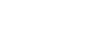
Testpoints play a crucial role in reducing PCBA testing and debugging time while increasing measurement reliability in automated systems. They help eliminate human errors and ensure accurate data collection directly from production batches.
Altium Designer's Testpoint Manager simplifies the testpoint assignment process, making it easier for PCB designers to integrate testpoints efficiently. Our latest whitepaper explores the theoretical importance of testpoints, covering optimization strategies, fault detection in automated testing, and best practices for reliable measurements. Additionally, it provides a step-by-step tutorial on using Testpoint Manager in Altium Designer, including configuration and assignment methods for an exemplary PCB design.
An integrated PCB editor along with real-time connection to multiple domains.
One interface. One data
model. Endless possibilities.
Effortlessly collaborate with
mechanical designers.
The world's most trusted
PCB design platform
Best in class interactive
routing
View License Options
Simple solutions to high-speed design challenges.
The world’s most trusted PCB design system.
The world’s most trusted PCB design system.