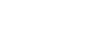
The PCB industry has been going through a period of transition over the past couple of decades, mainly driven by the relentless pace of technological advancement and the increasing complexity of modern devices. PCBs themselves have also evolved in recent times, having become the key to an intricate neural network powering everything from consumer devices to critical infrastructure. This escalating complexity demands a holistic, integrated approach to management that goes beyond traditional siloed operations.
Product lifecycle management (PLM) is arguably the best emergent technology for this task. It is the indispensable framework for overcoming existing and upcoming challenges. By providing a unified platform for managing product data and processes, PLM gives companies visibility into the entire PCB lifecycle, from conceptualization to end-of-life. It’s a comprehensive perspective that allows companies to make informed decisions, optimize operations, and accelerate time-to-market.
Beyond operational efficiency, PLM is considered a very agile strategic catalyst for innovation. This innovative system enables a collaborative environment that accelerates design iterations, facilitates rapid prototyping, and supports the development of groundbreaking products. Such features are crucial for companies looking to compete at the highest levels, but this is not all PLM facilities; it also helps teams to ensure product quality, traceability, and compliance. PLM mitigates risks, safeguards brand reputation, and builds customer trust.
The financial implications of PLM are equally compelling. By streamlining processes, eliminating waste, and optimizing resource allocation, PLM could deliver a substantial return on investment. Additionally, as sustainability becomes a critical business imperative, PLM enables organizations to track environmental impact, comply with regulations, and identify opportunities for eco-friendly design.
Implementing PLM is a strategic transformation that requires a holistic approach encompassing people, processes, and technology. If organizations choose to align their business objectives with PLM capabilities, they will likely unlock their full potential and secure a competitive advantage.
The following are the key benefits that companies find after adopting and integrating PLM:
Here’s a breakdown of the key stages involved in implementation. The scenario will, of course, be unique to each company, but the following table gives you the gist.
Stage |
Description |
Potential Challenges |
Needs Assessment (1─2 months) |
Analyze current PCB design and manufacturing processes to identify pain points and inefficiencies and define desired implementation outcomes. |
Difficulty in quantifying the impact of current inefficiencies and lack of alignment among stakeholders on project goals. |
Software Selection (2─3 months) |
Evaluate PLM solutions on the market based on features, functionality, and compatibility with existing systems. Consider factors such as budget, scalability, and ease of use. |
Complex evaluation process with numerous vendors and features to consider; potential difficulty in defining specific needs and requirements upfront. |
Data Migration (2─6 months) |
Plan the process of extracting data from existing design, manufacturing, and ERP systems. Transform and cleanse data to ensure consistency and accuracy. Load the data into the PLM platform. |
Data inconsistency and incomplete records across different systems; compatibility issues between legacy systems and the PLM platform. |
User Training (1─2 months) |
Develop training programs to educate all relevant personnel on using the PLM system effectively. Training should cover core functionalities, workflows, and best practices. |
User resistance to change and new workflows; inadequate training materials or insufficient training time allocated. |
Change Management (ongoing) |
Develop a communication plan to keep stakeholders informed about the PLM implementation process. Address user concerns and provide ongoing support to ensure user adoption. Continuously monitor and improve PLM workflows based on user feedback. |
Lack of clear communication or resistance to new ways of working; difficulty in managing organizational change and overcoming ingrained habits. |
As time passes, new devices need more and more intricate PCBs to accommodate the integration of multiple components and functionalities; for design, manufacturing, and assembly, this is tough work full of challenges.
Following on from the increased number of PCBs necessary, manufacturers now also face pressure to introduce new products faster and faster. But, at the same time, they are expected to maintain high-quality standards.
The PCB industry is, as with most industries, highly dependent on global supply chains, which makes it vulnerable to disruptions caused by factors such as natural disasters, economic fluctuations, and geopolitical events.
Unfortunately, the price of just about everything is rising. With that in mind, increasing material costs, labor expenses, and energy consumption are impacting PCB manufacturers’ bottom lines pretty drastically.
The electronics industry is subject to a myriad of regulations that differ depending on region and tend to circle environmental, safety, and quality standards. Adherence to these regulations is one of the most important factors in PCB creation—falling foul of them can limit market access and result in costly penalties.
The PCB industry is going through a transformative period that, when dissected, is characterized by more intricate designs, shorter timeframes, increasing supply chain disruption, costs, and even more stringent regulations. For companies to thrive in this environment, PCB manufacturers must adopt a holistic approach to product life cycle management.
PLM offers precisely that—a comprehensive solution that unifies product data and improves processes to make more efficient collaboration between disparate silos. By integrating PLM into operations, PCB companies can accelerate time-to-market, improve product quality, reduce costs, and ensure regulatory compliance while also making teams work more effectively.
It’s a choice, yes. But it’s also a strategic imperative. If you want to position your company for long-term success and gain a competitive edge, PLM should be at the top of your shopping list.