conexiones de soldadura inestables que podían atribuirse al uso de un acabado superficial inadecuado. Cuando esto ocurre, la única solución consiste en tirarlo todo y volver a empezar. Esto puede ocasionar unos costes enormes y retrasos que podrían impedir que un producto se comercialice a tiempo y no genere los ingresos previstos.
El objetivo de todos los acabados superficiales de la capa externa, independientemente del tipo y del momento en el proceso general de fabricación en el que se apliquen, es proteger las áreas de la superficie de cobre frente a la corrosión en aquellos puntos donde se soldarán los componentes.
- Soldadura galvanizada
- Estaño galvanizado
- HASL
- ENTEC 106® u otra protección orgánica
- ENIG
- ENPIG
- Oro galvanizado sobre níquel galvanizado
- Inmersión de estaño
- Inmersión de plata
Es importante apuntar que la aplicación de estos acabados superficiales de la capa externa se produce en distintas fases del proceso de fabricación de la PCB. Además, el lugar de aplicación tiene un efecto directo sobre el buen funcionamiento de cada acabado. Estas dos fases distintas incluyen:
En este caso, el metalizado sirve como resistencia al grabado cuando llega el momento de eliminar el cobre no deseado de las capas externas. Los acabados en esta categoría incluyen soldadura galvanizada, estaño galvanizado y oro sobre níquel galvanizado.
En este caso, la soldadura galvanizada o el estaño galvanizado se utilizan como resistencia al grabado cuando se graban las capas externas. Este galvanizado se retira antes de aplicar la máscara de soldadura, dejando el cobre expuesto donde se harán las conexiones soldadas. Estos acabados superficiales de la capa externa están compuestos de materiales anticorrosivos para proteger los pads de montaje de los componentes hasta que finaliza la soldadura. Más adelante se explica detalladamente su uso. Los acabados específicos en esta categoría incluyen HASL, recubrimientos orgánicos como ENTEC 106, ENIG, ENEPIG, inmersión de estaño e inmersión de plata.
La evolución de estos acabados tuvo lugar de la siguiente manera:
- La soldadura galvanizada es el acabado de superficie original utilizado en el sector de las PCB. Es el acabado de más bajo coste, ya que realiza dos tareas en una sola operación. En primer lugar sirve como resistencia al grabado. También sirve como protección para las superficies de cobre sobre las que soldarán los componentes. El problema es que la máscara de soldadura que se aplica sobre este acabado superficial puede fallar cuando la soldadura bajo dicha máscara sobre las pistas se derrite durante la soldadura por ola. Esto crea cortocircuitos entre las pistas. Además, este acabado contiene una cantidad indeseable de plomo. Como resultado, se sustituyó por el siguiente acabado.
- El estaño galvanizado entró en escena como reemplazo RoHS de la soldadura galvanizada. El atractivo de este acabado es que la máscara de soldadura podría aplicarse directamente sobre el estaño y podría utilizarse como acabado final de superficie. Esto se probó en varios productos, incluidas placas base, con resultados dispares. El problema es que el estaño puro, así como varias aleaciones de estaño, presentan unos diminutos filamentos de estaño entre los circuitos de distintos voltajes. Cuando esos filamentos crecen, provocan cortocircuitos y líneas de fuga. Estos filamentos suelen aparecer algún tiempo después del ensamblaje de la PCB, cuando está ya en manos del usuario, lo que ocasiona una devolución. Por este motivo, cualquier forma de estaño como acabado superficial no es una opción fiable para las implementaciones de PCB.
- SMBOC (solder mask over bare copper, máscara de soldadura sobre cobre puro) como proceso se introdujo para abordar el problema de cortocircuito de la soldadura. Aquí, la soldadura o el estaño se elimina de las pistas antes de la aplicación de la máscara de soldadura. Puesto que la máscara de soldadura se adhiere muy bien al cobre puro, soluciona el problema de cortocircuito de la soldadura. Sin embargo, deja los pads de montaje expuestos, ya que el cobre puro se oxida muy rápidamente. Esto quiere decir que se necesita algún tipo de material anticorrosivo para proteger los pads de montaje de cobre. Estos materiales anticorrosivos se indican más arriba y a continuación se ofrecerá más información sobre ellos.
- Oro galvanizado sobre níquel galvanizado como acabado superficial es tan antiguo, si no más, que la soldadura galvanizada. Las ventajas de este acabado es que resulta fácil de metalizar, es una excelente protección para las superficies de cobre y tiene buen aspecto. No obstante, es el acabado más caro, así que solamente se utiliza en las PCB de mayor precio. Pero también conlleva algunos riesgos menores. Cuando este acabado se utiliza en PCB con orificios pequeños, con alta relación de aspecto, hay un problema con el proceso de grabado que se utiliza para eliminar el cobre no deseado de las capas externas de la PCB. El níquel y el oro protegen el cobre en los orificios de paso metalizados Si el proceso de metalizado utilizado para depositar el níquel no se controla muy bien, el cobre del centro de un orificio de paso metalizado no quedará cubierto Esto no es un problema si el cobre está completamente grabado porque se muestra como un circuito abierto y la tarjeta puede desecharse antes de que se siga procesando. El problema es que en el orificio queden pequeñas cantidades de cobre y esto sea suficiente para pasar la comprobación de la tarjeta. Sin embargo, tras el proceso de soldadura el cobre suele fallar y eso da lugar a una PCB defectuosa. Hay formas de abordar este tipo de fallo del cobre. La primera es metalizar cobre adicional en los orificios para permitir el proceso de grabado. La segunda es conectar las vías situadas en las partes superior e inferior de la PCB con un material fotoimageable antes de grabar las capas externas.
