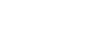
In the PCB industry, engineers must now, more than ever, strive to achieve design excellence; it is no longer a choice but a necessity. It signifies high-performance, reliable electronics that not only meet stringent industry standards but also deliver superior functionality in a volatile market that pushes engineers to meet tightened deadlines and budgets caused by shifts and rising demand. To lessen the burden on designers and engineers, product lifecycle management assists in the establishment of a strategic framework for the management of all data and processes associated with the PCBs life cycle, from its initial conceptualization to eventual end-of-life disposal.
By leveraging a robust PLM system, PCB engineers can improve design efficiency, help disparate teams embrace innovation and collaboration, and ensure exceptional product quality.
PLM software functions as a centralized repository for all critical PCB design data, including schematics, layouts, comprehensive component libraries, and bills of materials (BOMs), among others. By adopting this centralized approach, companies can eliminate the inefficiency associated with scattered files and version control issues across disparate workstations and departments and promote collaboration between designers, who can meticulously track changes made to the design and ensure that everyone is working on the most current version. Not only that, PLM can also automate repetitive tasks such as design document generation and BOM updates whenever there’s a component change; the benefit of this is two-fold: human error, which is common in data entry tasks, is mitigated, and engineers have time to focus on core competencies like creative problem-solving and innovation.
For instance, advanced PLM systems can integrate with specialized design for manufacturability (DFM) software. DFM tools analyze the PCB layout and identify potential manufacturing challenges early in the design process, which allows engineers to proactively make adjustments to the layout, such as optimizing component placement for easier assembly by automated pick-and-place machines or ensuring sufficient clearances to avoid solder bridging during soldering. By incorporating DFM principles from the outset, PLM contributes to a smoother manufacturing transition and reduces the potential for costly rework cycles, positively impacting a company’s bottom line.
Effective communication between PCB designers, engineers, and manufacturing teams is the cornerstone of successful collaboration; PLM encourages and facilitates this collaborative environment through the provision of a secure platform for real-time communication and data sharing. Design reviews can be conducted efficiently online, with stakeholders from various departments or teams accessing the latest design files and providing constructive feedback directly within the PLM system. This enables transparency, which, when combined with streamlined communication, drastically reduces errors and accelerates critical decision-making throughout the design lifecycle.
Not limited to internal ecosystems, PLM also facilitates communication with external partners such as component suppliers and contract manufacturers. Through secure online portals within the system, external stakeholders can gain real-time visibility into design changes and specifications, allowing them to anticipate necessary supply alterations; this level of transparency helps companies to closely collaborate with one another across the supply chain, with each stakeholder being on the same page enabling proactivity in the face of change.
Not limited to just internal design data, PLM influence extends to the integration of sophisticated tools that capture and analyze valuable customer requirements and usage data, helping designers incorporate user experience (UX) considerations right from the outset of the design process. For example, PLM can integrate with thermal simulation software, which allows engineers to optimize heat dissipation within the final PCB layout. By adopting this data-driven approach, companies can be sure that the resulting product is not just functional but also delivers a superior user experience—leading to higher customer satisfaction and more brand loyalty.
Taking a user-centered design a step further, advanced PLM systems can even integrate with tools for capturing real-world performance data from deployed PCBs. This data can then be fed back into the PLM system and analyzed to identify areas for improvement in future designs; it’s a closed-loop approach that guarantees PCB designers are constantly innovating and developing products that exceed the evolving expectations and needs of the customer base.
Product lifecycle management plays an instrumental role in achieving PCB design excellence; through the implementation of a robust PLM solution, companies can streamline workflows, better the collaborative experience across siloed teams, and integrate user-centric design principles. While initial implementation may involve the navigation of challenges such as system customization, data migration, and additional employee training, the long-term benefits of achieving design excellence outweigh potential cost and time considerations.
Companies can expect to see improvements in efficiency, product quality, and time-to-market, ultimately gaining a competitive edge in a continuously changing electronics industry. As the industry and its key stakeholders continue to push the boundaries of miniaturization, high-speed signal integrity, and complex functionality, PLM will likely become an even more indispensable tool for PCB designers, which ensures they can translate innovative ideas into market-leading products.