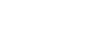
Digital transformation is a buzzword seen all across industries and in publications. Every company is on it, and when it comes to implementing new, accessible software or systems in the workplace, it often comes across as if it’s as simple as plug-and-play. It seldom ever is. In reality, successful implementation relies on talented teams and training.
Without well-structured and comprehensive training programs, companies cannot realize the potential of their cutting-edge tools. This is especially true in the face of continuous innovation, where new solutions, like product lifecycle management (PLM) and enterprise resource planning (ERP), among others, are emerging and disrupting everyday business operations.
According to Gallup’s State of the Global Workplace (2019), companies that give employees sufficient training are 17% more productive than those that don’t. Focusing on PLM basics, which is essential in modern manufacturing processes, untrained teams may have access to the software but won’t understand its intricacies. They won’t use all the features; workflows would remain inefficient; and your company would miss an opportunity to maximize the return on investment promised by the new technology.
Back in time, PLM training was limited to basic user manuals and one-size-fits-all workshops. Today, the increasing sophistication of tools on the market necessitates a nuanced approach to PLM training that addresses the diverse needs of different teams within companies.
Tailored PLM training programs, for example, cater to role-specific needs and functionalities within the team, such as designers, engineers, and project managers. For employees who need a flexible experience, personalized learning approaches combine instructor-led sessions with self-paced online modules and on-demand resources to suit individual learning styles and preferences. And, given that technology is in a state of continuous evolution, so must PLM training programs; companies can incorporate ongoing PLM training modules and resources to keep teams updated on new features and best practices and create a culture of continuous learning.
Comprehensive and adaptable PLM training strategies can help companies equip teams to adopt PLM tools and thrive in product design and development. It might cost, but remember that investment in PLM training is not just an expense; it’s a commitment to unlock cost savings and operational efficiency.
Different teams have unique needs and skill sets, so you must tailor your company’s PLM training approach for maximum impact. The programs need to guarantee seamless adoption and optimal use of the new tool. Here’s how to assess and address these requirements:
These lists are not exhaustive; there are many ways to improve the internal PLM training process. But there are three critical considerations, regardless of the methods chosen, to ensure success. Involving members of different teams in the PLM training design process will help you craft programs that meet employees’ needs; asking participants for feedback will help you assess your program’s effectiveness, allowing for adjustments where necessary; and PLM training should not end after initial implementation. Make it continuous, provide ongoing support, and try to get teams access to experts or leading institutions to improve long-term engagement and knowledge retention.
It’s important to remember that PLM training isn’t exclusive to employees; sometimes, employers need the same amount. When it comes to PLM basics and more, leaders must understand that its power extends beyond operation efficiency; its centralized repository of data, collated from the entire product life cycle, can help them unlock valuable insights for strategic decision-making.
Companies must equip executives with the knowledge to leverage the tool to its full potential and assist their employees in doing so.
Focus on the long-term benefits of PLM integration—the big picture. Lean on improved product quality and cost-efficiency factors, as well as better collaboration between siloed teams and reduced time to market. Add to this lessons on how to extract and analyze key performance indicators (KPIs) from the system to inform strategic decisions on product development, resource allocation, and market competitiveness, and show leaders how PLM solutions can align with specific business goals and objectives, contributing to the company’s strategic vision.
To align business goals with PLM capabilities, stakeholders must:
Without measuring the effectiveness of your PLM training programs and evaluating the impact of PLM implementation, your company won’t know whether its investments were worthwhile. But how can you set benchmarks for success? First, you need to have outlined a clear learning objective that employees are expected to meet, and then you need to move forward with a multi-pronged approach, focusing on both knowledge acquisition and behavioral change. Here are a few recommended methods:
The Kirkpatrick Four-Level Model
Donald Kirkpatrick’s 1959 framework (with updates in 1974 and 1993) remains popular today and helps evaluate PLM training at different levels:
If your company uses an LMS, leverage the data to track completion rates, engagement metrics, and time spent on different modules. This will give you insights into employee progress and identify areas needing improvement or further tweaking.
Performance metrics:
Monitor PLM-related KPIs like data entry speed, accuracy, and completion rates of specific tasks within the system to help assess how employees adapt to the new system and see its impact on their work.
Manager feedback:
70% of team engagement is attributable to managers. With that in mind, encourage team leaders to give leadership regular updates on employee progress. Leaders can use this feedback to identify where employees are excelling and struggling.
Self-assessment surveys:
Conduct surveys to gather employee feedback on their comfort level and confidence using the PLM system. This can help identify areas where additional support and PLM training might be needed.
Focus groups:
All employees can discuss their experiences with the new PLM system through inclusive focus groups. Focus groups provide useful insights into challenges, suggestions for improvement, and perception of a new system.
Combining these methods will help you understand how your employees feel about PLM adoption, how they are learning, and whether you need to adapt your approach to better suit them. A culture of honest, open communication will help you to identify areas for improvement, ensure successful implementation, and maximize the benefits of the PLM system for your company.
Implementing new technology is an ongoing journey rather than a destination. The initial PLM training is crucial, but so is the adoption of a continuous learning culture for companies that plan to maximize the tool’s potential and help their teams perform to the best of their ability in a dynamic industry. By evaluating the effectiveness of PLM training programs and adapting them to suit your employee needs, companies can ensure knowledge retention, encourage upskilling and reskilling, and drive longer-term success across the board. Again, it’s an investment in your company’s future, not a box-checking expense.