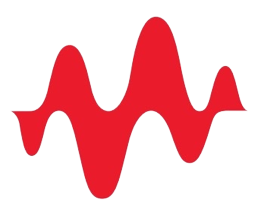
Progettare un PCB che non includa un elemento di alimentazione è piuttosto insolito, ma il fatto che sia un elemento comune non significa che non comporti delle sfide a livello di progettazione. Ci sono due varianti principali da considerare: gli alimentatori PCB lineari e a commutazione. Ognuno di essi presenta le proprie sfide in termini di layout PCB dell'alimentatore.
I circuiti degli alimentatori lineari sono semplici nella loro natura, con pochi componenti facili da montare su un PCB. Il problema è che questi circuiti sono inefficienti, il che implica la necessità di gestire significative perdite di potenza nell'energia termica irradiata e condotta. Questo fattore può complicare la situazione in presenza di componenti sensibili alla temperatura sul PCB o racchiusi all'interno di un involucro ermetico protettivo, in cui le opzioni di raffreddamento sono limitate.
I circuiti degli alimentatori PCB a commutazione sono più complessi degli alimentatori PCB lineari, ma anche molto più efficienti. Pur essendo un elemento significativo, perché riduce il tempo di progettazione del progettista PCB che si occupa della gestione termica, sfortunatamente comporta un'altra serie di problemi. Il circuito di commutazione potrebbe generare livelli significativi di rumore elettromagnetico che il progettista PCB deve gestire. Questo rumore elettrico può influenzare altri elementi del circuito sul PCB ed essere percepito oltre la scheda influenzando le apparecchiature vicine. In casi estremi, il rumore generato dal circuito dell'alimentatore PCB può risalire attraverso il cablaggio della rete elettrica e influenzare altri dispositivi collegati alla stessa alimentazione di rete.
Un altro potenziale problema di rumore è che i circuiti a commutazione tendono a generare una tensione di ondulazione sull'uscita che, se non gestita correttamente, può indurre interferenze sulla scheda attraverso accoppiamento capacitivo o induttivo tra tracce che corrono in parallelo o cavi raggruppati. Un ultimo e più delicato problema è il potenziale rimbalzo di massa sul PCB su cui è montato il circuito di commutazione. Una commutazione rapida può causare una variazione transitoria del potenziale di terra nel punto della scheda in cui i componenti di commutazione si collegano al piano di massa. Ciò si traduce in una differenza di potenziale temporanea sul piano di massa della scheda. In casi estremi, la differenza può far sì che componenti in una parte distante della scheda osservino e reagiscano a un segnale percepito risultante da questa falsa differenza di potenziale.
A meno che lo spazio non sia limitato, è consigliabile includere nel progetto della scheda un solido piano di massa dell'alimentatore per fornire una schermatura elettromagnetica. Se non è possibile dedicare un intero layer, considera come minimo un poligono di terra che copra l'intera area al di sotto dei componenti dell'alimentatore PCB.
Il piano di massa per la progettazione dell'alimentatore PCB deve essere separato dalla terra comune del resto del circuito per ridurre al minimo gli effetti di accoppiamento del rumore. Inoltre, il collegamento tra queste due masse dovrebbe essere limitato a un punto sulla scheda per evitare loop di massa.
Mantieni le tracce dei circuiti degli alimentatori PCB il più brevi e ampie possibile per ridurre le perdite resistive e le emissioni di rumore elettromagnetico. Dove lo spazio lo consente, il consiglio è di utilizzare colate poligonali. Questo è particolarmente importante per gli alimentatori lineari, in cui la conduttività termica può essere fondamentale.
Per ottimizzare il risultato, sarebbe meglio includere nel progetto della scheda dei layer interni a riempimento solido che utilizzano via per il collegamento dei piani di alimentazione e di massa. L'uso di via per commutare le tracce dell'alimentatore PCB da un layer all'altro dovrebbe essere evitato, in quanto il via agirà come un punto di aumento dell'impedenza. I poligoni che collegano più via offrono una soluzione migliore.
Le prestazioni sono influenzate dallo spessore dei layer di rame, anche se il maggiore spessore comporta un sovrapprezzo, e quindi potrebbe essere necessario trovare un compromesso tra costi e prestazioni.
Un'altra opzione per aumentare la conduttività consiste nell'aggiungere un layer di saldatura ai layer della scheda esterna attraverso modifiche alla maschera di saldatura. Tuttavia, è possibile ottenere prestazioni migliori aggiungendo delle barre o dei fili esterni tra i punti sulla scheda in cui sono installati i componenti di progettazione dell'alimentatore PCB.
Tenendo conto dell'esigenza di avere tracce quanto più corte possibile, i componenti dell'alimentatore PCB dovrebbero essere posizionati il più vicino possibile tra loro nell'orientamento ottimale per ottenere lunghezze di traccia brevi. A tal fine, può essere necessario montare i componenti su entrambi i lati della scheda.
Le tracce che trasportano segnali sensibili dovrebbero essere possibilmente instradate lontano dagli alimentatori su un layer della scheda non connesso, separato dalle tracce di progettazione del layout PCB dell'alimentatore a 12 V da un piano di massa. Le tracce del segnale non devono mai correre parallele alle tracce che trasportano l'alimentazione, per impedire l'accoppiamento del rumore dall'alimentatore del layout al segnale. Se la vicinanza è inevitabile, le tracce di segnale devono incrociare le tracce dell'alimentatore PCB a 90 gradi per ridurre al minimo gli effetti di accoppiamento del rumore.
Tutti i circuiti di alimentazione del layout generano calore, quindi il progetto della scheda dovrà includere la gestione termica. Pertanto, la prima considerazione relativa al layout dovrebbe essere il posizionamento dei componenti, separando quelli che generano calore da quelli sensibili al calore, se possibile mantenendo brevi lunghezze di traccia.
La considerazione successiva consiste nell'utilizzare il rame della scheda per fornire una conducibilità termica in modo da distribuire il calore in modo più uniforme lontano dai punti caldi e verso le aree che consentono la dissipazione del calore.
Un potenziale problema per gli alimentatori PCB a commutazione è che il circuito di controllo del feedback spesso contiene componenti sensibili alla temperatura che devono essere collocati insieme ai componenti di commutazione che generano calore. Se non controllati, i punti caldi possono causare instabilità dell'alimentatore del layout e aggravare i problemi termici.
Gli alimentatori PCB possono essere la fonte della maggior parte dei problemi termici e di rumore in un PCB, pertanto la progettazione della scheda deve tenerne conto fin dall'inizio. Una buona progettazione di una scheda comincia con un buon layout dell'alimentazione PCB.
Vuoi saperne di più su come Altium Designer® può aiutarti con le linee guida per l'elettronica di potenza per la tua prossima progettazione PCB? Parla con un esperto di Altium.