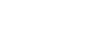
Ein Board zu bauen bedeutet, sich an den Herstellungsprozess für Ihren Lagenstapel und die Materialauswahl anzupassen. Irgendwann müssen Sie die Verbindungen auf Ihrer Leiterplatte entwerfen, und auch diese haben spezifische Anforderungen, die darauf abzielen, die Herstellbarkeit zu gewährleisten. In diesem Abschnitt unseres DFM-Crashkurses werden wir uns einige der grundlegenden DFM-Beschränkungen für leitfähige Elemente auf einer Leiterplatte ansehen, sowie die Entwicklung der Oberflächen-Siebdruck-/Lötstopplackschichten für DFA.
Erfolgreiches DFM im PCB-Layout beginnt damit, Ihre Designregeln so festzulegen, dass sie wichtige DFM-Beschränkungen berücksichtigen. Die unten gezeigten DFM-Regeln spiegeln einige der zeitgenössischen Designfähigkeiten wider, die man bei den meisten Herstellern finden würde. Stellen Sie sicher, dass die Grenzen, die Sie in Ihren PCB-Designregeln festlegen, diese Grenzen nicht verletzen, damit Sie sicherstellen können, dass Sie den meisten Standard-Designbeschränkungen entsprechen.
Mit der endgültigen Auswahl Ihrer Materialien ist es nun an der Zeit, sich in die spezifischen Details Ihres PCB-Layouts zu vertiefen. Obwohl die Arbeitsabläufe einzelner Ingenieure von einem Designer zum nächsten unterschiedlich sein können, gibt es eine Reihe von primären Designüberlegungen, die präzise DFM-Anforderungen benötigen, um eine Platine als 100% fertig für die Herstellung zu betrachten. In den folgenden Abschnitten erfahren Sie die Einzelheiten der Strategie für Ihr PCB-Layout, einschließlich SMT- und Durchsteck-Spezifikationen, Siebdruckdokumentation, Lötmaskenanwendungen und mehr.
Professionelle Designer verwenden mehrlagige PCBs mit Verdrahtung auf zwei Ebenen, was den Einsatz von Vias erfordert. Vias sind ein kritischer Teil jedes PCB-Designs und sind verantwortlich für die Übertragung des elektrischen Stroms zwischen den Schichten. Beim Design von durchkontaktierten Vias wird empfohlen, ein Aspektverhältnis von 8:1 zwischen dem Lochdurchmesser und der Via-Länge einzuhalten. Die untenstehende Tabelle zeigt eine Reihe von Standardbohrgrößen (in mils):
|
|
|
|
|
|
|
|
|
|
|
|
|
|
|
|
|
|
|
|
|
|
|
|
|
|
|
Standard-Durchkontaktierungen sollten minimale Abstände zu benachbarten Leitern einhalten. Der Abstand hängt von den spezifischen Verarbeitungskapazitäten des Herstellungsbetriebs ab, sowie von der Notwendigkeit spezifischer Abstände, die für bestimmte Arten von PCBs erforderlich sind (wie z.B. Hochspannungsplatinen). Es gibt einen Durchkontaktierung-zu-Durchkontaktierung-Abstand, der die zulässige Dichte von Durchkontaktierungen begrenzt, mit typischen Bohrlochwand-zu-Bohrlochwand-Abständen, die bis zu 10 mils groß sein können. Diese Anforderungen werden begrenzen, wie dicht Verbindungen zwischen den Schichten sowie die Dichte von Stitching-Durchkontaktierungen beim Verbinden von Ebenen oder Polygonen geroutet werden können.
Die Wahl zwischen Durchsteckkomponenten oder oberflächenmontierten Bauteilen (SMD) hat direkte Auswirkungen auf die Gesamtkosten und die Fertigungszeit. Es wird empfohlen, bei modernen Platinenentwürfen bei SMD zu bleiben, da dies zu schnelleren Platinenfertigungen und einer höheren Zuverlässigkeit führt. Die meisten Komponenten, die für ein modernes Design benötigt werden, werden als SMD-Komponenten hergestellt. Einige Ausnahmen bilden Steckverbinder, die oft sowohl als SMD- als auch als Durchsteckkomponenten verfügbar sind. Um die Produktionskosten in einem Design niedrig zu halten und um sicherzustellen, dass möglichst wenige Löt-Durchgänge benötigt werden, ist es wünschenswert, nur eine Schicht für die Platzierung zu haben, selbst in Fällen, in denen beide Arten von Komponenten im gleichen Design gemischt werden.
