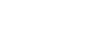
基板を製作するということは、レイヤースタックや材料選択における製造プロセスに従うことを意味します。いずれにしても、PCB上での接続を設計する必要があり、これらにも製造可能性を確保することを目的とした特定の要件があります。このDFMクラッシュコースのセクションでは、PCB内の導電要素に対する基本的なDFM制約と、DFAのための表面シルクスクリーン/はんだマスク層の開発について見ていきます。
PCBレイアウトにおける成功したDFMは、重要なDFM制約を考慮して設計ルールを設定することから始まります。以下に示すDFMルールは、ほとんどの製造業者で見られる現代の設計能力を反映しています。PCB設計ルールで設定する制限がこれらの制限を超えないようにして、ほとんどの標準的な設計制限に準拠できるようにしてください。
材料選定が完了したら、PCBレイアウトの具体的な詳細に深く潜り込む時が来ました。個々のエンジニアリングワークフローは設計者によって異なるかもしれませんが、製造のためにボードを100%準備完了とみなすためには、正確なDFM要件を考慮する必要があるいくつかの主要な設計上の考慮事項があります。以下のセクションでは、SMTおよびスルーホール仕様、シルクスクリーンの文書化、はんだマスクの適用など、PCBレイアウトを戦略的に進める具体的な方法について学びます。
プロの設計者は、2層でルーティングされる多層PCBを使用し、これにはビアの使用が必要です。ビアはすべてのPCB設計において重要な部分であり、層間で電流を伝達する責任があります。スルーホールビアを設計する際には、穴の直径とビアの長さの間で8:1のアスペクト比を維持することが推奨されます。以下の表は、標準的なドリルサイズ(ミル単位)のセットを示しています:
|
|
|
|
|
|
|
|
|
|
|
|
|
|
|
|
|
|
|
|
|
|
|
|
|
|
|
スタンダードビアは、隣接する導体からの最小クリアランスを保持する必要があります。クリアランスは、製造工場の特定の処理能力と、高電圧ボードなどの特定のタイプのPCBに必要な特定のクリアランスの要求に依存します。ビア間のクリアランスは、ビアの許容密度を制限し、典型的なドリルホール壁からドリルホール壁までのクリアランスは10ミルまで大きくなることがあります。これらの要件は、層間の接続をどれだけ密にルーティングできるか、および平面やポリゴンを結びつける際のステッチングビアの密度を制限します。
スルーホール部品と表面実装デバイス(SMD)の選択は、全体のコストと製造時間に直接影響を与えます。現代のボード設計では、SMDを使用することが推奨されます。これにより、ボードの回転が速くなり、信頼性が高まります。現代の設計に必要なほとんどの部品は、SMD部品として製造されています。例外としては、コネクタがあり、これらはしばしばSMDまたはスルーホール部品として利用可能です。設計における生産コストを低く抑え、最小限のはんだ付けパスが必要とされるため、同じタイプの設計で両方のタイプの部品が混在している場合でも、1層にのみ配置することが望ましいです。
アニュラリングは通常、望ましいパッド直径と対応するドリル直径との差として定義されますが、これは完全に正しいわけではありません。私が先に述べた古典的な定義は、ビアの着地パッドを指しています。実際には、アニュラリングはビアの着地パッドサイズとはかなり異なり、ドリルされた穴の周りに残された銅のリングを指します。これは、穴がドリルされ、エッチングされ、銅でめっきされた後のことです。製造中のワンダーにより、ドリルがパッドを完全に真ん中で打つとは限りません。その結果、ドリルがわずかに中心からずれ、ビア穴の周りにいくらかの銅が残ることがあります。
上記の画像から、完璧に製造されたビアの環状リング幅が以下の式に従うことがわかります:
環状リング幅 = (パッドの直径 - 穴の直径) / 2
基板がIPC信頼性基準に準拠していることを確実にするために、パッドの直径はビアのドリル穴の直径よりも8ミル(IPCクラス2)または10ミル(IPCクラス3)大きくする必要があります。これは、完成したビアの周りにほぼ常に何らかの環状リングが存在することを保証する保守的な限界です。
ビアのアスペクト比は、ビアの深さと(メッキを適用した後の)穴の直径との比率です。これらの構造の高い製造収率を保証するために、ビアのアスペクト比は十分に低く保たれるべきです。マイクロビアを使用するHDI PCBなど、より高度な設計では、アスペクト比の限界が非常に小さくなり、1:1やそれ以下に達することがあります。PCBレイアウトにビアを追加する前に、製造業者の能力を確認してください。PCB設計ルール内でビアサイズの限界を設定できます。
