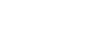
Manufactured products leave a trail of technical documentation behind them. Ranging from product specification and regulatory requirements to CAD drawings and manufacturing instructions, companies must maintain these documents throughout the product life cycle.
In this process, stakeholders must follow stringent documentation standards to produce safe and reliable products; discrepancies, no matter how minor, can result in miscommunication between teams, design flaws, manufacturing errors, and cost overruns that affect design phase efficiency and the final product's functionality. They may even pose a risk to consumers.
And so, in a time when demand for innovation is at its highest and time-to-market limited, this difficult task is being met by technological disruption, beckoning a new era of cross-functional collaboration.
Product lifecycle management (PLM) leans on interconnectivity, a staple of Industry 4.0, to synchronize data and information across platforms (AR, CAD, ERP, IoT, MES, and others) to create a digital thread. This thread provides a flexible but structured framework to bridge the gap between all key stakeholders and technologies, acting as the central nervous system of an ecosystem that puts collaboration and consistency on a pedestal. Through this digital thread, PLM resources enable collaboration between distant silos and coordinates disparate workflows into a framework that eases the burden of maintenance, increases accessibility to real-time data, and lessens the risks of mistakes in the documentation process.
Using the digital thread, PLM solutions collate information from silos to ensure documentation accuracy and continuity throughout a product’s life cycle through the following functionalities:
The integration of electronic design automation (EDA) and PLM resources also play a pivotal role in achieving consistency in product documentation and design data as it introduces standardized documentation that aligns components, symbols, and other elements, ensuring uniformity and accuracy across the board.
As part of their everyday role, electronic design engineers have to maintain precise documentation throughout the product life cycle. That precision is non-negotiable, and they leverage PLM systems to guarantee it. Here are a few examples of how:
These—and other—capabilities help engineers to corroborate transparent PLM documentation so that stakeholders from other silos have access to the most up-to-date information on one platform. That, and the integration of PLM resources with manufacturing execution systems (MES), reduces the likelihood of errors and misinterpretations and alleviates pressure, as it streamlines communication and facilitates the exchange of critical information between the lab and manufacturing floor seamlessly.
Quality assurance (QA) teams are strong proponents of top-quality documentation; they exhaust their efforts, ensuring data is recorded in real time and kept consistent across platforms in the PLM ecosystem. They do this by defining and enforcing engineering specifications, reviewing and approving documentation, implementing and monitoring quality control processes, training and supporting engineers, and auditing and reporting.
PLM systems can track and analyze parts throughout the product life cycle and assist in maintaining the design documentation, part specifications, technical drawings, and related data found in centralized repositories, which helps engineering teams track the usage and evolution of individual parts across various product iterations so that they, too, can ensure documentation remains synchronized with design changes from their end.
Additionally, through PLM’s facilitation of real-time collaboration across multiple silos, relevant stakeholders at every level of the process can access the most recent documentation and contribute insight for improved transparency and accountability of processes.
With technology changing, suppliers modifying their offerings, and geopolitical issues frustrating supply chains, companies often have to deal with component obsolescence, which threatens product continuity. PLM, which integrates with industry resources and supplier databases, monitors the lifecycle of each component used in product designs to identify potential issues ahead of time, helping companies plan mitigation measures—whether through redesign or procuring alternative parts.
Operations management can be used to enable communication between design and manufacturing teams in various ways.
Standardization and automation are paramount, with the establishment of templates and guidelines for documents like technical drawings or BOMs ensuring consistency and clarity while minimizing errors through automated data exchange between design and manufacturing systems. The use of digital signatures and version control improves traceability and accountability, too.
Operations managers can establish effective collaboration and communication through joint review meetings and dedicated company channels—Teams or Slack, for instance—and cross-training programs. These efforts will help disparate teams understand each other's needs, roles, and the documentation each contributes. The PLM system, which hosts these documents, can provide real-time data dashboards that help the teams visualize production metrics and identify potential issues early on in the manufacturing process.
Additional strategy:
Those who take the initiative and implement PCB design PLM systems will be ahead of the curve in years to come. PLM gives a clear pathway to achieving documentation excellence, which has become decisive for companies to stay ahead of next-generation challenges and ensure success in the evolving documentation landscape. For leaders considering investing in PLM integration, it offers several advantages:
Value of PLM:
In the longer term, PLM resources can facilitate sustainable growth by providing scalable document management solutions that support company expansion. On top of that, a reputation for consistent and high-quality documentation builds trust with customers and partners to the benefit of the brand, and PLM’s streamlined workflows and accelerated time-to-market confer a competitive edge and poise companies for sustained success.
Implementing a new system requires adherence to best practices. Executive support is imperative in any infrastructure-related venture as they can allocate the resources and commitment necessary for a successful go at it. Alongside executives, companies should put a change management strategy in place, providing comprehensive training programs to relevant teams to ease the adoption of the new system.
Developing a clear and detailed plan for data migration will facilitate an efficient transfer of existing documentation to the PLM system, which users can align with specific workflows and needs to maximize its effectiveness and enhance user acceptance.
Precise documentation is quintessential throughout a product’s life cycle, especially in PCB manufacturing. PLM systems are the golden ticket to achieving this accuracy through streamlined processes and heightened efficiency that bring data from disparate silos together in a centralized repository. However, companies must remember that documentation excellence is a continual process rather than a final destination. By implementing the listed best practices, keeping up with evolving regulations, and committing to ongoing improvement, they can make significant strides toward sustaining that excellence.
To elevate your PCB design standards and unlock unparalleled efficiency and innovation, look at Altium Enterprise Solutions, where we bring digital transformation to life with a comprehensive, digitally integrated electronic design solution for enterprises.