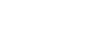
Khi nói đến công nghệ, chúng ta không bao giờ nhìn lại phía sau. Đôi khi, có vẻ như công nghệ cũ không bao giờ lỗi thời. Một ví dụ có thể thấy trong công nghệ lắp đặt qua lỗ mạ cho các linh kiện điện tử của bạn; loại linh kiện di sản này dường như vẫn tồn tại đến ngày nay, ngay cả khi các thiết kế mới đòi hỏi các linh kiện nhỏ hơn.
Nhưng thực sự có đơn giản như vậy không? Tại sao sử dụng công nghệ qua lỗ trên bảng mạch in (PCB) khi có vẻ như các linh kiện công nghệ gắn mặt (SMT) nhỏ hơn và cho phép đặt linh kiện gọn gàng hơn trên PCB của bạn? Như hầu hết các quyết định thiết kế, có những sự đánh đổi khi sử dụng từng loại linh kiện. Để bắt đầu, hãy cùng nhanh chóng tìm hiểu về công nghệ lắp đặt qua lỗ mạ và công nghệ gắn mặt liên quan đến quy trình thiết kế bảng mạch in PCB.
Giống như tất cả các linh kiện khác, linh kiện mạch in có lỗ xuyên qua (plated through hole circuit board components) cũng có thể được chia thành hai loại cơ bản: linh kiện chủ động và linh kiện bị động. Mỗi loại linh kiện được lắp đặt lên bảng mạch theo cùng một cách. Người thiết kế cần phải đặt các lỗ xuyên qua trên bố cục PCB của họ, nơi mà các lỗ được bao quanh bởi một pad trên lớp bề mặt để hàn. Quy trình lắp đặt xuyên lỗ rất đơn giản: đặt chân linh kiện vào các lỗ và hàn chân linh kiện lộ ra với pad. Linh kiện mạch in có lỗ xuyên qua được làm to và chắc chắn đến mức chúng có thể dễ dàng được hàn bằng tay. Đối với các linh kiện bị động xuyên lỗ, chân linh kiện có thể khá dài, vì vậy chúng thường được cắt ngắn lại trước khi lắp đặt.
Linh kiện xuyên lỗ bị động có hai loại bao bì có thể có: radial và axial. Một linh kiện xuyên lỗ axial có các chân điện chạy dọc theo trục đối xứng của linh kiện. Hãy nghĩ về một điện trở cơ bản; các chân điện chạy dọc theo trục trụ của điện trở. Diode, cuộn cảm, và nhiều tụ điện được lắp đặt theo cùng một cách. Không phải tất cả các linh kiện xuyên lỗ đều có bao bì hình trụ; một số linh kiện, như điện trở công suất cao, có bao bì hình chữ nhật với một dây dẫn chạy dọc theo chiều dài của bao bì.
Góc nhìn bên của một linh kiện gắn qua lỗ trục.
Trong khi đó, các linh kiện hướng tâm có chân dẫn điện nhô ra từ một đầu của linh kiện. Nhiều tụ điện lớn dùng điện phân thường được đóng gói theo cách này, cho phép chúng được gắn vào bảng mạch bằng cách chạy chân dẫn qua một lỗ pad trong khi chiếm ít không gian hơn trên bảng mạch. Các linh kiện khác như công tắc, LED, rơ le nhỏ và cầu chì được đóng gói như các linh kiện hướng tâm gắn qua lỗ.
Tụ điện hướng tâm (trái) và trục (phải).
Nếu bạn nhớ lại các lớp học điện tử của mình, bạn có thể nhớ về các mạch tích hợp mà bạn đã sử dụng với gói đôi hàng song song (DIP) hoặc gói DIP bằng nhựa (PDIP). Những linh kiện này thường được thấy được gắn trên bảng mạch thử nghiệm cho việc phát triển ý tưởng ban đầu, nhưng chúng cũng thường xuyên được sử dụng trong các PCB thực tế. Gói DIP phổ biến cho các thành phần hoạt động qua lỗ như gói op-amp, bộ điều chỉnh điện áp công suất thấp, và nhiều linh kiện phổ thông khác. Các thành phần khác như transistor, bộ điều chỉnh điện áp công suất cao hơn, bộ dao động thạch anh, LED công suất cao hơn, và nhiều linh kiện khác có thể đến trong gói zig-zag hàng song song (ZIP) hoặc gói vỏ transistor (TO). Giống như công nghệ lỗ thông qua chủ động dạng trục hoặc dạng bánh xe, những gói khác này cũng được gắn vào PCB theo cùng một cách.
Các linh kiện qua lỗ xuất hiện vào thời điểm mà các nhà thiết kế quan tâm nhiều hơn đến việc làm cho hệ thống điện tử có độ ổn định cơ khí và ít quan tâm hơn đến thẩm mỹ và tính toàn vẹn của tín hiệu. Việc giảm không gian chiếm dụng bởi các linh kiện không được chú trọng, và vấn đề về tính toàn vẹn tín hiệu không được coi là mối quan tâm. Sau này, khi mức tiêu thụ điện năng, tính toàn vẹn tín hiệu và yêu cầu về không gian bảng mạch bắt đầu trở thành tâm điểm, các nhà thiết kế cần sử dụng các linh kiện cung cấp cùng một chức năng điện tử trong một gói nhỏ hơn. Đây là nơi mà các linh kiện gắn mặt xuất hiện.
