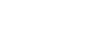
PCB design has always been intertwined with product development, spanning into realms like mechanical design and software development as progressively more advanced products are released to market. How does the electronics design portion of a system get rolled in with the rest of the product data? The answer is integration between CAD data management systems and PLM systems.
On paper, the integration of PLM with existing design tools can sound simplistic, but, in reality, it isn’t without challenges. PLM integration requires up-front investment in time and development effort (and of course cost), but the return on investment comes from eliminating errors, reduced time to market, and a closed loop between design, manufacturing, and quality control. Once CAD systems across engineering disciplines are linked into an integrated PLM solution,
Let’s take a look at some of the common hurdles faced by companies and how integrated PLM solutions can help overcome them.
One of the biggest challenges lies in the fragmented nature of PCB design data. Design files, component libraries, manufacturing specifications, and revision control often reside in separate silos, which can lead to version control issues and inefficiencies across teams.
Integrated PLM solutions provide companies with a single source of truth for all product data, which guarantees all relevant stakeholders are working from the same information. Inevitably, this eliminates the finger-pointing that can arise from version control confusion and wasted time searching for the correct files. Specific functionalities like native integrations with popular PCB design tools like Altium further streamline data exchange within the design environment. The provision of a central repository allows team members to easily access and share data in real time, streamlining communication and reducing the risk of errors, which helps to enhance collaboration between design, engineering, and manufacturing.
Another hurdle is the incompatibility between design tools and data formats. Migrating data between different software programs can be a tedious and, when dealt with by humans, error-prone process.
Fortunately, PLM solutions can act as a bridge between these design islands. They offer translators and importers that convert data between various design tools and formats, removing the need for manual data entry and reducing the risk of errors during migration. Product lifecycle management also provides a platform for the management of different data formats within a single system, which simplifies the design process and fosters better collaboration between teams that use different design tools and systems.
Coupled with the increasing demand and shortened timeframes given to engineers, the complexity of modern PCBs can lead to errors and inefficiencies. Manually managing repetitive tasks like bill of materials (BOM) generation and design rule checks (DRCs) is time-consuming and error-prone, even in times when there isn’t so much pressure.
Product lifecycle management systems can provide some reprieve for teams through the automation of such tasks. They can automatically generate BOMs based on the latest design data, which ensures accuracy and reduces the risk of human error, and automate DRCs to free up engineers’ time to focus on human-dependent—usually more technical—tasks. Leading PLM solutions have the added benefit of automating tasks like change order management and revision control, which, ultimately, reduces the time it takes to get products to market and improves teams’ overall efficiency courtesy of a streamlined workflow.
The benefits of PLM do, however, extend beyond said streamlining of workflows and reduction of errors. Through the establishment of a central repository for all PCB data, PLM allows companies to adopt a culture of knowledge sharing and collaboration, which opens the door to new ideas and innovations, as engineers have easier access to past designs and can learn from each other’s work. That same level of access and insight showcases PLM’s ability to improve traceability throughout the entire PCB lifecycle, with the identification and consequent fixing of problems being made easier through past iterations—potentially leading to significant cost savings and improved product quality when issues are found early in the design process.
For industries with stringent regulations and complex PCB requirements, like medical devices or automotive electronics, PLM can be particularly advantageous. Through integration with industry-specific tools and standards, the system can streamline compliance processes and ensure that designs, across their entire life cycle, meet the rigorous safety and performance requirements of the sector they will go into. The system can, for example, manage and track documentation related to regulatory approvals so that all necessary paperwork is up-to-date and readily available in case of audits or reviews.
In the medical device industry, this facilitation translates to the role of ensuring patient safety. By providing traceability throughout the entire PCB design and manufacturing process, PLM helps identify the root cause of any potential issues with a device, which allows for faster and more targeted recalls—reducing patient risk.
Taking a PCB design from concept to reality necessitates a deep understanding of design for manufacturability (DFM) principles. Back in time, DFM analysis happened late in the design cycle, which could lead to costly rework projects and, in the end, delays in the completion of products.
That isn’t as much of a problem today as it once was, courtesy of PLM solutions that bridge the gap between design and manufacturing by incorporating DFM tools and functionalities, which engineers can use to perform checks early in the design process to identify potential manufacturability issues before they become problematic. With the facilitation of open communication between designers and manufacturers, PLM ensures that PCBs are designed with manufacturability in mind, which reduces the need for rework and expedites time-to-market.
While the integration of PLM solutions with existing workflows can present challenges, the benefits far outweigh the initial hurdles. If companies can overcome such obstacles, they can unlock a new level of efficiency, collaboration, and innovation, previously unafforded by legacy systems and siloed tools. Integrated PLM solutions empower businesses to streamline workflows, reduce errors, accelerate time-to-market, and unlock a new wave of creativity to optimize designs for manufacturability. In challenging, increasingly competitive times, these advantages can be the difference between leading the pack and falling behind, and it is most important that companies do not give up at the first hurdle of integration.