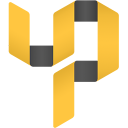
When it comes to electronics, consumer devices like smartphones and Alexa tend to get all the attention. However, according to Alun Morgan at Ventec International Group, “about 23% of PCBs produced worldwide are used in electronics equipment for manufacturing applications.” The numbers only go up when you include other non-consumer categories that support manufacturing operations, such as automotive, telecom, power generation/distribution, and computing. Western manufacturers have largely accepted that onshoring will only occur through greater automation and productivity on the factory floor. This is the essence of Industry 4.0, where factory operations are more intelligent and more connected than ever before.
So where can manufacturers continue to cut expenses and see greater productivity benefits through onshoring? There are a number of answers to this question, especially when you consider advanced manufacturing technologies like 3D printing. One thing everyone agrees on is this: manufacturing operations for many products will be further digitized in the near future. This level of digitization requires PCBs to run equipment and gather data, as well as technology to quickly process data and gain useful insights. In Industry 4.0, artificial intelligence (AI) will be instrumental to managing operations and processing data, ultimately providing insights to managers and engineers.
Designing a new AI system to support manufacturing operations is as much a hardware endeavor as it is about software. Both areas complement each other; an embedded board must be designed to support the embedded software, while the embedded software should not be so resource-consuming as to cripple other functions on the board. This means every manufacturing asset and the systems that support data acquisition/process will become an embedded IoT ecosystem, where data is processed at a central location or in the cloud.
In Industry 4.0, manufacturers are expected to generate significantly more data than ever before as more manufacturing assets become connected. This connectivity is enabled through new industry standards for data exchange, such as the IPC-CFX standard. Any manufacturing operation that wants to connect its assets and aggregate data throughout any manufacturing process will need a wealth of embedded IoT devices throughout a factory.
New embedded IoT devices can support AI applications if they meet some basic hardware requirements. These embedded devices are specialized single-board computers that can support standard AI/ML models while enabling communication of data over standard protocols. Here are some basic requirements to consider when designing new systems for Industry 4.0 manufacturing operations:
Cutting costs and increasing productivity is all about getting a new system deployed and configured quickly. Most manufacturing engineers are not printed circuit designers, but this critical class of engineers can quickly create new AI products for manufacturing operations by taking a modular approach to electronics design. This class of design features allows any systems designer to connect computing, sensing, and communications interfaces together into a custom system for AI applications in manufacturing.
These tools take advantage of standard computing interfaces and the standardized electrical connections between them. Computer-on-modules (COMs), systems-on-module (SoMs), and other hardware for AI applications on the factory floor can be connected on a custom board in a modular fashion. Some options for SBCs and COMs to consider using on the factory floor are shown in the following table:
|
|
|
|
|
|
|
|
|
|
|
|
|
|
|
|
|
|
Industry standard EDA tools can help designers quickly layout new boards with standard layout and routing features, but not all engineers in this space are specialists with EDA software. Using a modular design platform like the Upverter Board Builder allows anyone from an embedded software developer to AI entrepreneurs to build data-intensive AI applications in less time.
In the Upverter design platform, a designer can easily connect together modules graphically in a web-based interface. There are no tools to download and install, and there are plenty of standardized modules available within the platform. This allows you to quickly build out a new Industry 4.0 artificial intelligence product using any of the above AI hardware platforms and quickly take it to manufacturing.
The modular electronics design tools in Upverter (previously known as Geppetto) give you access to a broad range of industry-standard COMs and popular modules, allowing you to create production-grade hardware for Industry 4.0 artificial intelligence applications. You can also easily build new products in a matter of minutes. If your system needs additional functionality, you can include wireless connectivity, an array of sensors, high resolution cameras, and a number of standard COMs.
Take a look at some Gumstix customer success stories or contact us today to learn more about our products, design tools, and services.