Nếu bạn nhìn vào bất kỳ thiết kế PCB hiện đại nào, bạn sẽ thấy các bảng mạch chủ yếu được chiếm dụng bởi các linh kiện gắn mặt. Các thiết kế mới vẫn sử dụng các linh kiện qua lỗ, nhưng những linh kiện này thường được sử dụng nhiều hơn trong điện tử công suất và các thiết bị khác phát ra nhiều nhiệt. Công nghệ gắn mặt là công nghệ đóng gói linh kiện được sử dụng phổ biến nhất hiện nay. Các loại linh kiện này không sử dụng chân cắm cho các dẫn điện. Thay vào đó, các dẫn xuất hiện dưới dạng các miếng đệm kim loại nhỏ trên cùng một mặt của linh kiện. Mục đích chính của các miếng đệm này là để cho phép hàn trực tiếp lên bề mặt của PCB trong quá trình lắp ráp.
Việc sử dụng các pad trong công nghệ gắn mặt so với công nghệ xuyên lỗ mang lại một số lợi ích nhất định, sẽ được thảo luận dưới đây. Ngoài ra, kích thước pad nhỏ hơn và kích thước tổng thể của linh kiện nhỏ hơn khiến cho các linh kiện này có các thành phần parasitic kém nổi bật hơn. Điều này cho phép chúng hoạt động ở tốc độ/tần số cao hơn trước khi bạn bắt đầu nhận thấy vấn đề về tính toàn vẹn tín hiệu.
Nếu bạn nhớ về chiếc PC cũ của mình, có lẽ bạn sẽ nhớ về các bộ vi xử lý Pentium với hàng loạt chân ở phía dưới của gói sản phẩm. Loại bao bì này được gọi là mảng chân cắm (PGA), tương tự như gói bao bì mảng chân đất (LGA) hiện đại hơn. Một linh kiện PGA có thể trông giống như một linh kiện xuyên lỗ, nhưng nó không được hàn vào các lỗ trên bảng mạch. Thay vào đó, nó được cắm vào một gói gắn mặt được hàn lên bảng mạch. Điều này cho phép linh kiện PGA dễ dàng được thay thế hoặc nâng cấp nếu cần.
Các linh kiện gắn mặt thường nhỏ hơn so với linh kiện thông qua lỗ tương đương. Tuy nhiên, điều này không nhất thiết có nghĩa là chi phí của một linh kiện gắn mặt luôn rẻ hơn chỉ vì sử dụng ít nguyên liệu thô hơn trong quá trình sản xuất các linh kiện này. Chính bản thân các linh kiện gắn mặt có thể có giá tương tự như một linh kiện thông qua lỗ tương đương. Tuy nhiên, một khi xem xét chi phí lắp ráp tự động cho mỗi linh kiện, tổng chi phí cho mỗi linh kiện gắn mặt thường rẻ hơn so với một linh kiện thông qua lỗ với cùng giá trị linh kiện, đánh giá công suất/điện áp và dung sai.
Sự khác biệt này xuất phát từ việc đặt linh kiện thông qua lỗ đòi hỏi phải khoan lỗ trên PCB của bạn, điều này gây ra chi phí dụng cụ. Ngược lại, không cần khoan khi sử dụng linh kiện gắn mặt, điều này giải thích cho sự chênh lệch chi phí. Tất cả điều này đặt ra câu hỏi: nếu linh kiện gắn mặt nhỏ hơn, nhanh hơn và rẻ hơn, thì tại sao lại sử dụng công nghệ gắn qua lỗ chút nào? Câu trả lời phụ thuộc vào trường hợp sử dụng thiết kế PCB của bạn. Có, công nghệ PCB thông qua lỗ là cũ, to và đắt, nhưng cũng có một số ưu điểm.
ƯU ĐIỂM |
NHƯỢC ĐIỂM |
Dễ dàng cho việc chế tạo mẫu |
Chi phí bảng mạch cao hơn do khoan |
Kết nối vật lý mạnh mẽ |
Chiếm nhiều diện tích bảng mạch hơn |
Khả năng chịu nhiệt |
Quy trình lắp ráp PCB phức tạp hơn |
Khả năng xử lý công suất |
Tốc độ chậm hơn |
ƯU ĐIỂM |
NHƯỢC ĐIỂM |
Kích thước nhỏ → Bảng mạch dày đặc hơn |
Kết nối vật lý yếu hơn với PCB |
Giảm parasitics → Đáng tin cậy ở tốc độ cao hơn |
Khả năng chịu nhiệt thấp hơn |
Lắp ráp nhanh hơn & rẻ hơn |
Khả năng xử lý công suất thấp hơn |
Không cần khoan → Chi phí sản xuất bảng mạch rẻ hơn |
DFM: tombstone, pop cornering, v.v. |
Khi so sánh hai công nghệ thiết kế PCB, dễ dàng thấy tại sao gắn bề mặt lại là nhà vô địch. Các thành phần gắn bề mặt nhỏ hơn, rẻ hơn và có thể chạy ở tốc độ cao hơn. Điều này đặc biệt quan trọng trong các ứng dụng tín hiệu hỗn hợp và chứa nhiều tín hiệu tương tự sắp tới như thiết bị IoT, thiết bị không dây mới và thiết bị đeo được. Khi tốc độ mạng tăng và các thiết bị mới hoạt động ở tốc độ dữ liệu cao hơn, các thành phần gắn bề mặt sẽ tiếp tục xuất hiện vì chúng nói chung không thể thay thế cho các thành phần xuyên lỗ.
