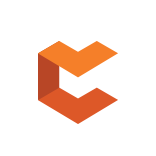
Have you ever gone out to a well-reviewed, luxurious restaurant for dinner? I’m sure you paid a pretty penny for it. However, if fine dining is a passion of yours and you enjoyed it then it’s worth the expense. On the other hand, it’s hard not to feel silly paying $20 more than you’re supposed to for a sandwich at an average local restaurant. In this situation, you’re much better off putting that money towards cooking lessons and becoming your own chef.
As an electronics designer, I’ve had similar experiences with programmable logic controllers (PLCs) and localized embedded systems. So what is the difference between PLC and embedded system? You can achieve significant cost reduction by replacing PLCs with localized embedded systems. However, much like those times when your dining experience is worth every dollar, I’ve also learned that there are scenarios where an embedded PLC, the more expensive option, is the better choice.
A programmable logic controller is a specialized, industrial, embedded computer. It is custom programmed to monitor input signals (digital or analog), perform logical operations, and trigger specific output signals. This embedded controller is known to be rugged and is commonly used in extreme industrial environments or applications that have almost no room for failure.
Let us take a moment to compare a soft PLC and a microcontroller, as they do have some significant differences. PLCs are popular because of their modular structure. This makes them easy to install in a plug-and-play manner. At their most basic, they consist of a central processing unit (CPU), a power supply, and input/output (I/O) modules. Programming PLCs is less complicated than coding a microcontroller. This is because it revolves around ladder logic diagrams, functional block diagrams, and structured text on software provided by the manufacturers, which is not the case in a microcontroller.
PLCs are not strangers to industrial applications. They are commonly used in production lines, road traffic signals, escalators, and HVAC systems. They’re capable of basic data manipulation and support various communication protocols like Modbus, and DeviceNet. This has made them a preferred option in automated control systems.
PLC installation is mostly plug-and-play.
In general, an embedded PLC system is defined as a dedicated set of hardware and software working together to provide application-specific functionality. From an electronic designer’s point of view, it consists of a microcontroller (MCU), memory chips, power management circuits, communication modules, and input/output functionality.
This might sound similar to a PLC system, but there are distinct differences between them.
Configuration: PLCs are known to be modular and easily replaceable if a specific module fails. On the other hand, embedded PLC systems are mostly designed as a single board. This reduces their cost.
Programming: PLC programming is generally less time-consuming since they come with easy-to-understand ladder logic diagrams. However, embedded PLC systems are coded in a high-level programming language, like C, and their firmware takes longer to write.
Cost: PLC systems are associated with having a high cost, especially when they are from reputable manufacturers. Alternatively, an embedded system, when localized, has a very low production cost per unit.
Despite the differences in hardware build-ups and programming methods, an embedded system can easily replicate a PLC’s functions. During the course of my freelancing career, I’ve helped clients in various industries replace industrial PLCs with localized embedded systems. This was for one reason only, cost. In certain applications, a localized embedded system can cost as little as 20% of a branded PLC. In business, that translates into a healthy profit margin while still achieving the same functionality.
Technical support is critical regardless of whether you choose a PLC or an embedded system
You might be wondering why we aren’t all switching over to embedded systems. Cost is always a consideration, but it is a mistake to automatically prefer a localized embedded system for cost alone. There are times when it is best to stick with using a PLC despite the fact that it can significantly increase your expenses. Here are some factors that make the cost of PLCs worthwhile.
Volume: Unless you’re working on a project that requires hundreds of PLCs with the same setup, it can be more cost-effective to purchase a commercial off-the-shelf PLC. The costs in a time of developing a localized embedded system and manufacturing its setup might not be worthwhile.
Certification: In certain industrial applications, there are requirements for the electronics control system to be certified by standard organizations. Branded PLCs usually came with CE, UL, and other certifications. If the cost of certifying your own embedded system outweighs the cost of the PLC, then it’s better to stick with the latter option.
Support: PLCs often come with support from a reputable company. If you’re outsourcing the manufacturing of your localized embedded system to a contractor, make sure that you’ll receive a decent amount of technical support. Otherwise, it’s better to stay safe with PLC.
Reliability: If your intended application involves your control systems operating in harsh electrical and physical environments, it is often better to go with a PLC that is already proven to work in these environments. Unless you’re set on developing localized embedded systems for these conditions and have budgeted to do so, there’s a good chance that they won’t have sufficient lab testing.
At the end of the day, the choice of whether you should opt for a PLC PCB or a localized embedded system goes beyond financial considerations. In practice, your choice will be situational. In situations where an embedded system is preferential, look no further than CircuitMaker for an easy-to-use PCB layout tool that includes everything needed to build high-quality manufacturable circuit boards. All CircuitMaker users also have access to a personal workspace on the Altium 365 platform. You can upload and store your design data in the cloud, and you can easily view your projects via your web browser in a secure platform.
Start using CircuitMaker today and stay tuned for the new CircuitMaker Pro from Altium.