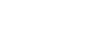
Costruire una scheda significa conformarsi al processo di fabbricazione per il vostro stack di strati e la selezione dei materiali. Ad un certo punto, dovrete progettare le connessioni sul vostro PCB, e anche queste hanno requisiti specifici intesi a garantire la fabbricabilità. In questa sezione del nostro corso intensivo su DFM, esamineremo alcune delle restrizioni DFM di base sugli elementi conduttivi in un PCB, così come lo sviluppo dei livelli di serigrafia/solder mask di superficie per DFA.
Un DFM di successo nel layout del PCB inizia impostando le regole di progettazione per tenere conto delle importanti restrizioni DFM. Le regole DFM mostrate di seguito riflettono alcune delle capacità di progettazione contemporanee che si troverebbero nella maggior parte dei produttori. Assicuratevi che i limiti impostati nelle vostre regole di progettazione del PCB non violino questi limiti, in modo da poter garantire la conformità con la maggior parte delle limitazioni di progettazione standard.
Con le selezioni dei materiali finalizzate, è ora il momento di immergersi nei dettagli specifici del layout del vostro PCB. Sebbene i flussi di lavoro ingegneristici individuali possano differire da un progettista all'altro, esistono una serie di considerazioni di progettazione primarie che necessitano di requisiti DFM precisi per considerare una scheda 100% pronta per la produzione. Nelle sezioni seguenti imparerete i dettagli specifici per strategizzare il layout del vostro PCB includendo specifiche SMT e through-hole, documentazione serigrafica, applicazioni di maschera di saldatura e altro ancora.
I progettisti professionisti utilizzano PCB multistrato con routing su due strati, il che richiede l'uso delle vie. Le vie sono una parte critica di ogni progetto di PCB e sono responsabili della trasmissione della corrente elettrica tra i vari strati. Quando si progettano vie passanti placcate, si raccomanda di mantenere un rapporto di aspetto 8:1 tra il diametro del foro e la lunghezza della via. La tabella sottostante mostra un insieme di dimensioni standard di foratura (in mils):
|
|
|
|
|
|
|
|
|
|
|
|
|
|
|
|
|
|
|
|
|
|
|
|
|
|
|
Le vie standard dovrebbero mantenere delle distanze minime dai conduttori adiacenti. La distanza dipenderà dalle specifiche capacità di lavorazione della fabbrica di produzione, così come dalla necessità di distanze specifiche richieste per certi tipi di PCB (come le schede ad alta tensione). Esiste una distanza minima tra via e via che limiterà la densità consentita di vie, con distanze tipiche da parete del foro di trapanazione a parete del foro di trapanazione che possono essere grandi fino a 10 mils. Questi requisiti limiteranno quanto densamente le connessioni possono essere instradate tra i livelli così come la densità delle vie di cucitura quando si collegano piani o poligoni.
La scelta tra componenti through-hole o dispositivi a montaggio superficiale (SMD) avrà un impatto diretto sui costi complessivi e sui tempi di produzione. Si raccomanda di optare per gli SMD per i design moderni delle schede, poiché ciò comporta tempi di realizzazione più rapidi e un'affidabilità superiore. La maggior parte dei componenti che sarebbero necessari per un design moderno sono prodotti come componenti SMD. Alcune eccezioni includono i connettori, che sono spesso disponibili sia come componenti SMD che through-hole. Per mantenere bassi i costi di produzione in un design e per garantire che siano necessari il minimo di passaggi di saldatura, è desiderabile avere il montaggio su un solo strato, anche nei casi in cui entrambi i tipi di componenti sono miscelati nello stesso tipo di design.
L'anello annulare è solitamente definito come la differenza tra il diametro desiderato del pad e il corrispondente diametro di foratura, anche se ciò non è completamente corretto. La definizione classica che ho appena menzionato si riferisce al pad di atterraggio su una via. La realtà è che l'anello annulare è piuttosto diverso dalla dimensione del pad di atterraggio della via; si riferisce all'anello di rame residuo attorno a un foro trapanato dopo che il foro è stato trapanato, inciso e rivestito di rame. Il trapano non colpisce sempre perfettamente al centro del pad a causa della deviazione durante la produzione. Il risultato è che il trapano potrebbe essere leggermente fuori centro e lascerebbe del rame attorno al foro della via.Dall'immagine sopra, possiamo vedere che la larghezza dell'anello anulare per una via perfettamente fabbricata obbedirebbe alla seguente formula:
Dall'immagine di cui sopra, possiamo vedere che la larghezza anulare di un anello perfettamente fabbricato via obbedirebbe alla seguente formula:
Larghezza Anello Anulare = (Diametro del pad – Diametro del foro) / 2
Per assicurare che la scheda sia conforme agli standard di affidabilità IPC, il diametro del pad dovrebbe essere di 8 mils (Classe IPC 2) o 10 mils (Classe IPC 3) più grande del diametro del foro di via. Questo è un limite conservativo che garantirà che ci sia quasi sempre un anello anulare intorno alla via finita.
Il rapporto d'aspetto di una via è il rapporto tra la profondità della via e il diametro del foro trapanato (dopo l'applicazione della placcatura). Il rapporto d'aspetto delle vie dovrebbe essere mantenuto abbastanza basso per garantire l'alta resa nella fabbricazione di queste strutture. Per progetti più avanzati, come i PCB HDI che utilizzano microvie, il limite del rapporto d'aspetto può essere molto piccolo, raggiungendo 1:1 o meno. Assicurati di verificare le capacità del tuo fabbricante prima di iniziare ad aggiungere vie nel layout del PCB. Puoi impostare i limiti sulle dimensioni delle vie all'interno delle regole di progettazione del tuo PCB.