Der Ringplattenbereich wird üblicherweise als die Differenz zwischen dem gewünschten Pad-Durchmesser und dem entsprechenden Bohrdurchmesser definiert, obwohl dies nicht ganz korrekt ist. Die klassische Definition, die ich gerade erwähnt habe, bezieht sich auf das Landepad bei einer Durchkontaktierung. Die Realität ist, dass der Ringplattenbereich sich ziemlich von der Größe des Landepads einer Durchkontaktierung unterscheidet; er bezieht sich auf den verbleibenden Kupferring um ein gebohrtes Loch, nachdem das Loch gebohrt, geätzt und mit Kupfer beschichtet wurde. Der Bohrer trifft nicht immer perfekt zentriert auf das Pad aufgrund von Abweichungen während der Fertigung. Das Ergebnis ist, dass der Bohrer leicht außermittig sein könnte und somit etwas Kupfer um das Durchkontaktierungsloch herum lassen würde.
Aus dem obigen Bild können wir sehen, dass die Breite des Ringes für eine perfekt gefertigte Durchkontaktierung der folgenden Formel folgen würde:
Ringbreite = (Durchmesser des Pads – Durchmesser des Lochs) / 2
Um sicherzustellen, dass die Platine den IPC-Zuverlässigkeitsstandards entspricht, sollte der Pad-Durchmesser 8 mils (IPC Klasse 2) oder 10 mils (IPC Klasse 3) größer als der Durchmesser des Bohrlochs der Durchkontaktierung sein. Dies ist eine konservative Grenze, die sicherstellt, dass fast immer ein Ring um die fertige Durchkontaktierung vorhanden ist.
Das Aspektverhältnis einer Durchkontaktierung ist das Verhältnis zwischen der Tiefe der Durchkontaktierung und dem Durchmesser des gebohrten Lochs (nach dem Auftragen der Beschichtung). Das Aspektverhältnis von Durchkontaktierungen sollte niedrig genug gehalten werden, um eine hohe Ausbeute bei der Fertigung dieser Strukturen zu gewährleisten. Für fortschrittlichere Designs, wie HDI-PCBs, die Mikrovias verwenden, kann die Grenze des Aspektverhältnisses sehr klein sein und 1:1 oder kleiner erreichen. Stellen Sie sicher, dass Sie die Fähigkeiten Ihres Herstellers überprüfen, bevor Sie Durchkontaktierungen in das PCB-Layout einfügen. Sie können die Grenzen für die Größen der Durchkontaktierungen in Ihren PCB-Designregeln festlegen.
Wenn die Anschlussdichten sehr hoch werden, wie bei einem BGA mit feinem Raster, ist es möglich, die Via direkt im Landepad für eine Komponente zu platzieren. Via-in-Pad-Design ermöglicht eine enge Platzierung von Komponenten, da Vias nicht in einiger Entfernung von ihrem Anschluss-Landepad platziert werden müssen. Via-in-Pad-Designs erfordern eine gewisse Füllung mit leitfähigem oder nicht-leitfähigem Epoxidharz, gefolgt von Abdeckung und Beschichtung, um das Innere der Via-Struktur zu schützen.
Via-in-Pad wird bei Durchkontaktierungen verwendet, in Fällen, in denen mechanisches Bohren noch möglich ist, dessen Grenze bis zu 8 Mil klein sein kann. Wenn die Komponentendichte extrem hoch ist, sind HDI-Design-Techniken erforderlich, um Verbindungen zu inneren Lagen herzustellen. Dies ist ein fortgeschritteneres Thema, das in unseren anderen eBooks besprochen wird.
Ein abgedecktes Via ist ein Standard-Via, dessen Oberflächenschichten mit Lötstopplack bedeckt sind, sodass kein Kupfer freiliegt. Es ist üblich, kleine Vias (12 Mil oder weniger) als abgedeckt zu definieren. Größere Vias benötigen möglicherweise eine Kappe und Füllung, bevor sie mit Lötstopplack abgedeckt werden können. Vias werden aus verschiedenen Gründen abgedeckt, und es ist eine gute Idee, sie abzudecken, wenn sie sehr nah an den Landepads von SMD-Komponenten liegen. Das untenstehende Beispiel zeigt einen Fall, in dem es notwendig ist, das Abdecken aufgrund der Nähe zwischen Vias und einer Reihe von Lötpads auf einer SMD-Komponente anzuwenden. In diesem Fall könnte, wenn die Vias nicht abgedeckt wären, Lötzinn durch diese auf die Rückseite der Platine fließen, was möglicherweise einen Kurzschluss verursachen könnte.