Vấn đề với các thành phần qua lỗ và các thành phần nhiễu xạ được tạo ra trong bố cục PCB tạo ra thách thức cho các sản phẩm ô tô, hàng không vũ trụ và quân sự cần phải rất bền vững nhưng cũng cần hoạt động xa vào băng tần GHz. Có nhiều thách thức nơi mà một thành phần qua lỗ có thể tạo ra mất mát chèn lớn hơn dọc theo kết nối tại tần số mmWave. Tuy nhiên, các thành phần qua lỗ được ưa chuộng trong các ứng dụng này vì điểm hàn ít có khả năng hỏng hóc trong quá trình hoạt động. Vẫn còn rất nhiều sự đổi mới có thể xảy ra trong lĩnh vực này.
Các nhà lãnh đạo công nghệ cũng đang hướng tới một xã hội kết nối, và kích thước quan trọng khi nói đến thiết kế PCB. Trong nỗ lực cho tính toàn diện của máy tính, IoT, hay “trí tuệ phủ quanh” mà chúng ta đều khao khát, việc làm cho các thành phần nhỏ hơn bao gồm cả bảng mạch. Các thành phần nhỏ hơn cho phép bảng mạch nhỏ hơn, cho phép chúng ta xây dựng bảng mạch in gần như ở bất kỳ hình dạng nào. Kích thước nhỏ hơn có nghĩa là chi phí sản xuất thấp hơn. Các thành phần và bảng mạch rẻ hơn mang lại tiết kiệm chi phí cho khách hàng cuối cùng.
Công nghệ gắn qua lỗ rất tốt cho việc chế tạo mẫu và kiểm tra vì bạn có thể dễ dàng thay thế các thành phần trên bảng mạch in. Ngay cả trước khi bạn thiết kế bảng mạch của mình, bạn có thể lắp ráp thiết kế của mình với công nghệ qua lỗ.
Ngoài việc chế tạo mẫu và kiểm tra, các linh kiện xuyên lỗ còn có liên kết vật lý rất mạnh với bảng mạch do chúng được hàn từ cả hai mặt trên và dưới của bảng mạch. Điều này làm cho các bảng mạch sử dụng công nghệ gắn kết xuyên lỗ rất bền bỉ, đó là một phần lý do tại sao chúng được sử dụng trong quân sự và hàng không vũ trụ. Chúng cũng có khả năng chịu nhiệt độ cao. Bạn có thể tìm thấy công nghệ xuyên lỗ ở nhiều nơi. Một ví dụ là trên các bóng đèn LED trong bảng quảng cáo hoặc sân vận động. Các LED xuyên lỗ cực kỳ sáng và bền bỉ, cho phép chúng chịu đựng được các yếu tố bên ngoài.
Nếu bạn nhìn vào các máy móc và thiết bị công nghiệp, bạn có thể tìm thấy nhiều bảng mạch được xây dựng gần như hoàn toàn bằng các linh kiện xuyên lỗ. Một lần nữa, điều này là do điều kiện hoạt động khắc nghiệt, như cực đoan của nhiệt độ hoặc các tình huống liên quan đến tiêu thụ năng lượng cao. Công nghệ xuyên lỗ có thể cũ và có vẻ lỗi thời, nhưng nó có một mục đích và có thể được sử dụng vì độ bền và sức mạnh vật lý của nó trong thế giới kết nối ngày nay.
Các linh kiện xuyên lỗ trong một nguồn cung cấp điện
Altium Designer trên Altium 365 mang lại một lượng tích hợp chưa từng có cho ngành công nghiệp điện tử, trước đây chỉ giới hạn trong lĩnh vực phát triển phần mềm, cho phép các nhà thiết kế làm việc từ xa và đạt được mức độ hiệu quả chưa từng có.
Chúng ta mới chỉ khám phá bề nổi của những gì có thể thực hiện với Altium Designer trên Altium 365. Bạn có thể kiểm tra trang sản phẩm để biết thêm mô tả tính năng chi tiết hơn hoặc một trong những Hội thảo Trực tuyến Theo yêu cầu.
Bạn muốn tìm hiểu thêm? Hãy truy cập blog hướng dẫn thiết kế PCB phổ biến của chúng tôi và học hỏi từ các chuyên gia của chúng tôi.