接続密度が非常に高くなる場合、例えばファインピッチのBGAのように、コンポーネントの着地パッドに直接ビアを配置することが可能です。ビア・イン・パッド設計により、ビアをその接続する着地パッドからある距離離して配置する必要がないため、コンポーネントを密接に配置できます。ビア・イン・パッド設計は、導電性または非導電性のエポキシでの充填、その後のキャッピングとめっきにより、ビア構造の内部を保護することを要求します。
ビア・イン・パッドは、機械的なドリリングがまだ可能な場合のスルーホールビアで使用され、その限界は8ミルまで小さくなることがあります。コンポーネントの密度が極端に高い場合は、内層への接続を行うためにHDI設計技術が必要です。これは、私たちの他の電子書籍で議論されているより高度なトピックです。
テンテッド・ビアとは、その表面層がはんだマスクで覆われ、銅が露出していない標準的なビアのことです。小さなビア(12ミル以下)をテンテッドと定義することが一般的です。大きなビアは、はんだマスクでテントする前にキャップとフィルが必要になる場合があります。ビアをテントする理由は様々あり、SMDコンポーネントの着陸パッドに非常に近い場合には、それらをテントすることが良い考えです。以下の例は、SMDコンポーネントのはんだパッドのバンクとビアの間の近接性のためにテンティングを適用する必要がある一例を示しています。この場合、ビアがテンテッドでなければ、はんだがこれらを通って基板の裏側に流れ込み、短絡を引き起こす可能性があります。
組み立ての懸念がある一方で、ビアをテンテッドにしない理由があるかもしれません。例えば、特定のビアをテストポイントとして使用することが望ましい場合、プローブでアクセスできるようにそのビアからはんだマスクを取り除く必要があります。テストについては、このシリーズの次の章でさらに詳しく説明されます。
スルーホールと同様に、ブラインドビアおよび/またはバリードビア(BBV)は、1つ以上の層を接続する穴です。このプロセスでは、ブラインドビアは外層を1つ以上の内層に接続しますが、両方の外層には接続しません。バリードビアは1つ以上の内層を接続しますが、外層には接続しません。下の画像は、ブラインドビアとバリードビアを持つ6層PCBの断面図の例を示しています:
製造業者があらゆる組み合わせのブラインドビアとバリードビアを製造できると仮定しないでください。機械的に穿孔されたブラインドビアとバリードビアは、成功した製造を保証するために特定の層に設定されなければならず、任意の層ペアに配置することはできません。PCBレイアウトでのブラインドビアとバリードビアの使用について、まず製造業者に連絡して、いくつかのガイダンスを得ることを確認してください。
場合によっては、コンポーネントのランディングパッドにルーティングするためにトレースをネックダウンする必要があります。ネックダウンされたトレース(時にはネックダウンと呼ばれる)はパッドに接続し、パッドから少なくとも0.010インチ離れたところで細くなり、大きなトレース幅に広がります。
制御インピーダンストレースの場合、例えば高速設計で必要とされるような場合、ネッキングを適用するのは一般的に良くない考えです。これはインピーダンスの偏差を生じさせるからです。代わりに、もし幅を小さく保つ必要がある場合は、薄い層を使用してください。これらの設計のコンポーネントは、どのようにしても小さなランディングパッドを持つ傾向があるので、スタックアップとトレースが適切にサイズされていれば、ネッキングは必要ありません。
好みのコンポーネントタイプを確立したら、次に、ボード上でこれらの部品を効率的に配置し向ける方法を決定する時が来ました。このプロセスは、ボードレイアウト上で利用可能なスペースをどのように利用するかに大きな影響を与え、設計プロセスで最も挑戦的なステップの一つになることがあります。以下に、コンポーネントの配置を最適化して、製造可能であり、特定の設計要件を満たすことができるようにするための具体的な推奨事項を示します。
コンポーネントの配置と向きの具体的な話に入る前に、念頭に置くべきいくつかの一般的なガイドラインがあります:
この章で提示された情報をもとに、基本的な製造要件を満たすためのコンポーネントの配置と向きのプロセスを開始する準備が整いました。設計が完成に近づいている今、次の章でテストポイント要件を設定することによって、ボードレイアウトプロセスを最終化する時が来ました。
デザインを開始する準備ができて、PCBレイアウトのすべてのDFM要件を満たしたい場合は、Altium Designer®のデザインおよびレイアウト機能を使用してください。デザインが徹底的なデザインレビューと製造の準備ができたら、チームはAltium 365™プラットフォームを通じてリアルタイムで共有および協力できます。設計チームは、Altium 365を使用して、製造データ、プロジェクトファイル、およびデザインレビューを安全なクラウドプラットフォームおよびAltium Designer内で共有できます。
Altium DesignerとAltium 365で可能なことの表面をかすめただけです。今日、Altium Designer + Altium 365の無料トライアルを開始してください。