Obwohl es Montagebedenken gibt, kann es dennoch einen Grund geben, Vias nicht abzudecken. Wenn beispielsweise ein spezifisches Via als Testpunkt verwendet werden soll, muss es mit einer Sonde zugänglich sein, sodass der Lötstopplack von diesem Via entfernt werden muss. Das Testen wird im nächsten Kapitel dieser Serie ausführlicher besprochen.
Ähnlich wie Durchgangsbohrungen verbinden blinde und/oder vergrabene Vias (BBV) eine oder mehrere Schichten. Bei diesem Prozess verbindet ein blindes Via eine äußere Schicht mit einer oder mehreren inneren Schichten, jedoch nicht mit beiden äußeren Schichten, und ein vergrabenes Via verbindet eine oder mehrere innere Schichten, jedoch nicht mit einer äußeren Schicht. Das Bild unten zeigt eine beispielhafte Querschnittsansicht eines 6-Lagen-PCBs mit blinden und vergrabenen Vias:
Gehen Sie nicht einfach davon aus, dass Ihr Hersteller jede mögliche Kombination von blinden und vergrabenen Vias herstellen kann. Mechanisch und mit Laser gebohrte blinde und vergrabene Vias müssen in spezifische Schichten gesetzt werden, um eine erfolgreiche Fertigung zu gewährleisten; sie können nicht auf beliebigen Schichtpaaren platziert werden. Stellen Sie sicher, dass Sie sich zuerst mit Ihrem Fertigungsbetrieb in Verbindung setzen und einige Richtlinien für die Verwendung von blinden und vergrabenen Vias in einem PCB-Layout erhalten.
In einigen Fällen ist es notwendig, eine Leiterbahn zu verjüngen, um sie in ein Landepad für eine Komponente zu führen. Eine verjüngte Leiterbahn (manchmal auch als Verjüngung bezeichnet) verbindet sich mit einem Pad und verläuft mindestens 0,010” vom Pad entfernt, bevor sie sich zur größeren Leiterbahnbreite ausweitet.
Für kontrollierte Impedanzleiterbahnen, wie sie in Hochgeschwindigkeitsdesigns benötigt werden, ist es im Allgemeinen keine gute Idee, eine Verjüngung (Necking) anzuwenden, da dies eine Impedanzabweichung erzeugt. Verwenden Sie stattdessen dünnere Schichten, wenn Sie eine kleinere Breite beibehalten müssen. Komponenten für diese Designs werden ohnehin kleinere Landepads haben, sodass sie keine Verjüngung benötigen, wenn der Stackup und die Leiterbahnen richtig dimensioniert sind.
Mit Ihren bevorzugten Komponententypen steht nun die Entscheidung an, wie Sie diese Teile effizient auf Ihrer Platine platzieren und ausrichten. Dieser Prozess wird einen großen Einfluss darauf haben, wie Sie den verfügbaren Platz auf Ihrem Board-Layout nutzen, und kann einer der herausforderndsten Schritte in Ihrem Designprozess sein. Unten finden Sie spezifische Empfehlungen, wie Sie Ihre Komponentenplatzierung optimieren können, um sowohl fertigungsgerecht zu sein als auch Ihre spezifischen Designanforderungen zu erfüllen.
Bevor wir auf die Details der Komponentenplatzierung und -ausrichtung eingehen, gibt es mehrere allgemeine Richtlinien, die Sie im Kopf behalten sollten:
Mit den in diesem Kapitel präsentierten Informationen sind Sie jetzt gut gerüstet, um Ihren Komponentenplatzierungs- und Orientierungsprozess zu beginnen, um grundlegende Herstellbarkeitsanforderungen zu erfüllen. Jetzt, da Ihr Design auf dem Weg zur Fertigstellung ist, ist es an der Zeit, den Layoutprozess der Platine abzuschließen, indem Sie Ihre Anforderungen an Testpunkte im nächsten Kapitel konfigurieren.
Wenn Sie bereit sind, mit Ihrem Design zu beginnen und sicherstellen möchten, dass Sie jede DFM-Anforderung für Ihr PCB-Layout erfüllen, nutzen Sie die Design- und Layoutfunktionen in Altium Designer®. Sobald Ihr Design bereit für eine gründliche Designprüfung und Fertigung ist, kann Ihr Team in Echtzeit über die Plattform Altium 365™ zusammenarbeiten und teilen. Designteams können Altium 365 nutzen, um Fertigungsdaten, Projektdateien und Designprüfungen über eine sichere Cloud-Plattform und in Altium Designer zu teilen.
Wir haben nur an der Oberfläche dessen gekratzt, was mit Altium Designer auf Altium 365 möglich ist. Starten Sie heute Ihre kostenlose Testversion von Altium Designer + Altium 365.