Kella Knack
|  Créé: Septembre 23, 2019
 | 
Mise à jour: Septembre 13, 2020
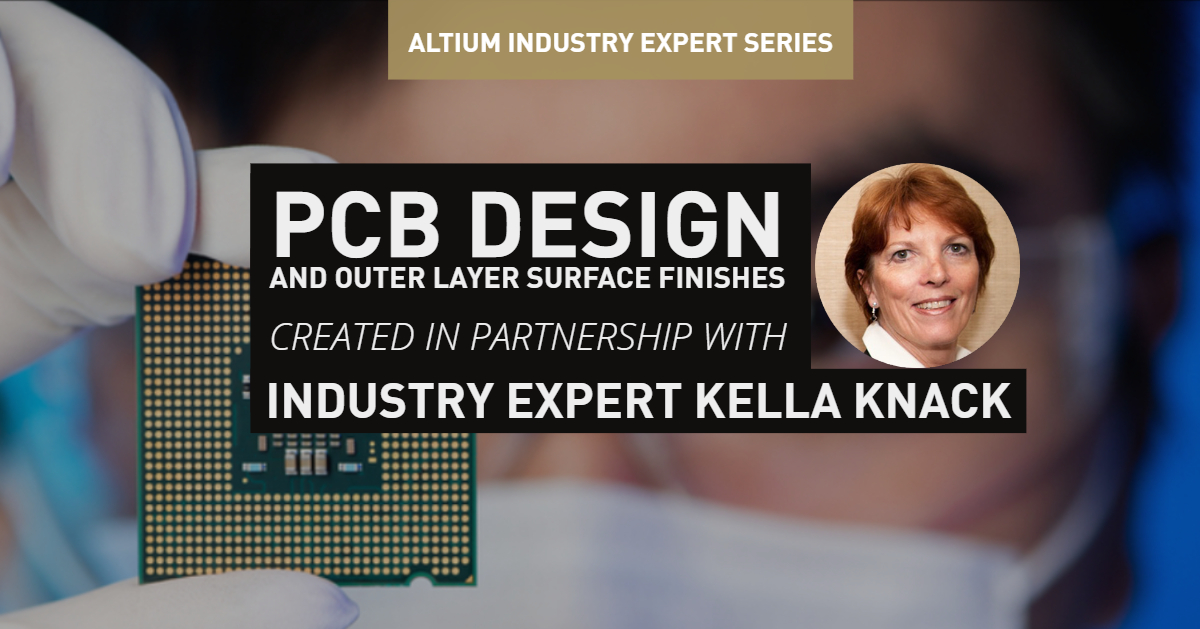
Bien qu’il soit très en aval en termes de développement de produits, le choix de la finition de surface de la couche extérieure du PCB doit être déterminé dès le début du processus de conception du PCB. Il existe une variété de finitions de surface de la couche extérieure et presque toutes offrent des avantages et des inconvénients. Le choix de la finition la mieux adaptée à votre conception particulière dépend principalement de l'application finale de votre produit. Cet article décrit les différentes classes de surfaces disponibles ; leur histoire et leur évolution ; leurs avantages et leurs inconvénients individuels ; pendant quelle étape de la fabrication du PCB l’application de la surface particulière est-elle réalisée, et la situation actuelle dans le contexte industriel.
Il est judicieux de poser la question : "Quel est le rapport entre la finition de la surface et ma conception à grande vitesse ? La réponse pourrait être "aucun" mais, au fil des ans, nous avons vu des dizaines, voire des centaines ou plus de conceptions à grande vitesse élégamment exécutées, mais qui ont échoué parce que la fiabilité des connexions de soudure dépendait en fait d’une mauvaise finition de surface. Dans ce cas, la seule solution est de jeter tout l'assemblage et de recommencer à zéro. Les coûts peuvent devenir énormes, avec ralentissement du projet, retard du produit fini, incapacité à atteindre la fenêtre de lancement sur le marché et à générer les revenus attendus.
Le but de toute finition de surface de la couche extérieure - quel que soit le type et l'endroit où elle est appliquée pendant le processus global de fabrication - est de protéger les surfaces en cuivre contre la corrosion sur les zones de soudage des composants.
- Soudure électrolytique
- Étain électrolytique
- HASL
- ENTEC 106® ou autre protection organique
- ENIG
- ENPIG
- Or électrolytique ou nickel électrolytique
- Étain d'immersion
- Argent d'immersion
Il est important de noter que l'application de ces finitions de surface sur la couche extérieure intervient pendant différentes phases
du processus de fabrication des PCB. En outre, le lieu où se déroule la procédure d’application a un impact direct sur l’efficacité de chaque finition. Ces deux phases différentes incluent :
Dans ce cas, le placage sert de réserve de gravure lorsqu'il est temps d'enlever le cuivre indésirable sur les couches extérieures. Dans cette catégorie, les finitions comprennent la soudure électrolytique, l'étain électrolytique et l'or électrolytique sur nickel.
