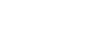
The printed circuit board (PCB) serves as the foundation upon which modern devices manage to function—it plays a critical role in electronics. From smartphones and laptops to lifesaving medical equipment and industrial control systems, PCBs direct the flow of electrons to enable the functionality that society increasingly depends upon.
However, with increased power and capability comes additional safety and quality considerations, and these intricate components, in particular, require a well-coordinated effort throughout the electronics supply chain to ensure they meet the standards. The expansive network of companies that maintain these standards is mission-critical in bringing electronic devices from concept to consumer, and each stakeholder has a responsibility to ensure the safety and quality of the final product.
PCBs are the backbone of this network, and PCB manufacturers sit at the forefront, responsible for meticulously crafting these essential components.
A successful outcome hinges on the collaboration of a well-coordinated team of stakeholders. Here are the key players:
One key element that fuses the stakeholders in the manufacturing process together is precision. The manufacture of safe and high-quality PCBs demands attention to detail that is not expected in many tasks. The following list presents some of the critical areas that PCB manufacturers must prioritize in their pursuit of excellence.
Every decision around materials, from base laminate to the surface finish, plays a pivotal role. PCB manufacturers must carefully select materials that meet rigorous industry standards established by organizations like the Association Connecting Electronics Industries (IPC). The chosen materials must also be suitable for the intended application. For instance, high-frequency applications necessitate materials with specific dielectric properties to ensure signal integrity and prevent overheating. In other cases, some applications may require specialized materials with flame retardancy or high thermal conductivity.
The quality of electronic components directly translates to the safety and functionality of the entire PCB. PCBs should only be populated with components sourced from reputable suppliers who adhere to stringent quality control measures and hold relevant certifications from organizations like Underwriters Laboratories (UL) or the International Electrotechnical Commission (IEC). These certifications provide assurance that components meet established safety and performance standards.
Each stage of PCB fabrication and assembly presents potential opportunities for the introduction of defects. To avoid such eventualities, PCBS must be manufactured using robust processes that prioritize quality control at each step; this could include the use of techniques such as automated optical inspections (AOI) and X-ray inspection to detect potential issues before they become major problems. Adherence to industry best practices like, among others, Six Sigma can also help minimize defects and increase quality consistency.
A comprehensive audit trail is essential throughout the supply chain. PCBs, especially, must be meticulously documented, with emphasis placed on tracking materials used, components sourced, and every step of the manufacturing process. This precise record-keeping becomes invaluable in the event of any safety or quality concerns as it assists companies in the swift identification and resolution of issues as they arise. If your company would like to level-up its paperwork game, traceability standards like IPC-1788 can provide a framework for the establishment of a robust documentation system.
Prior to shipping, to guarantee that they meet required specifications and function safely under various operating conditions, PCBs must undergo rigorous testing. Throughout the manufacturing process, teams should commit to thorough electrical and mechanical testing to make sure that the final product succeeds. These tests should include electrical continuity, shorts, opens, and proper functionality, as well as thermal and environmental tests, if necessary, according to the eventual application of the circuit.
With a focus on meticulousness in material selection, component quality, robust manufacturing processes, scrupulous documentation, rigorous testing, and open collaboration, PCB manufacturers can deliver not just a product but a foundation for safe and high-performing electronic devices that bolster brand reputation and loyalty in the saturated marketplace.
This focus on quality throughout the supply chain benefits all stakeholders. OEMs and CEMs, for example, receive PCBs they can confidently integrate into their final products, knowing they meet the required safety standards, and end users enjoy reliable devices that function as intended, free from hazards. In the end, a well-coordinated PCB supply chain promotes efficient production and helps to create a trustworthy position of excellence within the industry.
The impact of high-quality PCBs extends far beyond the immediate stakeholders. Consider a medical device manufacturer that relies on PCBs for critical equipment; if they are flawed, potential malfunctions could compromise patient safety and cause serious harm. On the other hand, perfectly manufactured PCBs ensure the precise functioning of devices to deliver lifesaving interventions. Similarly, in automotive and aerospace, where safety is paramount, high-quality PCBs are instrumental in the prevention of catastrophic failures.
The ethical implications are clear: PCB quality is not just about business success; it’s about safeguarding human well-being. By prioritizing quality over quantity, PCB manufacturers contribute to the development of reliable, trustworthy electronic devices that will continue to improve our lives in countless ways.
The future of PCB safety and quality likely lies in the gray area between continuous improvement and innovation. As the complexity of electronics deepens and further miniaturization occurs, the need for even stricter quality control measures will increase, so here are some potential areas for future development.
These advancements, when combined with a culture of quality throughout the supply chain, should pivot the PCB industry towards the continuous production of essential components to provide a safe and reliable foundation for the electronic devices that have become a part of our everyday lives. Needless to say, the future is bright, with the promise of a new era of miniaturization, increased functionality, and an unwavering commitment to both safety and quality.