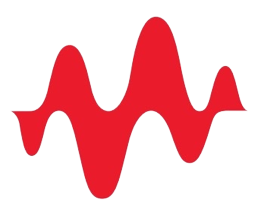
Better thermal efficiency, how to do better power efficiency, how to reduce losses, how to help people handle those thermal losses? This episode is a real treat.
Our guest Steven Schnier, Systems Engineer for Power Management at Texas Instruments generously shares the different strategies for designing better thermal and power efficient PCB.
Watch through the end, this episode is sure have great tips and strategies that you don’t want to miss.
Listen to this Episode:
Watch this episode:
Show Highlights:
Links and Resources:
Transcription:
Steven Schnier:
And typically, like you said, you do a DC-to-DC converter. Then you have an LDO with a fairly significant dropout, say 300 millivolts to 500 millivolt dropout. And then you have that going into your supply rail. That dropout does help you get the noise immunity that you need and the lower ripple and lower noise, but it also means that you're now, say if you're a 2 amp rail at 500 millivolts, that's a considerable amount of wattage that you're dropping there.
Zach Peterson:
Hello, everyone and welcome to the Altium OnTrack Podcast. I'm your host, Zach Peterson. Today we're talking with Steven Schnier, Systems Engineer for Power Management at Texas Instruments. Those of you who have watched the show for some time probably know that we don't get to talk to semiconductor folks that often, so I think this is a real treat. Steven, thank you so much for joining us.
Steven Schnier:
Thank you.
Zach Peterson:
So we often talk a lot about signal integrity, power integrity, EMI, those kinds of things, but we don't often talk about power. So it's interesting that you're here to talk about power management and power products, and I think one of the things that you wanted to bring up was some of the things that are going on with TI as far as power products are concerned.
Steven Schnier:
Yeah, absolutely. So one of our big focuses recently has been how to do better thermal efficiency, how to do better power efficiency, how to reduce losses, how to help people handle those thermal losses. And so that's been a variety of different things through package technology, through better processes, lower RDS on for FETs, enabling higher switching frequencies and so forth. And recently, we've developed a few products that actually help you get low noise and low ripple with a buck converter that allow you to get rid of an LDO, which is typically one of the places where, especially for noise sensitive designs, you have a lot of thermal and power loss.
Zach Peterson:
With the LDO, it's a pretty common strategy to go from your line in to mid-range, step down, maybe 12 or 5 volts, and then one more step down maybe with another buck converter, and then maybe another step down with an LDO. So you've got a lot of different power stages in there just to get to low voltage with reasonable efficiency and not a huge amount of noise. So I think someone might look at this and say, "Hey, we might want to eliminate a buck converter," but you're saying "No, let's eliminate the LDO and do better at the buck converter."
Steven Schnier:
Yeah, actually, it really depends on your duty cycle, how large of a step down you need, because sometimes you run into practical concerns like minimum on time. So if you want to do high switching frequency for smaller size inductors, then now you have a minimum on time that you can hit. Say you're doing 15 volts input to 1 volt output running at 1 or 2 megahertz, that's going to be a limitation. But typically, you don't need an LDO in a lot of power rails, because not all power rails are noise sensitive. So if you're doing a digital input into a microprocessor, for example, that core rail, the very high-current rail, is typically going to be pretty noise immune.
And you can check that out by doing a PSRR measurement on it and just see if it has a pretty good 40, 60, 80 dB rejection of whatever input noise you have. Then you're pretty noise immune. But a lot of analog front ends, ADCs, DACs, clocking devices, oscillators, PLLs and so forth, they're going to have a less noise immunity and you're going to need a clean power supply on that input. And typically, like you said, you do a DC-to-DC converter, then you have an LDO with a fairly significant dropout, say 300 millivolts to 500 millivolt dropout. And then you have that going into your supply rail.
That dropout does help you get the noise immunity that you need and the lower ripple and lower noise. But it also means that you're now, say if you're a 2 amp rail at 500 millivolts, that's a considerable amount of wattage that you're dropping there.
Zach Peterson:
So a couple of things here. Eliminating the LDO, I think in some cases that's totally warranted, because I've noticed in some data sheets that there is actually an LDO already built into the chip that you're powering. But is there any noise that's actually generated by the LDO or is the only issue thermal?
