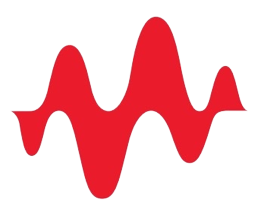
Embedded systems design and development is a broad area of electronics, spanning from developing code for an Arduino to designing custom computing systems with huge I/O count. On the more advanced end, where we see complex embedded systems for imaging, radar, modular computing, and edge computing, power regulator module design is a major determinant of system performance as it must ensure power integrity and signal integrity. These systems are the big enablers of new applications being pursued by large companies and startups.
Whether you design your own external regulated power supply, or place a power regulator and multiple supplies directly onto your board, there is a common set of power integrity specifications to follow to ensure stable power delivery to these digital systems. Should you use an external power supply, place onboard power regulation, or somewhere in between, and how does this change in an advanced embedded system with high compute?
All embedded systems use a primary processor to implement compute operations and run an embedded application or OS. A simpler embedded system (think Arduino or Raspberry Pi) may only have one or two core voltages for the main processor. If you look at something more advanced, like an FPGA or GPU, there will be multiple core voltages at almost every standard level (3V3, 2V5, 1V8, 1V2, and so on). An embedded system power supply has to provide voltages at all these levels across the entire system.
Power supplies for embedded systems normally must provide the primary input power at a standard voltage, and the power regulation strategy on the PCB provides power at the particular core voltages. A power tree showing this strategy is outlined below.
Typically the main power input will be a switching regulator as it will need to provide current to the entire system. In the case where this is much too large to place on a single PCB, a large regulator module can be used to provide stable power at the highest voltage level. This is a typical strategy taken in edge computing, automotive, aerospace, telecom, and modular embedded systems. These separate power supplies could be rack-mounted or chassis mounted in the case of modular embedded.
The various core voltages are provided by their own power regulators, each of which must be designed to meet particular operational requirements:
Stable voltage/current output: Your output should have as little noise as possible. This involves suppressing ripple, suppressing or filtering switching noise (e.g., in DC->DC conversion), and testing regulator modules for stable feedback during operation.
Maximum output current: As embedded systems scale, the current demand increases, and each regulator will need to provide high current at the required core voltage.
EMI/EMC compliance: EMI will need to be considered in embedded systems, particularly in new applications operating in electrically harsh/noisy environements. Industrial, automotive, and aerospace bring risk of transients (ESD) and power surges at the power input, and the system should have high enough withstand voltage to ensure reliability.
The guidelines for embedded power supply layout follow two sets of guidelines that are relevant for power supplies generally, as well as for high-speed PCB layout. The table below summarizes some of the important layout practices related to component selection and PCB stackup design to ensure power integrity in embedded systems.
|
|
|
|
|
|
For the power regulator circuits and modules, some simple guildelines will help ensure EMI/EMC compliance. Make sure power regulator layouts are tight with minimal area, use ground in the stackup below the regulators, and use large polygons to provide high current to processor packages. In terms of power management, PMICs with ENABLE pins and PGOOD pins can be used for specific components or subsystems, allowing the primary processor to monitor these components and turn these off when they are not in use.
For the other aspects of on-board design for power delivery in embedded systems, make sure you use plane layers, sufficient decoupling on each rail, and place high-frequency bypass caps close to VDD/GND pins of ICs to compensate for any lack of on-die/in-package capacitance.
Simulations are very important for identifying power integrity problems that might cause the system to fail in terms of DC power delivery, as well as power integrity problems that later form signal integrity problems. Power integrity simulations must therefore be focused in two areas:
Finally, power integrity simulations can be performed in the schematic and in the PCB layout. Starting with a simple model in the schematic is useful for identifying or estimating the required number and type of capacitors/plane capacitance needed for power integrity using SPICE simulations. This is a great way to narrow down to specific groups and numbers of components, as well as transfer impedance between different rails at the same voltage level.
To verify whether the size and expanse of power rails is sufficient for power delivery at the target average current, DC power integrity simulations can be used. These simulations cannot determine the PDN impedance, but they can help you identify spots in the PCB layout that will require more copper to provide the target current without exceeding an allowed current density.
Identifying power integrity problems is important for ensuring stable power and signal integrity in embedded systems, and you’ll need design tools that can help you prevent these problems when designing an embedded system power supply. Altium Designer contains all these features and many more in a single program. Altium Designer includes a powerful PDN analyzer as an add-on that is conveniently available within the program.
Now you can download a free trial of Altium Designer if you’re interested in learning more about its power integrity and layout tools. Talk to an Altium expert today to learn more.