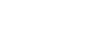
As your printed circuit board operates, power dissipation in active components causes the junction temperature to increase, and heat begins flowing from your components into your conductors and your substrate. PCB substrate materials tend to have low thermal conductivity, causing thermal problems like hot spots and high temperature in your PCB. Keeping the temperature of your components below their rated maximum requires thermal heat dissipation techniques that help aid heat conduction away from hot areas of your printed circuit board.
Active and passive thermal heat dissipation techniques are designed with the same goal in mind: remove heat from components and dissipate it into the surrounding air, or dissipate it into a portion of the board with lower temperature. Passive heat management takes advantage of natural phenomenon where heat moves to cooler regions of space and does not require input energy to achieve heat transport. Active thermal management techniques provide more aggressive means of carrying heat away from a circuit board during operation. You often don’t need to choose between active and passive thermal design techniques; you can implement both in a design if you need a more aggressive cooling strategy.
Each working component will act as a heat source, and it is unavoidable that the temperature of your board will increase during operation. As a result, you need to have a strategy to remove heat from active components and spread it throughout your circuit board in order to keep your component temperatures within acceptable limits.
A heat sink is one of the most common passive cooling methods for active devices like high-speed processors, MCUs, FGPAs, and other devices. These components generate significant heat, and the low thermal conductivity of most circuit board substrate materials will cause heat to accumulate in the substrate below these components. As the substrate expands, conductive traces and vias in the substrate can experience significant stress. If a board is repeatedly cycled between extreme temperatures, thinner traces can delaminate from the substrate, and the next in vias can crack under extreme stress. This is particularly common in printed boards that use small diameter unfilled vias with a high aspect ratio.
Any heat sink should be mounted to a component with a thermal pad or thermal paste. Both mounting techniques take advantage of the low thermal resistance of the heat sink and the pad/paste material. This aids heat conduction away from the component and into the heat sink, where heat can be dissipated into the surrounding air. Placing a heat sink on active components that generate significant heat is an important part of any passive cooling strategy, although this may create problems with keeping a small footprint.
Thermal paste for a CPU heat sink
Judicious design and placement of thermal vias will help keep junction temperature in active components low during operation. Thermal vias are placed below active components and can be soldered to the die-attached pad on the bottom of an integrated circuit. These vias will span through the circuit board substrate, and they can be filled with a low thermal resistance epoxy to conduct heat away from the component in question. You can ground your thermal vias to provide a direct connection to an interior copper plane, which provides a low thermal resistance path for heat dissipation to cooler areas of the board.
Thermal vias in this QFN pad arrangement can draw heat from the semiconductor die and transfer it into an internal copper ground plane.
Your layer stack plays an important role in providing passive heat conduction away from active components. Copper planes in the internal layers of your layer stack will provide a low thermal resistance path for heat away from active components. When thermal vias are combined with the proper layer stack design, you can increase the effective thermal of your PCB substrate near components and help keep component temperatures from exceeding your design limits.
Thermal design for your layer stack in Altium Designer
Ceramic and metallic substrates have higher thermal conductivity (i.e., lower thermal resistance) than FR4 and other laminates. Once heat does leave an active component and conduct into your substrate, a substrate with higher thermal conductivity will allow heat to quickly move to cooler regions of the circuit board. This helps ensure that your PCB has a more uniform temperature distribution and helps to eliminate thermal hot spots beneath active components.
Using ceramics is desirable in high-temperature applications as a ceramic PCB material can have a thermal conductivity value that is a factor 20 to 100 larger than that of standard FR4 and similar laminates. These boards are also mechanically stronger than FR4, making them useful for high-power electromechanical applications in high-temperature environments.
A metal core PCB is especially useful in applications that run at high power, such as LED arrays and power electronics. The metal core provides the same function as a substrate material with a high thermal conductivity; it provides a low thermal resistance path for heat to conduct to regions of the board with low temperature. The metal core provides much lower thermal resistance than interior copper layers because the metal core is generally thicker. One great example is an aluminum core PCB, which offers high thermal conductivity at low cost.
Aluminum circuit board as part of thermal design for a multi-board system
A more sophisticated approach is to embed large pieces of copper into a cavity between copper layers in the PCB stack-up. This involves fabricating a cavity, followed by completely filling and plating it with copper using a standard deposition process. The resulting copper slug, sometimes referred to as a "copper coin," provides a very low thermal resistance path for heat dissipation away from specific components on the circuit board.
