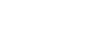
Noise on power supply lines can be a significant headache, adversely affecting devices’ performance, causing reliability issues, and leading to unexpected system behavior. When designing an electrical device, the designer needs to consider two questions.
Noise generally comes in two forms: common-mode and differential-mode. When we refer to common-mode noise, we mean a specific form of noise that exists on two conductors with same polarity, frequency content, and magnitude. There is one component that can be used to suppress this noise: a common-mode choke. In this article, we'll look at how to select common-mode choke coils for use in power systems to help suppress common-mode noise.
Common-mode noise on power supplies entering a device is typically caused by large discharge currents coupled onto long wires, the presence of unwanted radio frequency emissions, or switching devices such as inverters and motors connected to the power supply. The device itself can also create common-mode noise through switching components and unshielded circuits. Common-mode noise generated through the power lines is a particularly critical problem in switched-mode power supply design. Managing these emissions is crucial for protecting devices connected to such power sources and to meet regulatory requirements.
Common-mode noise can be visualized by looking at a noise signal on two conductors. Regardless of the cause, all common-mode noise will have some the same characteristics:
These are ideal characteristics of common-mode noise; in reality noise is rarely only common-mode, and generally common-mode noise will coexist with differential-mode noise. However, we care more about common-mode noise from an EMI/EMC perspective because it can be much "louder" (more intense) than differential mode noise. Therefore, it will be a bigger contributor to EMI problems, both conductive and radiated. Since common-mode noise that is radiated from a board begins as common-mode currents, we need to filter or otherwise suppress common-mode noise to ensure low noise is radiated and conducted around a PCB layout.
The problem with electromagnetic interference and switching transients is that they equally affect all power lines going in and out of a device and unaffected by differential shielding or filtering. Discrete inductors and capacitors can be used to implement a front end low pass filter instead of a common-mode choke. While these on their own are potentially a low-cost solution, it may necessitate the requirement for main transformer flux bands or shields to block common-mode currents within the transformer due to parasitic capacitance between the primary and secondary coils. This adds cost and complexity and can drive down reliability.
An alternative solution is to use a common-mode choke, which essentially also acts as an electrical filter that blocks high-frequency noise common to two or more power lines while allowing the desired DC component on the line to pass through. The most common use for common-mode chokes is to filter out conducted switching and RF noise produced by switched-mode power supplies. Where common-mode noise exists on a power supply, a common-mode choke can use the voltage fluctuations to create opposing magnetic fields concentrated in a core that cancels each other out and dissipates the energy in the form of heat. This is achieved by winding the power lines around a common core, as shown below.
The choke is made with two identical windings around a common core, which is normally made form a ferrite material. This ensures the magnetic field will couple between the coils with very high mutual inductance. Where the windings are used for the lines of a power supply, the current flowing in both will be the same. These two lines will create an equal and opposite magnetic flux in the common core that will cancel each other out, creating, in theory, a zero net flux in the core. This means that the magnetic flux within the core will not be dependent on the current flowing through the power lines, and so will not be limited by saturation of the core. The DC power supply will effectively see negligible inductance or impedance. However, the high-frequency noise currents will see a high impedance due to the windings’ common inductance and hence be attenuated. Choke devices by their very nature are significantly more reliable components than capacitors.
In simple terms, a choke is a magnetic inductor used to block or limit unwanted high-frequency signals while allowing direct current to pass through unimpeded. When choosing the right choke for your application, three factors need to be considered.
A good rule of thumb is that the lower the frequency that the choke is required to filter, the physically larger the choke will need to be. Depending on your choke’s essential characteristics, components can be found in traditional through-hole wire coils and encapsulated components or in surface-mount packages. The surface mount variants that are ideal for simple board construction are available that are specifically designed to eliminate AC line-conducted common-mode noise across a broad range of frequencies, with up to 1500 V isolation and carry up to 15 A. This makes them perfect for switch-mode power supplies.
Common-mode chokes are typically available in two different types: RF (radio frequency) and AF (audio frequency). The primary difference between the two is the material used to construct the choke’s core. RF chokes use a powdered iron or ferrous bead core while AF chokes use a solid magnetic iron core. The solid ferrite cores typically have a higher saturation flux density and a higher current rating than powdered iron cores. Which one you require will depend on the noise’s lower range frequency, though for DC power supplies, the AF chokes are usually preferred.
If you are unsure of the real-world filtering characteristics you need, a good rule of thumb is to select the biggest choke that will physically fit the available board space to get the largest possible choking impedance and hence the maximum suppression of common-mode noise.
Ferrite toroid cores offer the most effective core shape, with maximum magnetic coupling between windings and minimum leakage inductance. However, the core material, the high number of windings, and a plastic mounting base make them a more expensive option. Their maximum voltage rating is also limited by the isolation between windings, typically below 1500 V. Ferrite ‘E’ or ‘U’ core shapes offer better isolation between windings of up to 3000 V.
The data sheet limits for a choke are generally governed by the components allowable heating limits. If the choke is going to be exposed to significant common-mode noise levels, then don’t forget to take thermal management into account as part of the design process.
The performance of any ferrite choke is governed by core saturation effects. If a chock is presented with noise with a significant peak current or a high-voltage, high-energy common-mode surge, then the core can saturate, and the surge voltage will pass through. The choke’s ability to cope will depend on its maximum current rating and the nature of any surge. If the device in question will be exposed to such surges, then separate surge protection should be designed in addition to the common-mode choke.
If you've implemented best practices in your PCB layout and you find you'll need a common-mode choke in your design, you can increase your common-mode noise immunity using the component selection and routing features in Altium Designer®. Once your design is ready for a thorough design review and manufacturing, your team can share and collaborate in real time through the Altium 365™ platform. Design teams can use Altium 365 to store component data, share manufacturing documentation, and project files through a secure cloud platform and in Altium Designer.
We have only scratched the surface of what’s possible with Altium Designer on Altium 365. Start your free trial of Altium Designer + Altium 365 today.