Steven Schnier:
Okay, so that internal LDO, that makes it easier for a customer to use that part. But let's say that the semiconductor vendor like us, for example, doesn't want to put that LDO internal to our design because that actually increases the power loss in our device as well. So that makes now a thermal issue in our device. So the ideal thing would be is to get rid of the LDO altogether. And it really depends on how much noise reduction you need. So an LDO, a low-noise LDO, can be anywhere from 20 microvolt RMS noise from say 10 hertz to a hundred kilohertz down to the latest one that we have, the TPS A92 I think it is. That one is a half a microvolt RMS from 10 hertz to a hundred kilohertz. So that's extremely low noise.
Now, for the type of product I'm talking about, a switching regulator that gives you low noise, it's going to be more towards the end of the 15 to 20 microvolt RMS figure and not the super low noise. However, if you have a low-noise switcher and you still need that super low noise, you could have that ultra low-noise LDO follow the switcher. And you don't have to have as high of dropout to get the same performance. So you're saving your power loss that way. So you can go from 500 millivolts down to 300 millivolts. Well, that's a three-fifth savings in power loss. A two-fifth savings, sorry.
Zach Peterson:
Yeah, so in these kinds of applications, where you're eliminating some of that power loss, this is where you're really starting to try and supply power to a lot of different, let's say, digital inputs as well as some of these other things that might be on a board. You mentioned ADCs would be a good example. I've had to deal with this actually in an RF system where it's pulling a lot of current, and in addition to the power amplifier itself, the LDO was probably the second hottest component on the board.
Steven Schnier:
Absolutely. And keep in mind that the LDO does not solve all your noise issues. There's still the 1/f noise that any device will do, but the LDO does have very stable performance over that low frequency range. That's where the noise is. 10 hertz to a hundred kilohertz is typically there. And these new products from TI, we actually co-opt one of the techniques where they have a noise reduction soft start cap to stabilize the band gap of the LDO. We adopt that into these switchers so the noise performance is pretty much adequate and relative to the same performance you get for that typical low noise LDO.
Zach Peterson:
So you brought up something awe about the LDO specification as far as the noise bandwidth that's covered by an LDO. You said it goes up to about a hundred kilohertz, let's say. I think here is a place where maybe a designer might unintentionally have a mismatch between what their buck converter needs to do and where the LDO is capable of suppressing noise. Because sometimes it's seen as LDO is a cheap noise suppression mechanism, but if it only operates up to a hundred kilohertz and your buck converter is, let's say, switching at half a megahertz, are you really doing anything from the noise from your buck converter?
Steven Schnier:
So that's where there's a little bit of a terminology difference. So there's low noise, which is the lower end of the spectrum, up to say a hundred kilohertz. Then there's what we call ripple, which is typically at the switching frequency, and then multiples of that, which could be anywhere, 10 megahertz, a few, maybe up to a hundred megahertz, that that's where your ripple and your harmonics will come in. And then what you have higher than that is EMI. And EMI is your hundred megahertz and above. Then you start looking at CSPR requirements and so forth. So if you look at those three things and people use noise to describe all three of those ranges. So yes, the LDO is actually a good filter for higher frequency ripple as well as the noise.
It doesn't generate the noise at the low end. It's good at filtering out that low noise as well as the ripple at the switching frequency. But now, if you can reduce the ripple at the switching frequency, that's another very good benefit. And you can do that in a lot of different ways. You don't need necessarily a special part to do that. There's a lot of techniques that you can do from board layout techniques, where you basically cancel current loops to bypass caps, where you minimize the input ripple of your power supply so that you're not amplifying that on the output, to filter caps. So there's three terminal filter caps that are very good at suppressing noise.
To the most common way that people suppress noise across a wide range noise, meaning both the low frequency noise as well as the switching frequency noise or switching frequency ripple is a ferrite bead filter, and that ferrite bead filter allows you to really squelch that ripple at the switching frequency and above.
Zach Peterson:
You brought up ferrite beads, which sometimes in the Altium audience is like dropping a nuke on a conversation. But maybe go more into the use of the ferrites, because that can be a contentious issue among people who do SIPI and then people who are doing power supplies. I think maybe those two groups talk past each other a little bit. So maybe go more into the use of ferrites and when it's really appropriate and what type of systems you might want to target with a ferrite.
Steven Schnier:
So I haven't found a place. It's like the magic solution that handles your input ripple. It handles your output ripple. But there are some things that you have to be careful with where you introduce that ferrite bead filter. That ferrite bead is basically a very small inductor, say 10 nanohenry or somewhere around that range with a cap and you're essentially creating a pie filter. Then that kills the noise at a certain frequency. But if you have that LC filter placed with the wrong corner frequency, you can actually interfere with the primary regulation of your DC-to-DC converter and cause some instability. So you do have to be very careful with how you're placing it, what the ratio is to your primary bulk caps on your DC-to-DC converter, as well as that LC filter with the ferrite bead.