Dans ce cas, la soudure plaqué ou l'étain plaqué est utilisé comme réserve pour la gravure des couches extérieures. Ce placage est enlevé avant l'application du masque de soudure, laissant le cuivre exposé sur les zones où les connexions de soudure doivent être réalisées. Ces finitions de surface de la couche extérieure sont composées de matériaux anticorrosifs qui protègent les pastilles de montage pendant le soudage. Des informations sur leur utilisation sont ajoutées ci-dessous. Dans cette catégorie, les finitions spécifiques incluent le HASL, les revêtements organiques tels que l’ENTEC 106, ENIG, ENEPIG, l'étain d'immersion et l'argent d'immersion.
Ces finitions ont connu l’évolution suivante :
- La soudure électrolytique est la finition de surface originale utilisée par l'industrie des PCB. C'est la finition la moins coûteuse car elle permet d'effectuer deux tâches en une seule opération. D'abord, elle est utilisée comme réserve de gravure. Elle sert également à protéger les surfaces de cuivre sur lesquelles les composants seront soudés. Le problème est que le masque de soudure appliqué sur cette finition peut se rompre lorsque la soudure des pistes sous ce masque se met à fondre pendant la soudage à la vague. Cela provoque donc des courts-circuits entre les pistes. En outre, cette finition contient une part excessive de plomb. Elle a donc été remplacée par la version suivante.
- L'étain électrolytique a ensuite été choisi comme remplacement RoHS, au lieu de la soudure électrolytique. L'intérêt de cette finition est que le masque de soudure peut être appliqué directement sur l'étain comme finition de surface finale. Cette méthode a été testée sur plusieurs produits, incluant des fonds de panier, avec des résultats mitigés. Le problème est que l'étain pur, ainsi que certains alliages d'étain, développent de très petites barbes d'étain entre des circuits de tensions différentes. Lorsque les barbes se forment, elles provoquent des courts-circuits et des lignes de fuite. Ces barbes apparaissent généralement quelque temps après l'assemblage du PCB et entre les mains de l'utilisateur, ce qui provoque un retour externe. C'est pourquoi toute forme d'étain comme finition de surface n'est pas un choix fiable pour la mise en œuvre des PCB.
- Le SMBOC (masque de soudure sur cuivre nu) est un procédé qui a été développé pour résoudre le problème des courts-circuits de soudure. Dans ce cas, on élimine la soudure ou l'étain sur les pistes avant d’appliquer le masque de soudure. Comme le masque de soudure adhère très bien au cuivre nu, il résout le problème des courts-circuits de soudure. Cependant, il laisse les pastilles de montage exposées et le cuivre nu se corrode très rapidement. Par conséquent, un matériau anticorrosif est nécessaire pour protéger les pastilles de montage en cuivre. Ces matériaux anticorrosifs sont listés ci-dessus et de plus amples informations à leur sujet sont incluses.
- L'or électrolytique sur nickel électrolytique comme finition de surface est aussi ancien, sinon plus, que la soudure électrolytique. Les avantages de cette finition incluent sa facilité de métallisation, sa protection des surfaces en cuivre et son esthétique. Cependant, comme il s'agit de la finition la plus coûteuse à utiliser, nous ne l'utilisons que sur les PCB haut de gamme. Toutefois, elle présente quelques risques mineurs. Lorsque cette finition est utilisée sur des PCB qui présentent de petits trous, avec un rapport d'aspect élevé, un problème apparaît pendant le processus de gravure qui sert à éliminer le cuivre indésirable sur les couches extérieures du PCB. Le nickel et l'or protègent le cuivre présent dans les trous traversants plaqués et évitent son élimination pendant la gravure. Si le processus utilisé pour déposer le nickel n'est pas parfaitement contrôlé, le cuivre au centre des trous traversants ne sera pas recouvert, et il sera donc éliminé par la gravure. Ce n'est pas un problème si le cuivre est complètement gravé, puisque le circuit ouvert est facile à détecter. La carte peut être immédiatement rejetée. Cependant, de petites quantités de cuivre peuvent rester dans le trou, ce qui suffit à passer les tests de la carte nue. Mais après le processus de soudure, des ruptures interviennent souvent au niveau du cuivre et ruinent le PCB. Plusieurs solutions sont possibles : la première consiste à plaquer du cuivre supplémentaire dans les trous pour contrer les effets du processus de gravure. La seconde consiste à boucher les vias sur le dessus et le dessous du PCB avec un matériau photosensible avant de graver les couches extérieures.