Quando le densità di connessione diventano molto elevate, come in un BGA con passo fine, è possibile posizionare il via direttamente nel pad di atterraggio per un componente. Il design via-in-pad consente una collocazione ravvicinata dei componenti perché i via non devono essere posizionati a una certa distanza dal loro pad di connessione. I design via-in-pad richiedono un certo riempimento con epossidico conduttivo o non conduttivo, seguito da cappatura e placcatura per proteggere l'interno della struttura del via.
Il via-in-pad è usato con i via passanti nei casi in cui la foratura meccanica è ancora possibile, il cui limite può essere piccolo fino a 8 mils. Quando la densità dei componenti è estremamente alta, sono necessarie tecniche di progettazione HDI per realizzare connessioni agli strati interni. Questo è un argomento più avanzato che viene discusso nei nostri altri eBook.
Un via protetto è un via standard che ha i suoi strati superficiali coperti con maschera di saldatura in modo che non sia esposto rame. È tipico definire piccoli via (12 mil o meno) come protetti. I via più grandi possono richiedere una copertura e riempimento prima che possano essere protetti con maschera di saldatura. I via sono protetti per una varietà di motivi, ed è una buona idea proteggerli quando sono molto vicini ai pad di atterraggio sui componenti SMD. L'esempio sottostante mostra un'istanza in cui è necessario applicare la protezione a causa della prossimità tra i via e un gruppo di pad di saldatura su un componente SMD. In questo caso, se i via non fossero protetti, è possibile che la saldatura si diffonda attraverso questi sul retro della scheda, causando potenzialmente un cortocircuito.
Sebbene ci siano preoccupazioni di assemblaggio, può comunque esserci una ragione per lasciare i via non protetti. Ad esempio, se un via specifico è desiderabile per l'uso come punto di test, allora deve essere accessibile con una sonda, quindi la maschera di saldatura dovrà essere rimossa da quel via. I test saranno discussi più approfonditamente nel prossimo capitolo di questa serie.
Similmente ai fori passanti, i via ciechi e/o sepolti (BBV) sono fori che collegano uno o più strati. In questo processo, un via cieco collega uno strato esterno a uno o più strati interni ma non ad entrambi gli strati esterni, e un via sepolto collega uno o più strati interni, ma non a uno strato esterno. L'immagine sottostante mostra un esempio di vista in sezione trasversale di un PCB a 6 strati con via ciechi e sepolti:
Non assumere semplicemente che il tuo fabbricante sarà in grado di produrre ogni possibile combinazione di via ciechi e sepolti. I via ciechi e sepolti forati meccanicamente e forati con laser devono essere impostati su strati specifici per garantire una fabbricazione di successo, non possono essere posizionati su coppie di strati arbitrari. Assicurati di contattare prima la tua casa di fabbricazione e ottenere alcune indicazioni sull'uso dei via ciechi e sepolti in un layout di PCB.
In alcuni casi, è necessario ridurre una traccia per poterla instradare verso un pad di atterraggio per un componente. Una traccia ridotta (talvolta chiamata neck-down) si collega a un pad e corre per almeno 0,010” dal pad prima di allargarsi verso la larghezza maggiore della traccia.
Per le tracce a impedenza controllata, come quelle necessarie nei progetti ad alta velocità, generalmente non è una buona idea applicare il restringimento poiché ciò crea una deviazione dell'impedenza. Invece, utilizza strati più sottili se hai bisogno di mantenere una larghezza minore. I componenti per questi progetti tendono comunque ad avere pad di atterraggio più piccoli, quindi non avranno bisogno di restringimento se lo stackup e le tracce sono dimensionati correttamente.
Con i tuoi tipi di componenti preferiti stabiliti, è ora il momento di decidere come posizionare e orientare in modo efficiente queste parti sulla tua scheda. Questo processo avrà un grande effetto su come utilizzi lo spazio disponibile sul layout della tua scheda e può essere uno dei passaggi più sfidanti nel tuo processo di progettazione. Di seguito troverai raccomandazioni specifiche su come ottimizzare il posizionamento dei tuoi componenti per renderli sia fabbricabili sia capaci di soddisfare le tue specifiche esigenze di progettazione.
Prima di entrare nei dettagli del posizionamento e dell'orientamento dei componenti, ci sono diverse linee guida generali da tenere a mente:
Con le informazioni presentate in questo capitolo, ora sei ben attrezzato per iniziare il tuo processo di posizionamento e orientamento dei componenti per soddisfare i requisiti fondamentali di fabbricabilità. Ora che il tuo progetto è ben avviato verso il completamento, è il momento di finalizzare il processo di layout della scheda configurando i tuoi requisiti per i punti di test nel prossimo capitolo.
Quando sei pronto per iniziare il tuo progetto e vuoi assicurarti di soddisfare ogni requisito DFM per il layout del tuo PCB, utilizza le funzionalità di progettazione e layout in Altium Designer®. Una volta che il tuo progetto è pronto per una revisione del design approfondita e per la produzione, il tuo team può condividere e collaborare in tempo reale attraverso la piattaforma Altium 365™. I team di progettazione possono utilizzare Altium 365 per condividere dati di produzione, file di progetto e revisioni del design attraverso una piattaforma cloud sicura e in Altium Designer.
Abbiamo solo sfiorato la superficie di ciò che è possibile con Altium Designer su Altium 365. Inizia oggi la tua prova gratuita di Altium Designer + Altium 365.