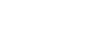
The question of what PCB thickness to use might seem quite basic, but in many systems, it is an important mechanical consideration. In some designs, you are forced into a thicker board as the layer count begins to increase unless you take an HDI approach. In other designs, such as Flex designs, there is no standard or common thickness because all stacks of designs in these domains will be customized.
No matter what total thickness and tolerance value you decide to use, that value is used to select or design a stackup for your PCB. For designers taking ownership over their stackup design, the PCB laminate material thickness on each layer will have to be selected to hit an overall PCB thickness target. Otherwise, manufacturers will offer standard stackups and fixed thicknesses with a known tolerance. This article will cover a range of standard thickness options from manufacturers, as well as some non-standard PCB thickness values that can be found in commercial products.
The most commonly used PCB stackup thickness is the 1.57 mm stackup, or 62 mil thickness in imperial units. The typical tolerance for this stackup is +/- 7 mil or less, a value that is attainable for most standard materials in PCB stackups. The reason this thickness has become the de facto standard is largely historical and is based on how PCBs were taped out before the development of computers and CAD software.
Today, PCB manufacturers still support this thickness value for PCB stackups, including in their standard stackup options. In fact, if a thickness value is not specified for a PCB manufacturing order, it is generally assumed that the PCB will be approximately 62 mil thick. This value applies after accounting for surface finish plating, solder mask thickness, and even conformal coatings if applicable.
The standard PCB thickness value also applies up to high layer counts, which inevitably requires dielectric layers to get quite thin. PCB laminate material manufacturers offer a range of thicknesses for their materials, which will allow a designer to get quite close to this standard thickness value if it is required in a design. When specifying a particular material in a stackup, make sure to get the datasheet and determine what thickness values are available. Some materials will not be available above or below a certain thickness limit.
While 1.57 mm thickness is certainly the most popular standard thickness value, it is not the only value used in many designs or offered by manufacturers. These other standard thickness values may be a multiple of 1 mm or 1.5 mm, both offered as a standard stackup by a PCB fabrication house or used as a design target for a PCB designer. In mechanical designs that follow the metric system, 1 mm multiples are also an attractive option as they have nice round units and well-understood tolerances.
Standard stackups often target 1 mm and 2 mm thicknesses, typically up to 10 or 12 layers. These designs may incorporate thicker internal dielectrics so that controlled impedance designs will not have trace widths that are too small when routed as striplines. If a thinner PCB stackup at these layer counts is desired, you will then be forced to use thinner dielectrics in all layers.
As an example, see the image below. This PCB stackup uses multiple laminations for blind and buried vias. The total thickness is larger than the standard board thickness, reaching a value of 81 mils. The particular application for this design is an RF sensor with multiple digital interfaces, which requires the internal layers to be allocated to high-speed and low-speed digital signals.
10-layer PCB stackup with total thickness of 81 mils.
Some products and types of PCB designs do not follow a standard PCB stackup thickness value. Instead, the selection of PCB layers and per-layer thickness requirements creates a non-standard PCB thickness value. Over the years, I have encountered several examples:
Flex and rigid-flex PCBs
Ceramic core PCBs
Metal core or metal-backed PCBs
Backplanes with thick dielectric layers
PCBs with many sequential laminations
Printed ink electronics
Additively manufactured PCBs
These PCBs could technically have any thickness value as long as that thickness can be produced from commercially available materials with the relevant fabrication process. In backplanes, for example, it is not uncommon to see PCBs reach large thicknesses, even with high-density daughter board connectors present in the design. At the other end of the spectrum, substrates for printed ink electronics and flex PCBs tend to be very thin due to the thin base materials used to build these designs.
An example rigid-flex layer stackup is shown below, which uses many thin polyimide layers and rigid prepreg layers. As a result the total stackup thickness in each region does not follow a standard value listed above.
You wouldn't use an integrated circuit without checking the datasheet first, so why would you take a different approach with PCB laminate materials?
Before designing your PCB stackup, take some time to learn about a few of the common materials used in many PCBs. I think it's always good to have a few materials that you prefer for certain types of designs. This way, you can at least spec something into a prototype or request something similar from a materials vendor. Many materials vendors supply this information in their datasheets or in tables available on their websites.
Some of the common materials vendors and products designers should be aware of include:
Isola FR406, FR408, and 370HR
Rogers 3000 series or 4000 series PTFE laminates, and 4450 Bondply
Shengyi FR4 materials and high-speed materials
Iteq FR4 materials and high-speed materials
Panasonic Megtron for high-speed digital PCBs
AGC low DK materials and ultra-thin materials
There is also a host of HDI materials that can be used in rigid PCBs and IC substrates. I have always kept these datasheets and material data tables handy on my computer whenever I need them for a project.
The documentation you will need for your PCB stackup is simple and can be provided in a standard fabrication drawing. Make sure you include your PCB thickness in a stackup drawing with an allowed tolerance value, such as the values I listed above. If specific materials are being selected and PCB layer thickness values are known or have been calculated, state these in the fabrication drawing. Finally, if you're willing to accept alternative materials, cite the relevant IPC slash sheet in your PCB fabrication notes, as well as any relevant acceptable dielectric constant range.
Auto-generated manufacturing drawings in Altium Designer Draftsman
Whether you need to build reliable power electronics or advanced digital systems, use the complete set of PCB design features and world-class CAD tools in Altium Designer®. To implement collaboration in today’s cross-disciplinary environment, innovative companies are using the Altium 365 platform to easily share design data and put projects into manufacturing.
We have only scratched the surface of what’s possible with Altium Designer on Altium 365. Start your free trial of Altium Designer + Altium 365 today.