One nice thing about some of these new parts that TI has is we have the integrated ferrite bead filter compensation in the device. So we actually have two sense points with the device. We have the VO sense point, which is at the primary LC filter of your switching converter. And then we have a feedback sensing point with that resistor divider for your output regulation. So that's really your DC regulation. And those two compensation loops internally are spaced far enough of part as far as their poles and zeros so that they don't interfere with each other. You get the AC, fast AC response, and then you also get the good DC regulation to compensate for that drop across the ferrite bead and give you good DC performance.
Zach Peterson:
So when you mentioned you could potentially introduce instability, maybe if you're doing this from discrete components and you do this on your own and maybe misselect the cap or the ferrite. So when you say introduce instability, I think that means introducing a new pole in the transfer function for a circuit?
Steven Schnier:
That's a double pole.
Zach Peterson:
A double pole. Okay.
Steven Schnier:
Yeah and in-
Zach Peterson:
So that's-
Steven Schnier:
I'm sorry.
Zach Peterson:
Oh, so that's because you basically form a second order filter with the cap plus the ferrite and then another cap.
Steven Schnier:
Absolutely. And there's a good resource. Last year for part of the power supply design seminars from TI, we wrote an application note that gives you some of the pros and cons of ferrite bead filters and also a design methodology about how to go about doing this with a standard buck converter that typically only has one feedback sense point and the choices you have to make. You can either regulate before the ferrite bead filter, which then you take that instability out of the way. Or you can regulate after the ferrite bead filter, which gives you better DC regulation. But now you need to make sure that you're designing so that you're not causing instability. And there you may need some dampening circuits or you may need some other things to adjust for that.
Zach Peterson:
So I like adding damping. It's a really simple solution. And if you don't mind losing just a little bit of efficiency, I don't think it's too much of a problem. So where would you add damping in that pie circuit that you might be putting on the output of that buck converter?
Steven Schnier:
Right before the ferrite bead filter. So right at your bulk cap of the primary DC-to-DC converter.
Zach Peterson:
So just in series with the bulk cap?
Steven Schnier:
Right, exactly.
Zach Peterson:
Yeah. Okay. But then that increases your turn on time a little bit.
Steven Schnier:
Yeah, there's always trade-offs with everything that you've done here. Just some of the basic standard techniques of lowering your output voltage ripple can also cause transient response issues, can cause load regulation issues. There's no free lunch.
Zach Peterson:
Sure. So with the load regulation, I guess the issue would be you have a switching current moving out of the buck regulator and then through this filter circuit. But that excites a transient. And essentially, the feedback loop is trying to compensate for this transient that you excite unintentionally.
Steven Schnier:
Well, it's not the transient. It's just really the IR loss through the ferrite bead, because that ferrite bead is not resistorless. So you have a drop across that. And if you have the sense point of your feedback after that drop, well, then now your on time can compensate for that. If it's before then, now you have a drop that is totally dependent upon the output current, whatever your load is. So if you have a heavier load, your output and voltage is going to droop a little based on that resistance.
Zach Peterson:
That makes sense, because you brought up that ferrites are like an inductor, and I think most people think of ferrites in that way and then forget about the resistance.
Steven Schnier:
Exactly. Whenever you buy a cap, you also get an inductor. And that's actually what causes some of the output voltage ripple as well. So if you're trying to reduce output voltage ripple, one common board layout technique, and the schematic/layout technique, is just add a bunch of caps in parallel. Because that paralleling the caps, you can use smaller values of caps, get the same effective capacitance. But now you're doing a bunch of inductances. That parasitic inductance on each cap reduces based on the number of times. So the number of times you have the cap there. So it's a one 1/L, you're dividing the inductance by the number of caps you have. So that helps reduce the ripple caused by that parasitic inductance.
Zach Peterson:
That's a good point. And I see that recommendation in some data sheets come up and you bring up a good point. I think sometimes folks don't know why that's done on what is ostensibly supposed to be a DC regulator. We talk about it a lot in terms of power integrity for a large processor, where maybe you put a bunch of caps in parallel in order to hit your capacitance target. But like you brought up, also prevent moving that pole to a lower frequency. And so you can do the same thing on a buck converter.
Steven Schnier:
Yep, absolutely.
