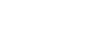
Construir uma placa significa conformar-se ao processo de fabricação para a sua seleção de camadas e materiais. Em algum momento, você terá que projetar as conexões na sua PCB, e até mesmo estas têm requisitos específicos que visam garantir a fabricabilidade. Nesta seção do nosso curso intensivo de DFM, vamos olhar para algumas das restrições básicas de DFM em elementos condutores de uma PCB, bem como o desenvolvimento das camadas de silkscreen/solda de superfície para DFA.
Um DFM bem-sucedido no layout da PCB começa por definir suas regras de design para levar em conta restrições importantes de DFM. As regras de DFM mostradas abaixo refletem algumas das capacidades de design contemporâneas que se encontraria na maioria dos fabricantes. Certifique-se de que os limites que você define nas regras de design da sua PCB não violem esses limites, para que você possa garantir a conformidade com a maioria das limitações de design padrão.
Com suas seleções de materiais finalizadas, agora é hora de mergulhar nos detalhes específicos do layout da sua PCB. Embora os fluxos de trabalho de engenharia individuais possam variar de um projetista para outro, existem várias considerações de design primárias que necessitam de requisitos precisos de DFM (Design for Manufacturing) para considerar uma placa 100% pronta para a fabricação. Nas seções seguintes, você aprenderá os detalhes de como estrategizar o layout da sua PCB, incluindo especificações de SMT (Surface-Mount Technology) e through-hole, documentação de silkscreen, aplicações de máscara de solda e mais.
Projetistas profissionais usam PCBs multicamadas com roteamento em duas camadas, o que requer o uso de vias. As vias são uma parte crítica de todo design de PCB e são responsáveis por transmitir corrente elétrica entre as camadas. Ao projetar vias passantes (plated through-hole vias), é recomendado manter uma proporção de aspecto de 8:1 entre o diâmetro do furo e o comprimento da via. A tabela abaixo mostra um conjunto de tamanhos padrão de brocas (em mils):
|
|
|
|
|
|
|
|
|
|
|
|
|
|
|
|
|
|
|
|
|
|
|
|
|
|
|
As vias padrão devem manter distâncias mínimas de folga de condutores adjacentes. A folga dependerá das capacidades de processamento específicas da casa de fabricação, bem como da necessidade de folgas específicas conforme exigido para certos tipos de PCBs (como placas de alta tensão). Há uma folga entre vias que limitará a densidade permitida de vias, com folgas típicas de parede de furo de broca a parede de furo de broca sendo tão grandes quanto 10 mils. Esses requisitos limitarão quão densamente as conexões podem ser roteadas entre camadas, bem como a densidade de vias de costura ao amarrar planos ou polígonos juntos.
Escolher entre componentes through-hole ou dispositivos de montagem em superfície (SMD) terá um impacto direto nos custos gerais e no tempo de fabricação. É recomendado optar por SMD para designs de placas modernas, pois isso resulta em tempos de produção mais rápidos e maior confiabilidade. A maioria dos componentes necessários para um design moderno são fabricados como componentes SMD. Algumas exceções incluem conectores, que muitas vezes estão disponíveis como componentes SMD ou through-hole. Para manter os custos de produção mais baixos em um design e garantir que o mínimo de passagens de solda sejam necessárias, é desejável ter a colocação apenas em uma camada, mesmo nos casos em que ambos os tipos de componentes são misturados no mesmo tipo de design.
O anel anular é geralmente definido como a diferença entre o diâmetro desejado do pad e o diâmetro correspondente da broca, embora isso não seja completamente correto. A definição clássica que acabei de mencionar refere-se ao pad de aterrissagem em uma via. A realidade é que o anel anular é bastante diferente do tamanho do pad de aterrissagem da via; ele se refere ao anel de cobre restante ao redor de um furo perfurado após o furo ser perfurado, gravado e revestido com cobre. A broca nem sempre atinge o pad perfeitamente no centro devido à variação durante a fabricação. O resultado é que a broca pode estar ligeiramente fora do centro e deixaria algum cobre ao redor do furo da via.
A partir da imagem acima, podemos ver que a largura do anel anular para uma via perfeitamente fabricada obedeceria à seguinte fórmula:
Largura do Anel Anular = (Diâmetro do pad – Diâmetro do furo) / 2
Para garantir que a placa esteja em conformidade com os padrões de confiabilidade IPC, o diâmetro do pad deve ser 8 mils (Classe IPC 2) ou 10 mils (Classe IPC 3) maior que o diâmetro do furo da via. Este é um limite conservador que garantirá que quase sempre haja algum anel anular ao redor da via finalizada.
A relação de aspecto de uma via é a razão entre a profundidade da via e o diâmetro do furo perfurado (após a aplicação da galvanização). A relação de aspecto das vias deve ser mantida baixa o suficiente para garantir a fabricação de alta rendimento dessas estruturas. Para designs mais avançados, como PCBs HDI que usam microvias, o limite da relação de aspecto pode ser muito pequeno, alcançando 1:1 ou menor. Certifique-se de verificar as capacidades do seu fabricante antes de começar a adicionar vias ao layout da PCB. Você pode definir os limites para os tamanhos das vias dentro das regras de design da sua PCB.
