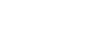
The medical device industry relies heavily on technology to deliver life-saving treatments and diagnostics. At the heart of many of the devices used, you will find the printed circuit board—a network of electrical pathways etched onto a laminate substrate. Given the industry in which devices are used, it is of the utmost importance that designers guarantee both quality and compliance in their PCB designs to ensure patient safety and device efficacy.
With that in mind, manufacturers must establish relationships with certified suppliers for compliant medical PCBs, and we will explore exactly how they can do so.
It’s a given. With lives potentially on the line, medical devices are subject to rigorous regulatory requirements to ensure effectiveness as, in use, patient well-being. These regulations extend to the components used within the devices, including PCBs. Here’s why certified suppliers are essential:
By partnering with certified suppliers, medical device manufacturers gain access to PCBs that meet the highest quality and compliance standards, mitigating the risks associated with faulty, unreliable devices.
If your company is looking for a certified supplier, note that several key certifications demonstrate a supplier’s commitment to quality and compliance for medical components.
Specific ISO’s aside, differing industry certifications might be relevant depending on the type of medical device and its intended use. Examples include Underwriters Laboratories, which offers certifications for various components used in medical devices, making sure that they meet safety standards, and Association Connecting Electronics Industries, which provides standards and certifications for various elements of the PCB manufacturing process for the sake of consistent quality and reliability in creations.
Beyond certifications, there are a myriad of important qualities that companies should consider when choosing a medical PCB supplier. Experience in the medical device industry is, of course, a given. But also, working with a supplier that has a proven track record in this specific field ensures a shared understanding of the critical nature of quality and stringent regulatory compliance requirements associated with the end devices.
Look for a supplier that possesses the technical expertise and production capacity to meet your specific PCB requirements—this includes the ability to handle a multitude of materials, elaborate circuitry needs, and the desired layer count for your PCB design. Comprehensive testing throughout the manufacturing process is also essential to prevent errors or faults further down the production line. If possible, try to partner with a supplier that has robust testing procedures and validation protocols that meet industry standards specifically designed for medical devices.
A robust change control process will also prove beneficial. This system ensures that any modifications made to the PCB design—or the manufacturing process itself—are documented meticulously and implemented effectively. Traceability, as mentioned before, will help companies efficiently identify and track the materials and production steps used in every PCB design. Finally, your ideal supplier should be able to guide you through the PCB compliance process to guarantee your product meets the critical standards held in the medical industry—expertise in this area is a key quality to seek.
Before any successful partnership can be forged and fully fruitful, companies have additional work to do. Partnering with a certified supplier is just one step on the journey toward compliant and reliable component sourcing. Remember that building a strong working relationship—one of collaboration, communication, and transparency—is arguably even more important; at the very least, it is imperative for success. Maintain consistent communication with your supplier so that you can outline your specific needs, the relevant regulatory requirements, and your quality expectations in detail.
Involve your supplier early in the design phase of your device, also. This collaborative approach will help designers optimize the PCB for manufacturability from conception, with regulatory compliance considerations also taken into account throughout the development process. Lastly, it’s important to work with suppliers to identify and mitigate potential risks associated with the PCB design, materials and components used, and the manufacturing processes; a joint approach to risk management somewhat safeguards the quality and compliance of your eventual devices and introduces a degree of equal accountability if faults are found.
Strong relationships equate to solid products, which can only be a good thing for both the end user and the bottom line.
Finding the right supplier is, beyond establishing internal systems and teams, the most important element for your project’s eventual success. If companies prioritize certified suppliers, they can ensure the consistent production of PCBs that meet the highest standards for quality, safety, and regulatory compliance. This, in turn, translates to life-saving devices with reliable performance that build trust with both patients and healthcare professionals. As always, a focus on quality throughout the supply chain will determine the success of a device and the well-being of the patients who rely on it.