Como se indica anteriormente, los siguientes acabados se aplican después de que la PCB haya sido completamente metalizada y las capas externas se haya grabado con su patrón final y se haya aplicado la máscara de soldadura. Los acabados que entran dentro de esta categoría incluyen los siguientes:
- HASL (hot air solder leveling, soldadura con nivelado de aire caliente) fue el primer acabado creado para PCB de SMOBC y sigue siendo la primera elección de acabado para este tipo de placas. Es el acabado menos caro después de la soldadura galvanizada. HASL se aplica mediante la inmersión de la PCB de SMOBC en un recipiente de soldadura fundida para cubrir todo el cobre expuesto. La PCB se extrae del baño de soldadura a través de un par de cuchillos de aire que eliminan el exceso de soldadura, dejando la cantidad suficiente sobre cada pad para protegerlos de la corrosión. La desventaja de este acabado es que la altura de los pads de soldadura no es uniforme, por lo que los QFP y BGA de paso fino acaban con cortocircuitos o circuitos abiertos en la soldadura. Además, con HASL, las PCB se someten a un intenso choque térmico cuando se sumergen en la soldadura fundida. En las PCB gruesas que contienen un gran número de pequeños orificios de paso metalizados puede ocasionar el fallo de algunos de dichos orificios metalizados.
- ENTEC 106® o recubrimientos orgánicos son films delgados de sustancias orgánicas que protegen los pads de cobre hasta que tiene lugar la soldadura, donde sirven como fundentes de soldadura. Una ventaja de ENTEC es que no resulta caro en comparación con algunas de las demás opciones de acabados superficiales de la capa externa. La desventaja de este tipo de recubrimiento es que si el acabado se toca con los dedos queda destruido, con lo que la PCB queda inutilizable hasta que se elimina el recubrimiento y se vuelve a aplicar. Por eso ENTEC y otros recubrimientos similares no resultan adecuados para prototipos que tengan más posibilidades de ser manipulados. Pero sí que es un acabado adecuado para la producción de PCB.
- ENIG (electroless nickel under immersion gold, níquel no electrolítico con inmersión de oro) puede ser un buen recubrimiento si se aplica correctamente. «No electrolítico» e «inmersión» indican que el níquel y el oro deben depositarse sobre el cobre sin utilizar la electricidad. El problema es que este acabado se aplica con dos complejos baños químicos. Si no se mantiene bien la química, el resultado son pads negros. Este es un material que hará que las uniones de soldadura sean débiles y fallen a menudo al salir de las operaciones de soldadura. Desgraciadamente no existe ninguna solución para este problema y todo el ensamblaje tendrá que descartarse. Otra desventaja con ENIG es que la capa de oro que se aplica es tan fina que no ofrece protección anticorrosiva a largo plazo, y las placas resultantes no tienen periodo de conservación.
- ENEPIG (electroless nickel electroless palladium immersion gold, níquel no electrolítico paladio no electrolítico con inmersión de oro) se ha venido utilizando unos 10 años y se ha proclamado como un sustituto adecuado de ENIG. Las pruebas indican que presenta problemas similares de pad negros y exposición a la corrosión. Hemos visto indicios de ambos tipos de fallos por lo que no recomendamos este acabado.
- La inmersión de estaño al principio parecía ser un acabado muy atractivo. Como no contiene plomo, cumple los requisitos de la directiva RoHS y resulta muy fácil de aplicar. Pero, como se indica anteriormente, el estaño crea filamentos que lentamente ocasionan cortocircuitos o líneas de fuga, así que no lo recomendamos como acabado de superficie. La inmersión de plata es el acabado de elección si no puedes permitirte oro galvanizado sobre níquel galvanizado. Ofrece una larga vida útil y es tan barato como ENTEC. El único problema es que se vuelve negro (se ensucia). No obstante, este es un problema cosmético, no de rendimiento. Como respuesta, algunos OEM han decidido utilizar ENTEC en todos los lugares que van a ser soldados y después usar ENIG en los pads que quedarán expuestos después del ensamblaje. Así, las placas quedan «bonitas», funcionan como se supone que deben hacerlo y los clientes están satisfechos con su aspecto.
Resumen
Hay varios acabados superficiales de capa externa disponibles en el sector. Comprender la dinámica,
las ventajas y desventajas de cada uno de ellos es esencial para garantizar que el acabado que elijas sea el adecuado para tu implementación concreta de PCB. Tener en cuenta estos factores en las primeras etapas de la fase de diseño asegurará que todo el proceso de elaboración de tu producto transcurra sin problemas desde el diseño, a la fabricación y las operaciones de ensamble.
¿Te gustaría saber cómo Altium puede ayudarte en el diseño de tu próxima PCB? Habla con un experto de Altium o lee esta Guía de diseño de PCB de alta velocidad para obtener una visión general de todo lo que necesitas saber. Para obtener más información sobre los temas tratados en este artículo, también puedes leer las publicaciones que se indican más adelante.
REFERENCIAS
- Ritchey, Lee W. and Zasio, John J., “Right The First Time, A Practical Handbook on High-Speed PCB and System Design, Volume 2.”
- Ritchey, Lee W., “Update on PCB Surface Finishes,” Current Source Newsletter, Volumen 1, Número 4, Agosto 2005