Quando as densidades de conexão se tornam muito altas, como em um BGA com passo fino, é possível colocar a via diretamente na almofada de aterrissagem de um componente. O design via-in-pad permite a colocação próxima de componentes porque as vias não precisam ser colocadas a alguma distância de sua almofada de conexão. Os designs via-in-pad requerem algum preenchimento com epóxi condutivo ou não condutivo, seguido por vedação e metalização para proteger o interior da estrutura da via.
A via-in-pad é usada com vias passantes em casos onde a perfuração mecânica ainda é possível, cujo limite pode ser tão pequeno quanto 8 mils. Quando a densidade de componentes é extremamente alta, técnicas de design HDI são necessárias para fazer conexões com camadas internas. Este é um tópico mais avançado que é discutido em nossos outros eBooks.
Uma via coberta é uma via padrão que tem suas camadas superficiais cobertas com máscara de solda, de modo que nenhum cobre fique exposto. É típico definir vias pequenas (12 mils ou menos) como cobertas. Vias maiores podem exigir tampamento e preenchimento antes que possam ser cobertas com máscara de solda. As vias são cobertas por uma variedade de razões, e é uma boa ideia cobri-las quando estão muito próximas aos pads de aterrissagem em componentes SMD. O exemplo abaixo mostra uma instância onde é necessário aplicar o cobrimento devido à proximidade entre as vias e um banco de pads de solda em um componente SMD. Neste caso, se as vias não estivessem cobertas, é possível que a solda se infiltre por estas até a parte de trás da placa, possivelmente causando um curto-circuito.
Embora existam preocupações com a montagem, ainda pode haver uma razão para deixar vias descobertas. Por exemplo, se uma via específica for desejável para uso como um ponto de teste, então ela precisa ser acessível com uma sonda, então a máscara de solda precisará ser removida dessa via. Testes serão discutidos mais no próximo capítulo desta série.
Semelhante aos furos passantes, as vias cegas e/ou enterradas (BBV) são furos que conectam uma ou mais camadas. Neste processo, uma via cega conecta uma camada externa a uma ou mais camadas internas, mas não a ambas as camadas externas, e uma via enterrada conecta uma ou mais camadas internas, mas não a uma camada externa. A imagem abaixo mostra um exemplo de vista em corte transversal de uma PCB de 6 camadas com vias cegas e enterradas:
Não assuma simplesmente que seu fabricante será capaz de produzir todas as possíveis combinações de vias cegas e enterradas. Vias cegas e enterradas perfuradas mecanicamente e a laser devem ser definidas em camadas específicas para garantir uma fabricação bem-sucedida, elas não podem ser colocadas em pares de camadas arbitrários. Certifique-se de entrar em contato com sua casa de fabricação primeiro e obter alguma orientação sobre o uso de vias cegas e enterradas em um layout de PCB.
Em alguns casos, é necessário reduzir a largura de uma trilha para rotear até uma almofada de pouso para um componente. Uma trilha reduzida (às vezes chamada de redução) conecta-se a uma almofada e corre pelo menos 0,010” de distância da almofada antes de se alargar para a largura grande da trilha.
Para trilhas com impedância controlada, como as que seriam necessárias em designs de alta velocidade, geralmente é uma má ideia aplicar estreitamento, pois isso cria uma variação de impedância. Em vez disso, use camadas mais finas se você precisar manter uma largura menor. Os componentes para esses designs tendem a ter pads de aterrissagem menores de qualquer forma, então eles não precisarão de estreitamento se o empilhamento e as trilhas forem dimensionados corretamente.
Com os tipos de componentes preferenciais estabelecidos, agora é hora de decidir como colocar e orientar essas peças na sua placa de forma eficiente. Esse processo terá um grande efeito em como você utiliza o espaço disponível no layout da sua placa e pode ser um dos passos mais desafiadores no seu processo de design. Abaixo, você encontrará recomendações específicas sobre como otimizar o posicionamento dos seus componentes para que sejam tanto fabricáveis quanto capazes de atender às suas exigências de design específicas.
Antes de entrar nos detalhes de posicionamento e orientação de componentes, há várias diretrizes gerais a ter em mente:
Com as informações apresentadas neste capítulo, você está agora bem equipado para começar seu processo de colocação e orientação de componentes para atender aos requisitos fundamentais de fabricação. Agora que seu design está bem encaminhado para a conclusão, é hora de finalizar o processo de layout da placa configurando seus requisitos de ponto de teste no próximo capítulo.
Quando estiver pronto para iniciar seu projeto e quiser garantir que atende a todos os requisitos de DFM para o layout da sua PCB, use os recursos de design e layout no Altium Designer®. Uma vez que seu projeto esteja pronto para uma revisão de design completa e fabricação, sua equipe pode compartilhar e colaborar em tempo real através da plataforma Altium 365™. As equipes de design podem usar o Altium 365 para compartilhar dados de fabricação, arquivos de projeto e revisões de design através de uma plataforma segura na nuvem e no Altium Designer.
Apenas começamos a explorar o que é possível com o Altium Designer no Altium 365. Comece seu teste gratuito do Altium Designer + Altium 365 hoje.