To place a copper slug, the designer must first place a copper cavity definition on an internal layer. Copper slugs can be grounded, so they can be grown from a ground plane and into a signal layer. The design rules for the fabricated cavity structure in terms of routing and drilling of nearby vias are the same as you would have for a board outline. Observe the same tolerances and ensure you account for edge clearances if you do not want the copper slug to connect to a particular layer.
To learn more about placement on these cavities, watch the video below.
Typically, a copper coin can be placed between L2 and L3 in the PCB stackup. This allows a component on L1 that generates a lot of heat to dissipate that heat into the copper coin and then into a connected plane. However, the copper coin needs to be close to the component to be most effective, which requires a thin outer layer.
Some devices can leverage the thermal mass of an enclosure to cool components efficiently. Enclosures can be large and bulky, often secured with metal fasteners that fix the PCB in place. These metal regions can serve as pathways to dissipate heat from the PCB if designed correctly. As with many systems, this requires close collaboration with a mechanical designer to create a contact method that draws heat into the enclosure.
There are a few ways to design this contact method:
In certain instances, all three of these methods can be employed on the same PCB. They can also be utilized in conjunction with fans and more substantial heat sinks to facilitate temperature management.
In certain designs, when an exposed copper rail is visible, it is often assumed to serve the purpose of connecting to a shielded enclosure. However, as illustrated in the board below, it can also fulfill thermal transport functions.
The placement of these rails in your PCB design software follows the same rules you would apply to a chassis ground, which is essentially what these rails are. Chassis grounding provides the additional benefit of heat dissipation, but only when the contact method is combined with a fastening method as I mentioned above. This could involve multiple points of contact with metal fasteners to create a highly conductive path for heat.
There are certainly a few other cooling PCB techniques than the ones I’ll mention here. However, these are some of the most chilling schemes.
Conduction and Radiation/Heat Spreaders - Where convection involves heat transfer in fluids, radiation and conduction deal with solids. Heat spreaders normally are not the backbone of your thermal resistance management, but instead, augment it. Basically, any piece of metal acts as a heat spreader since it will conduct thermal energy. To best use conduction and radiation, you should try to direct as much heat as possible to the outside layers of your board and to the enclosure, where it can be radiated more efficiently.
Heat Exchangers - Heat exchangers are often used in conventional AC units. They use a refrigerant and a vaporization/condensation cycle to transfer heat from one area to another. In PCBs, there are two main types of heat exchangers: heat pipes and cold plates. The main difference between these is the form factor; heat pipes are thin and cold plates are wide. This kind of system can be very small, and it transfers heat efficiently. It also has a low chance of failure since it is a self-contained system with no mechanical.
Droplet Cooling - This experimental kind of cooling involves the same kind of process found in heat exchangers. The main difference is that the fluid in heat exchangers travels a relatively long distance horizontally, whereas here the fluid travels a short distance vertically. The nice thing about this system is that it automatically reacts to hotspots that can form integrated circuits (ICs). In addition, it can conduct and radiate thermal energy like a heat spreader for power dissipation, but with greater effect, because it can conduct in both the horizontal and vertical directions.
A simple way to add active cooling to a system is with an electric fan that directs airflow through the passive portion of the system. For exmaple, high power components like FPGAs and microprocessors may combine a heat sink with a cooling fan. More aggressive active cooling methods include liquid cooling, where a fluid flows past hot components and conducts heat to a radiator. Even more aggressive is an evaporative heat exchanger, which dissipates heat by inducing a phase change in a fluid within a closed system. The latter method is used in highly overclocked PCs and is popular among gamers.
Heat exchanger with electric cooling fan and heat sink
Before you can implement heat management strategies in your PCB design software, you need to account for the placement of active and passive thermal dissipation components, as well as design the enclosure for your product.
Altium Designer’s unified design platform offers a complete experience which takes users from concept to finished product. For thermal design, users can connect to an MCAD application which allows collaboration with a mechanical engineer, something which is essential when implementing a thermal management strategy. Altium Designer users can also export their layout data into standard modeling formats for use in simulation applications so that a heat management strategy can be validated before prototype testing.
Whether you need to build reliable power electronics or advanced digital systems, use the complete set of PCB design features and world-class CAD tools in Altium Designer®. To implement collaboration in today’s cross-disciplinary environment, innovative companies are using the Altium 365™ platform to easily share design data and put projects into manufacturing.
We have only scratched the surface of what’s possible with Altium Designer on Altium 365. Start your free trial of Altium Designer + Altium 365 today.