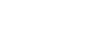
Sie möchten Ihren Prozess schnell abwickeln oder arbeiten am Design einer Hochgeschwindigkeits-Leiterplatte? Ganz egal, woran Sie arbeiten, durch die Anwendung bewährter Designverfahren können Sie die ordnungsgemäße Funktion Ihres Designs sowie eine Produktion im großen Maßstab sicherstellen. In diesem Leitfaden haben wir einige der wichtigsten Richtlinien zum Thema Design und Layout von Leiterplatten zusammengestellt, die für die meisten modernen Leiterplatten gelten. Bei speziellen Designs kommen möglicherweise zusätzliche PCB-Layoutrichtlinien zum Einsatz; die hier dargestellten PCB-Layoutrichtlinien sind jedoch für die meisten PCB-Designs ein guter Ausgangspunkt.
Die folgenden Richtlinien konzentrieren sich auf einige Kerngebiete und bieten Hilfestellung für die Bereiche Leiterbahnen, Herstellbarkeit, grundlegende Signalintegrität und Bestückung:
Zu Beginn eines neuen Leiterplatten-Designprozesses vergisst man leicht die wichtigsten Designregeln, die jedoch maßgeblich für das Projekt sind. Werden beispielsweise bestimmte grundlegende Abstandsanforderungen frühzeitig bestimmt, können Verschiebungen von Komponenten und Änderungen am Routing im weiteren Verlauf großteils verhindert werden. Aber wie gelangen Sie an diese Informationen?
Gute Hersteller stellen die Funktionalitäten ihrer Produkte normalerweise online oder in einem Dokument zur Verfügung und sind somit Ihre erste Anlaufstelle, um diese Daten zu eruieren. Falls diese Informationen auf der Website des Herstellers nicht ersichtlich sind, senden Sie einfach eine E-Mail an den Hersteller und bitten um Auskunft. Idealerweise sollten Sie diese Informationen noch vor Beginn der Komponentenplatzierung erfragen. Im selben Zuge sollten Sie zudem Ihren Plan für den Lagenaufbau zur Überprüfung einreichen oder alternativ die standardmäßigen Stackup-Daten des Herstellers ermitteln und verwenden.
Sobald Sie die Funktionalitätenliste des Herstellers gefunden haben, sollten Sie diese Daten mit den Zuverlässigkeitsstandards der Branche vergleichen, mit denen Sie arbeiten (Klasse 2, Klasse 3 oder ein spezieller Standard). Sobald diese Punkte festgelegt sind, sollten Sie sich an den eher konservativen Beschränkungen für das Design-Layout orientieren, um Herstellbarkeit und Zuverlässigkeit sicherzustellen. Diese Parameter können Sie dann in Ihre Regeln für das PCB-Design integrieren.
Im Laufe des Layout-Prozesses helfen Ihnen die Designregeln dabei, Designfehler, die Probleme bei der Herstellung und Bestückung nach sich ziehen könnten, größtenteils zu vermeiden. Nach der Festlegung der Designregeln können Sie mit der Platzierung der Komponenten beginnen.
Die Platzierung der Komponenten im PCB-Layout-Designprozess ist sowohl Kunst als auch Wissenschaft und erfordert strategische Überlegungen hinsichtlich der optimalen Nutzung der verfügbaren Fläche. Das Ziel bei der Komponentenplatzierung ist die Entwicklung einer Leiterplatte, die einfach geroutet werden kann und idealerweise mit möglichst wenigen Lagenübergängen auskommt. Darüber hinaus muss das Design den Designregeln entsprechen und die Grundvoraussetzungen für die Platzierung unbedingt erforderlicher Komponenten erfüllen. Es kann schwierig sein, alle diese Anforderungen zu erfüllen, doch ein einfacher Prozess kann einem PCB-Designer helfen, Komponenten zu platzieren, die diesen Anforderungen entsprechen:
Wenn Sie die ersten beiden Punkte befolgen, ergeben sich weniger Probleme beim übrigen Layout und übermäßige Überschneidungen in Bezug auf das Routing können vermieden werden. Darüber hinaus sorgen Sie damit für eine rundum moderne Gestaltung Ihres Layouts, bei dem ein zentral positionierter Prozessor zur Bereitstellung der Daten an alle anderen Komponenten entlang des Leiterplattenrandes dient.