Zach Peterson:
Okay. So what are some of the other reasons for maybe using a ferrite bead on these systems? And I bring this up because there is always a debate among the high-speed community about using a ferrite bead somewhere in the PDN, whether it's part of the buck converter or somewhere else in the PDN, maybe downstream from a series of caps or for isolation. Doing it on the buck converter sounds like a big advantage. Do you see the same advantage for digital systems? Or do the digital systems not really worry about this. It's more about where you put that ferrite elsewhere in the system that creates problems?
Steven Schnier:
Yeah, so digitals, power supplies, are fairly noise immune, so I wouldn't worry about that too much. You still may have ferrite beads all over the place because of EMI concerns, and crosstalk concerns, and transmission line effects when you have large buses and that kind of stuff, where they may be sprinkled all over the board. And so actually, some of the low-noise, low-ripple techniques that we're using, we're just taking advantage of a component that is being used for other purposes. It's really there because of EMI or because of something else. And it's been on the LDO output forever. We're just using that same ferrite bead in order to now do double duty as killing the noise and the output ripple.
Zach Peterson:
So if you were going to do some of this design work and maybe you put together a prototype, you've done some of the strategies that we've talked about here with TIS's products or with other products, which measurements would you need to perform to determine whether your supply is, I guess, objectively noisy? I put that in air quotes, because noisy is a relative term. But how exactly would you quantify that and what targets should you really go for?
Steven Schnier:
There's two aspects to it. One, I would look at what am I powering? And are the different power supplies on that device noise sensitive or not? So I would start with, say you have a VDA11 and a VDD11, so you have a digital and an analog 1.1 volt rail. Do a power supply rejection ratio where you're running through putting an input signal at a certain level on those pins and then measure your output and see how much of it shows up. And if you get 20 dB of drop between your input and your output, then you know that that's not very noise immune. It's actually going to pretty much propagate and mucks into your device anything you put on that input. So I'd be very sensitive about what type of power supply I put on there. And so that's where typically people have thrown an LDO on there.
Now, if you want to see what kind of power supply do you need in order to satisfy those noise sensitive inputs, do a couple basic measurements. A real easy one is a noise spectral density. So you use a signal analyzer to do basically the same thing. You put an input wave or input signal from DC from ground all the way up to a hundred kilohertz or a megahertz and see what kind of noise comes through there. And then you would measure that. That's basically a power measurement. Then you integrate under that curve to get your effective noise, which when I say 20 microvolt RMS, that's an integrated value from say, a hundred hertz to a hundred kilohertz. You can also do spot noise to say exactly what it is at a specific frequency.
And in most cases, if you look at an LDO, you'll see that curve on the power supply to begin with. If you look at most DC-to-DC converters, you will not see that curve. Most of the time that is not something anybody publishes, because if you need a noise-sensitive supply, they're typically going to put an LDO, that's where you're going to put an LDO after it. But there are a few components that do have that noise curve, that noise spectral density, actually in the data sheet. So a TPS62913 or a module equivalent, the TPSM82913, those devices have the noise curves in there.
The other thing I would look at is the ripple voltage. So if you look at the output ripple of a DC-to-DC converter, if it's 5 or 10 millivolts peak-to-peak, that's probably not going to cut it for some noise-sensitive device. Typically, that's going to be 1 millivolt or below. There are devices, again, like the same TPS62913 or TPSM82913, those devices have that integrated ferrite bead filter compensation that allow you to put that ferrite bead filter on there and give you about a 30 dB drop. So say your output voltage ripple is right at 1 millivolt or 2 millivolts peak-to-peak, with that ferrite bead filter you're now down into the 20-microvolt RMS or 10-microvolt RMS output ripple.
And in order to measure that, you can't use a standard scope, because in the time domain, that output ripple is going to be basically the noise floor of your scope. It's going to look like you have no signal on it whatsoever. So you need to go get a good signal analyzer like an FSW8 or something equivalent in order to do that FFT measurement. And you can see then the frequency components of the output ripple. And even in that case on some of these devices, you have to have a really low-noise floor to even see the output ripple, which is exactly the case you want. If you can't hardly measure it, your noise sensitive device is not going to see it and be affected by it.
Zach Peterson:
That's a good point. Now, when you say low-noise applications, you brought up ADCs earlier. And I think the main area where that applies is if you were going to use, let's say, the output from a buck converter, which most people that I think wouldn't do this, but they would use a output from a buck converter to maybe bring it into the reference voltage or to the analog interface, power the analog side. Are those the kind of applications you might consider with an ADC to be appropriate for these products that you're talking about from TI?
