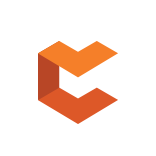
This seems to be such a basic question that always goes down a rabbit hole: when should you use an LDO vs. a buck regulator? Some important aspects of selecting an LDO compared to a switching converter are the types of components being powered, the total current drawn from the regulator, and the amount of heat these components can tolerate.
In a previous article, I looked at some of the factors that limit LDO efficiency, namely due to the construction of the component and how it responds to a high input voltage above its dropout level. With a buck converter, this is much less of a problem, but now the ON/OFF modulation rate in switching elements becomes the important point to consider. These are complex issues that relate to the structure of MOSFETs, so it’s best not to get stuck on this topic. Instead, we want to look at some cases where you’ll want to opt for a buck converter vs. an LDO as the final output stage in your power regulation strategy.
If you’re considering whether to use a buck converter or an LDO for certain portions of your system, or to power your entire board, you should think about the types of components you need to power and how much power they should consume. Here are the main points to think about when selecting regulator components and designing your circuits:
|
|
|
|
|
|
|
|
|
|
|
|
|
|
|
Each of these aspects of regulator circuits plays an important role in different types of circuits. To help make these differences clearer, let’s look at three typical systems: DC, AC (all-analog), and RF.
Working at DC is very easy as long as the input voltage you need to regulate is close to the output voltage you need from your regulator. If you’re operating in DC, or nominally at DC with digital circuits, LDOs will generally be your best choice for several reasons, but only as long as you’re operating at low current, or with minimal voltage differential above the dropout voltage. Because of the efficiency and dropout considerations I discussed in an earlier article, there are two cases where LDOs are best used:
If you’re operating an LDO outside these limits, you risk overheating the device until it fails, or you risk going out of regulation. In this case, go with a buck converter, particularly when you’re operating at high input-output differential.
For a faster digital processor, like one of the faster MSP430 or STM32 variants, you’ll have power integrity problems if you don’t use a power plane, leading to voltage fluctuations in excess of about 100 mV seen on the power rail. However, these fluctuations are generally small enough that you won’t knock the LDO out of regulation. This may change if you have multiple digital ICs in different circuit blocks all drawing large current, in which case you should separate components into different stages in parallel.
If you need to supply power to an analog circuit, an LDO is also useful as the device has low noise output. I have used an LDO up to a few W of power in DC and analog circuits, however this required adding a heatsink to the package to dissipate heat due to the high current and differential. Analog is challenging as these circuits are noise-sensitive, so an LDO would be preferred as these components typically have in excess of 50-60 dB of noise rejection on the output power. If you need to source higher power analog circuitry from a DC supply (this is not so common), a buck regulator is preferable. This is where we want to think about some of the strategies used in RF power supply designs.
RF systems like amplifiers could be powered with an LDO, although the efficiency and heating problem should be where you start to think about the design. For lower power systems, like a WiFi-enabled module (e.g., ESP32 or SimpleLink), an LDO is fine as you’re typically not running at too high power. If you can’t deal with the heating problem or you need high power for modulated signals, you’ll need to use a buck converter.
Building RF systems with a DC buck converter can be challenging. The major challenge is noise, although many RF ICs (such as an MCU with an integrated radio) will have an on-die LDO that provides regulation, so your job is to just get noise-free power to the power pins. You can use passive filtering on the output with a larger capacitor and inductor to help stabilize the DC output.
If you need to operate at high power and high frequencies while sourcing modulated signals, just know that this is a more advanced topic that requires its own article. I’ll discuss this in an upcoming blog.
If you’re using a regulated bench power supply and you’re plugging directly into a module or dev board, then you won’t need to worry about this. Bench power supply designs are specifically designed to be multifunctional and provide low switching noise through a variety of techniques (multiphase operation, higher PWM frequencies, faster edge rate PWM, large ferrites, etc.). However, when you’re ready to transition away from a prototype and build a custom board, you’ll need tools to help you build your power regulation schematics and create the PCB layout for your circuits.
Once you’ve decided on using a buck converter vs. LDO and you’re ready to create your PCB layout, you’ll have access to a complete set of layout and routing features in CircuitMaker. Users can build detailed schematics for power regulation circuits and instantly transfer their data into a new PCB layout. All CircuitMaker users also have access to a personal workspace on the Altium 365 platform, where they can upload and store design data in the cloud, and easily view projects via a web browser in a secure platform.
Start using CircuitMaker today and stay tuned for the new CircuitMaker Pro from Altium.