Comme indiqué ci-dessus, les finitions suivantes sont appliquées après la métallisation intégrale du circuit imprimé et après la gravure du motif final sur les couches extérieures et l’application du masque de soudure. Dans cette catégorie, les finitions incluent :
- Le HASL (nivelage de brasure à l'air chaud) a été la première finition développée pour les PCB SMOBC et elle reste la meilleure finition pour ce type. Elle est aussi la plus économique, après la soudure plaquée. Le HASL est réalisé en immergeant le PCB SMOBC fini dans une cuve de soudure fondue pour recouvrir tout le cuivre exposé. Le PCB est extrait du bain de soudure en passant à travers deux lames d’air qui évacuent l'excédent de soudure, laissant suffisamment de soudure sur chaque pastille pour assurer la protection contre la corrosion. L'inconvénient de cette finition est que la hauteur des pastilles de soudure n'est pas uniforme, si bien que les QFP et les BGA à pas fin accumulent les problèmes de courts-circuits de soudure ou de circuits ouverts. De plus, avec le HASL, chaque PCB subit un choc thermique sévère lorsqu'il est immergé dans la soudure fondue. Si les PCB sont épais et comptent un grand nombre de petits trous traversants plaqués, un certain nombre de trous peuvent devenir défectueux.
- L’ENTEC 106® ou les revêtements organiques sont de fines pellicules de substances organiques qui protègent les pastilles de cuivre jusqu'à l’étape du soudage, pendant lequel ils fonctionnent comme un flux de soudure. L'un des avantages de l'ENTEC est qu'il est peu coûteux par rapport à d’autres choix de finition pour la couche extérieure. Mais le simple fait de le toucher avec les doigts détruit le revêtement. Le PCB devient inutilisable jusqu'à ce que le revêtement soit décapé et réappliqué. Par conséquent, l’ENTEC et autres revêtements similaires ne conviennent pas aux prototypes de produits qui sont plus susceptibles d'être manipulés avec les doigts. Cette finition est néanmoins adaptée pour fabriquer des PCB.
- L'ENIG (dépôt autocatalytique de nickel sous immersion d’or) peut être un bon revêtement s'il est appliqué correctement. Les termes "autocatalytique" et "immersion" indiquent que le nickel et l'or doivent être déposés sur le cuivre sans utiliser l'électricité. Le problème est que cette finition est appliquée avec deux bains chimiques complexes. Si la chimie n'est pas parfaitement contrôlée, une pastille noire sera le seul résultat. Ce matériau affaiblit les soudures et se rompt souvent à la fin des opérations de soudage. Malheureusement, il n'y a pas de solution à ce problème et les montages entiers doivent être mis au rebut. Un autre inconvénient de l'ENIG est que la couche d'or appliquée est si fine qu'elle n'offre pas de protection anticorrosion à long terme. Les cartes n'ont alors aucune durée de conservation.
- L'ENEPIG (dépôt autocatalytique de nickel et dépôt autocatalytique de palladium sous immersion d’or) existe depuis une dizaine d'années et a été présenté comme un remplacement approprié de l'ENIG. Il rencontre aussi des problèmes similaires d'exposition à la corrosion et de pastilles noires. Nous avons constaté les effets de ces deux types de problèmes et nous ne pouvons pas recommander cette finition.
- L'immersion d’étain a initialement présenté certains avantages. Comme elle ne contient pas de plomb, elle répond aux exigences de la directive RoHS. Elle est aussi très facile à appliquer. Mais, comme nous l'avons déjà mentionné, l'étain produit des barbes qui provoquent lentement des courts-circuits ou des lignes de fuites, c'est pourquoi nous ne recommandons pas de l’utiliser comme finition de surface. L'immersion d’argent est la finition de choix si vous ne pouvez pas vous permettre les coûts de l'or électrolytique sur nickel électrolytique. Elle a une longue durée de vie et elle est aussi économique que l'ENTEC. Le seul problème, c'est qu'elle devient noire (ternissement). Toutefois, il s'agit seulement d'une question esthétique sans impact sur la performance. Par conséquent, certains fabricants OEM ont commencé à utiliser ENTEC sur tous les points de soudure, puis ENIG sur les pastilles qui seront exposées après l'assemblage. Les cartes sont donc plus "jolies". Leur fonctionnement répond aux attentes et leur apparence satisfait les clients.
Résumé
L'industrie dispose d'un certain nombre de finitions de surface de la couche extérieure. Il est indispensable de comprendre la dynamique,
les avantages et les inconvénients de chacune d’entre elles pour être certain que la finition choisie sera la bonne
pour vos PCB. La prise en compte de ces facteurs, dès la phase de conception, protègera
l'ensemble du processus de développement de votre produit contre les défaillances pendant toutes les
opérations de conception, de fabrication et d'assemblage.
Souhaitez-vous en savoir plus sur Altium et les avantages qu’il peut vous apporter pour concevoir votre prochain projet de circuits imprimés ? Discutez avec un expert Altium ou lisez ce Guide de la conception des PCB à haut débit pour avoir un aperçu sur tout ce que vous devez savoir. Pour en savoir plus sur les questions abordées dans cet article, vous pouvez également lire les documents référencés ci-dessous.
Références
- Ritchey, Lee W. and Zasio, John J., “Right The First Time, A Practical Handbook on High-Speed PCB and System Design, Volume 2.”
- Ritchey, Lee W., “Update on PCB Surface Finishes,” Current Source Newsletter, Volume 1, Issue 4, August 2005
___
For conclusions/CTAs: