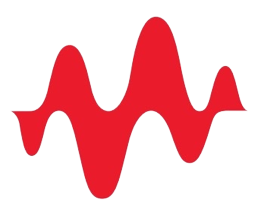
Reduce Design Cycle Risk and Improve Reliability With Easy and Frequent Power Network Analysis
Industry Fact:
“In the early days of Printed Circuit Board (PCB) design, power delivery was not a prominent consideration. With a high-speed design prevalent in the present context…performance should be anticipated early in the PCB design and tailored to satisfy the device specification with lower voltage, higher current, and tighter noise margins. The objective of power delivery is to supply a clean and stable voltage to the core devices in a complex product design.”
Embedded Computing Design, March 2022
Industry Objective:
An electronic circuit board requires one or more power supplies to function properly. These power supply "rails" are a network of traces that run across the PCB. This network is designed to ensure that each device on the PCB gets a clean and stable voltage at the required level. The power supply network should be able to handle the simultaneous switching of signals or larger dynamic currents. For example, the power network should remain stable when the processor cores power up from "sleep." It is also imperative to ensure that the power network accommodates high-current devices, signal pathways, and PCB subsections without causing excessive voltage (IR) drop, which can damage the board itself over time.
How This Affects You:
The increased integration of electronics requires lower voltages with tighter noise margins. As logic voltage levels continue to decrease, even the most innocuous voltage drop can result in odd signal integrity issues, strange circuit behavior, or intermittent failure. Additionally, if the power network on the PCB is not properly designed and routed, high-current pathways may function fine, but they may also create excessive heat on the board. Over time, power networks that are not well-optimized can experience severed traces, delaminated boards, and a variety of intermittent field failures.
As electronic devices become smaller and more powerful, the design of their power supply networks has become increasingly important. Early PCB designs paid little attention to these networks, but today's increased power, speeds, and decreased noise margins require a different approach. Best-in-class electronics design companies mitigate risk, ensuring on-time manufacturing and trouble-free field performance by embracing one-click analysis of the power network early and often from within their PCB design tool itself. The alternative is to risk delayed time to volume, reputation-harming failures, or worse.
If You Find Yourself Needing to:
Then This Leads to:
What If You Could:
What You Can Do:
PCB Designers can remove the guesswork from assessing a PCB's power delivery network through a DC Power Integrity (PI-DC) simulation tool, which analyzes a board design's DC performance based on its electrical and physical properties. Power Analyzer by Keysight Technologies, available in Altium Designer, provides an easy way to analyze your power distribution network.
Provided as a downloadable Altium Extension, the Power Analyzer integrates directly with Altium Designer to allow PI-DC simulation and analysis of the current PCB project. Since Power Analyzer runs within Altium Designer, there are no manual data import/export requirements, data conversions, or separate applications. PCB designers can run the Power Analyzer from the schematic or PCB editor, set the desired test parameters, and run a simulation. The results are primarily delivered through 2D/3D modeling of the circuit board copper layout, allowing a quick assessment of the results and the opportunity to perform exploratory 'what if' testing of the PCB layout design.
What It Is:
Use the Heatmap tab of the Power Analyzer panel to change the simulation results presented on the PCB. Here, the voltage drop results are displayed.
The logarithmic current density heatmap shows an area of concern.
Power Analyzer automatically details violations. This image shows a via current violation.
Probes can measure voltage or current as an absolute value or the difference between two locations.
Bringing Altium 365 into the Mix:
In addition to Altium 365’s version-controlled storage of your design data, the collaboration capability provides designers with an enhanced ability to comment and share design or BOM information.
The workspace provides a single location for all supply chain-aware electronic components, including schematic symbols, simulation models, PCB footprints, device parameters, part providers, supplier information, 3D views, and more.
Conclusion:
Elevating power supply network analysis to a level consistent with other design aspects, such as signal integrity, layer stack design, and BOM analysis can pay huge dividends by reducing the risk of prolonged product development time. Power analysis will support on-time manufacturing and trouble-free field performance of high-quality products while lessening the burden on PCB designers.