Steven Schnier:
Yeah, so there's a wide variety. So ADCs could be in radio applications and radar applications. And then if you want to take the ADC and add clocking and some other stuff where we call them AFEs, analog front ends, those go into wireless infrastructure, active antenna arrays, baseband units, test and measurement devices where you're doing a lot of these things together and aerospace and defense applications where you're doing telemetry, you're doing high-speed measuring LiDAR applications. There's quite a few different applications where it's high-precision or high-speed data measurement that you need.
Zach Peterson:
Radar is one of the ones I would've brought up and shout out to TI's radar portfolio. I use them pretty often.
Steven Schnier:
Pretty good.
Zach Peterson:
So another possible topology that I have seen discussed in a couple of different contexts we brought up on this talk is multi-phase converters. So I know that some VRMs are multi-phase. And I've seen multi-phase discussed in the context of RF. So why would someone maybe use one of your products instead of let's say, somebody else's multi-phase converter?
Steven Schnier:
So typically, multi-phase is at a current level above a certain amount. You typically won't see multi-phase at 3 amps. And typically, multi-phase is also directly towards a high transient requirement type application processor power, FPGA power, the core rail. Typically, it's also lower output voltage, where you have a ton of current, a low output voltage and you need low ripple for that because the percentage ripple when you get down into 0.75 volts or 0.6 volts, a few hundred or a tens of millivolts of ripple is a significant percentage of that output voltage.
So in that case, by using multi-phase converter running at say, 1 megahertz, say you have four phases, that's a 4 megahertz equivalent device. So transient responses get better. Your output ripple gets better. Now, you do have more expensive components because you have 4 inductors. You have 4 output filters. But you get the benefit of having that multi-phase controller there.
Zach Peterson:
So it's really a footprint issue and then not suitable for every single application is, I guess, you could summarize. Okay.
Steven Schnier:
Absolutely. I would find it hard pressed to find a modern day processor that isn't using a multi-phase supply.
Zach Peterson:
Well, I think it makes sense for the issue you brought up, because the core voltage keeps going down. And then, it's not just the noise margin is staying fixed, the noise margin is also going down as well. So you can't just scale down the noise voltage, or the core voltage, and then expect the noise requirement to scale down by the same factor. It actually scales down further.
Steven Schnier:
That's right, absolutely.
Zach Peterson:
And then if you were going to try and do a module for a multi-phase converter, those can look pretty complex too. When you've got multiple switchers, all lined up in parallel, they all have to be phased out correctly.
Steven Schnier:
And load share and, I mean, and timing. There's a lot of interleaving. And then there's also other complexity, like if you do have high-load demand and then you have a very light-load behavior, how you do load shedding or phase shedding in order to not have a high quest and current as those phases shed. So one size doesn't fit all. I would say for a single phase converter up to let's say, 50 amps probably makes sense. But when you're starting to scale up higher than that, then multi-phase. I don't think you're going to find many single-phase converters higher than that.
Zach Peterson:
It also sounds like once you get to those levels, there's a big efficiency issue just within the converter itself as well. And so by spreading it across multiple switchers, now those switchers can handle higher current, they have more time to cool off. So on average, they're receiving less current.
Steven Schnier:
And typically the truly low-noise rails that I'm talking about would be 10 amps or below. You're not going to throw an LDO, I mean, there there's hardly any 5-amp LDOs out there. And so maybe you put a couple in parallel. Now you're looking at a really large footprint. When you're looking at core processor voltage, you're definitely not throwing LDOs on there. So you have to come up with that ripple solution some other way. And multi-phase is a great way to do it.
Zach Peterson:
Okay. Those are great points. So there's one other thing that you mentioned that I haven't asked yet, but it is related to TI products. You had mentioned that you have some of these products in TPS series, and I've used quite a few of them in designs, TPS62, Triple X, something like that. You also mentioned that there are module equivalents. And I think folks who may use some components from another semiconductor company, that is well known for its power modules, are aware of this, but I think most designers aren't aware that sometimes these regulators come in a module equivalent. So maybe tell us a little bit more. What are some of those module equivalent products?
Steven Schnier:
So actually, this is something that we've been expanding recently over time. We have some great packaging technology. We have open frame. We have overmolded. We have lead frame based. We have substrate based. We have a wide variety of modules that fit different end applications. We have some that go into consumer electronics that are super low cost. We have some that are more full-featured, high power modules. But if you look at TPSM as typically what you would start with or you can go onto TI.com and just search our module portfolio and you might be surprised at how many we have. And we're developing more and more all the time.
