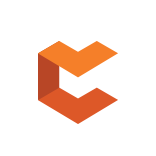
Magnetism allows you to do some really cool things—especially when electrons move through a magnetic field. One device that uses the deflection of electron motion for sensing is a Hall effect sensor. These little devices are used in automotive, manufacturing, consumer electronics, and other industries. The Hall effect basically allows a magnetic field to be sensed, which offers several possible applications.
Some of the possible applications include sensing motion and proximity of magnetized objects through a direct measurement of the magnetic field. I've done a couple projects where a sensor was needed to measure whether a lid or shutter had closed completely; a Hall effect sensor provided a nice solution by adding a magnet to the case. But how exactly do these devices work, and how does this affect the design? Keep reading to learn more about these unique devices.
A Hall effect sensor takes advantage of, as its name implies, the Hall effect, which can occur in a metal or semiconductor. This effect relies on the basic interaction between an electron and a magnetic field. Any electrically charged object moving in a direction perpendicular to a magnetic field experience the Lorentz force. This force is responsible for producing the electrical signal that would be measured across the body of the device.
This force causes charged particles (electrons and holes in a high-mobility semiconductor like GaAs, or electrons in metals) to be deflected when they pass through a magnetic field, with the direction determined by a right-hand rule. The Hall effect applies the same ideas to semiconductors, causing charge to accumulate along one side of the conductor creates an electric field that counteracts the force of the magnetic field. The transverse Lorentz force pushes the electrons to follow a curved path along and to one side of the semiconductor. Then, the right-hand rule tells us that the direction of the Lorentz force has a relationship with the direction of the electrons.
Placing some output connections perpendicular to the direction of current flow forms a Hall element. A difference in potential exists between the positive upper side and the negative side of the conductor. With that difference in potential, a measurable voltage—called the Hall voltage—occurs.
While the direction of the applied magnetic field determines the polarity of the Hall voltage, the voltage remains proportional to the applied field strength. Take away the magnetic field, and the current stops being deflected while the potential difference across the output drops to zero. At this point, the different influences on the voltage become interesting. The Hall voltage depends on the:
Each of those factors impact semiconductors influenced by the Hall effect. Placing a current-carrying silicon chip at a right angle to a magnetic field produces the low-level Hall voltage. The Hall voltage is a function of the input current.
When applied to semiconductors, the Hall effect creates a digital switch that produces an efficient on-off square wave signal. Disrupting the window between the magnetic field and the silicon chip produces a zero output. Connecting additional circuitry to the semiconductor produces the opposite effect and allows the interruption to the magnetic field to produce an increase in output voltage.
Hall effect sensors require a low noise, moderate gain amplifier to amplify the 30 µV Hall voltage and the addition of a regulator to hold current constant. The amplified output voltage of the Hall effect sensor occurs only as a function of the magnetic field. With all this, a Hall effect switch works as an ideal Hall sensor (thanks to the output voltage).
Digital Hall effect sensors sense the magnetic field and switches state when the sensor reaches the operating point. Decreasing the magnetic field until the magnetic sensor reaches its release point causes the Hall effect sensor to return to its original state. The fundamental points for designing Hall effect sensors include:
Different types of Hall effect sensors integrate into PCB design and include a vane operated position sensor, gear tooth sensor, digital current sensor, linear current sensor, latches, closed loop current sensor, unipolar switches, and mechanically-operated switches.
While Hall effect sensors can be a powerful tool within your PCB design, the first step when approaching any PCB design will always be in knowing what kind of PCB design software to use and which software has the right tools for your needs. When you need to access an easy-to-use PCB layout tool that includes everything needed to build high-quality manufacturable circuit boards, look no further than CircuitMaker. In addition to easy-to-use PCB design software, all CircuitMaker users have access to a personal workspace on the Altium 365 platform. You can upload and store your design data in the cloud, and you can easily view your projects via your web browser in a secure platform.
Start using CircuitMaker today and stay tuned for the new CircuitMaker Pro from Altium.