So this low noise converter, we have a 2 and a 3-amp discrete, and then we have a 2 and a 3-amp module version. And the module basically takes the discrete device, puts on some of the passives around it, has the inductor integrated into it. So all you have to do is lay down whatever output cap you want on there. And in this case, the ferrite bead filter, because that ferrite bead filter is typically close to the load of whatever you're doing so you can route that around wherever you want, because we have the remote sense through that ferrite, that feedback resistor divider, that can be right at the load.
And so that makes the whole design quite a bit simpler. Plus sourcing, a little bit simpler. You don't need to source the controller, converter, power stage inductor, all that kind of stuff. You just do the module and your output cap.
Zach Peterson:
So that gets to what I was going to ask next, which was, what's one of the advantages of a module? A module literally integrates as much as possible right into the package.
Steven Schnier:
Yep. It's the minimum viable set of components that everybody would need. And then the customization would be how much bulk cap do you need on your particular device? And then you can also still set externally, switching frequency, or some specific configuration features. On many of our products we have internal compensation, so you don't need to compensate except for say, a set 1 resistor that selects multiple different things. Does it have a load discharge feature? Does it have the switching frequency? Does it have an internal or external sync capability? Those kind of things.
Zach Peterson:
So it sounds like if you were to just go with one of these modules, you're going to get a much smaller footprint because you could eliminate some of those discretes and they're just put right into the package.
Steven Schnier:
Well, it's not just the discretes. But typically, when you lay out components, everybody has their board rules on how close components can be. Then you have silkscreen rules. Then you have probing and testing and all that kind of stuff. When you put it into a module, you're going to get 20 to 30% space savings, because we're doing our own rules. We do all the testing. We do the reliability to make sure that all these components work together. And you don't have to go by those board layout rules.
Zach Peterson:
Okay. Those are all great points. And then what's the footprint or the landing pad arrangement? Is it BGA?
Steven Schnier:
Yeah. It basically looks like your standard QFN. So there could be some power pads in the middle with some pins around the outside.
Zach Peterson:
Okay. I have seen them in BGAs. Is there an advantage to doing it in a QFN?
Steven Schnier:
No, it just depends on what exactly you're doing there. The BGAs would be for a certain style of product. I think it really comes down to, what product are you basing it on to begin with? And then how you're making it as well. Because we have some that are lead frame based, some are FR4 based. There's different variety of flexibility you have in creating the modules based on what the initial product is, as well as what the structure of the module is.
Zach Peterson:
And I think maybe a QFN is going to be easier for routing in on maybe a lower layer count board, so you don't need to have additional layers internally if you don't need them just to route into the BGA.
Steven Schnier:
Right. I can tell you my particular product group, I don't think we're doing anything but QFN. So it just makes it simple.
Zach Peterson:
That's true. I would agree. It does make it a lot simpler, for sure. Well, we're running out of time, but I think with these last few minutes I wanted to ask you, what else can you share about what might be coming out in terms of power products from ti?
Steven Schnier:
Boy, that's an open-ended question. We're always going with higher power density, so expect more progress on that. Lately, we're doing more PIN-compatible type devices, so to help with some of the supply concerns that customers have. So you can expect more of that. Innovation in features and control topologies to get better transient response with lower output cap. That's a ever-changing battle to make sure that people don't need a huge bulk cap in order to have a stable supply based on the load transients. But just a lot of innovation and keeping track of the market. And we're always working with customers on what their next problem is and trying to anticipate what products we make for those.
Zach Peterson:
Well, those all sound very interesting and I think very important. But I will say kudos on the PIN compatibility, because I mean, when something goes out of stock and you got to find something to replace it last minute, you always hope it's PIN compatible and sometimes it's hard to find it. So kudos on that one.
Steven Schnier:
All right. Thanks.
Zach Peterson:
Thank you for joining us. To everyone that's been watching today on YouTube and listening, we've been talking with Steven Schnier, Systems Engineer for Power Management from Texas Instruments. If you're watching on YouTube, make sure to hit that subscribe button. You'll be able to keep up with all of our episodes and tutorials as they come out. Also, make sure to check the show notes. We'll have some great links there where you can learn more about TI's Power Product Portfolio. And you'll be able to see some of the products that we've talked about in this podcast episode. And last but not least, don't stop learning. Stay on track and we'll see you next time.