Nachdem alle Komponenten platziert wurden, steht im nächsten Schritt das Routing der Stromversorgung, Masse und Signalleiterbahnen an, um klare und ungestörte Signalpfade zu gewährleisten. Die folgenden Richtlinien sollten Sie während dieser Phase beachten:
Üblicherweise werden Stromversorgung und Masse auf zwei inneren Lagen platziert. Bei einer zweilagigen Leiterplatte ist dies allerdings schwierig. Die einfache Lösung ist daher, eine große Massefläche auf einer Lage anzubringen und die Signale und Versorgungsleiterbahnen auf der anderen Lage zu routen. Bei einer vierlagigen Leiterplatte oder einer Leiterplatte mit noch mehr Lagen sollten Sie Masseflächen verwenden und nicht versuchen, Masseleitungen zu routen. Für Komponenten, die direkt an die Stromversorgung angeschlossen werden müssen, wird empfohlen, für jedes Netzteil gängige Schienen zu verwenden, wenn es keine Versorgungsfläche gibt. Stellen Sie sicher, dass Ihre Leiterbahnen breit genug sind (100 mils bei 5 bis 10 A) und vermeiden Sie Verkettungen von komponentenübergreifenden Versorgungsleitungen.
Oft wird empfohlen, die Platzierung auf den Lagen in jedem Fall symmetrisch zu gestalten. Für die Fertigung ist diese Vorgehensweise allerdings nicht zwingend erforderlich. Bei großen Leiterplatten kann dies relevant sein, um die Wahrscheinlichkeit des Verformens zu verringern; bei kleineren Leiterplatten ist dies jedoch kein Problem. Konzentrieren Sie sich stattdessen auf die Zugänglichkeit der Stromversorgung und Masse und stellen Sie sicher, dass alle Leiterbahnen über einen einwandfreien Rückpfad verfügen, der direkt an die nächstgelegene Massefläche gekoppelt ist. Im Anschluss können Sie sich mit der optimalen Symmetrie des Lagenaufbaus befassen.
Im nächsten Schritt geht es um die Verbindung Ihrer Signalleiterbahnen, um die Signale in Ihrem Schaltplan entsprechend zuzuordnen. Die bewährten Verfahren für PCB-Layouts sehen vor, wo immer möglich kurze, direkte Leiterbahnen zwischen Komponenten zu verlegen. Bei größeren Leiterplatten ist dies allerdings nicht immer praktikabel. Wenn aufgrund der Platzierung Ihrer Komponenten ein horizontales Routing von Leiterbahnen auf einer Seite der Platine erforderlich wird, sollten Sie die Leiterbahnen auf der gegenüberliegenden Seite immer vertikal routen. Dies ist eine von vielen wichtigen Designregeln bei der Arbeit mit zweilagigen Leiterplatten.
Designregeln und Layout-Richtlinien werden bei zunehmender Anzahl der Lagen im Lagenaufbau immer komplexer. Sie müssen als Teil Ihrer Routing-Strategie auf alternierend horizontale und vertikale Leiterbahnen setzen; es sei denn, sie trennen jede Signallage durch eine Referenzebene. Bei sehr komplexen Leiterplatten für spezialisierte Anwendungen verlieren die vielzitierten Best Practices für PCBs oftmals Ihre Gültigkeit und Sie müssen stattdessen PCB-Design-Richtlinien befolgen, die speziell auf Ihren Anwendungsfall ausgerichtet sind.
Bei PCB-Layout-Designs dienen Leiterbahnen zur Verbindung von Komponenten. Doch wie breit sollten diese Leiterbahnen sein? Die erforderliche Breite von verschiedenen Signalen hängt von drei potenziellen Faktoren ab:
Bei Leiterbahnen ohne spezielle Anforderungen in Bezug auf Impedanz oder Hochstrom ist eine Leiterbahnbreite von 10 mil für die allermeisten analogen und digitalen Schwachstrom-Signale ausreichend. Die Leiterbahnen von Leiterplatten, die über 0,3 A führen, müssen hingegen breiter angelegt sein. Um dies zu überprüfen, können Sie mithilfe des Nomogramms IPC-2152 die richtige Leiterbahnbreite Ihres PCB-Designs für die erforderliche Stromkapazität und Temperaturbegrenzung bestimmen.
Die Massefläche kann als großer Kühlkörper fungieren, der die Wärme gleichmäßig über die gesamte Leiterplatte transportiert. Wenn also eine bestimmte Via mit einer Massefläche verbunden ist, wird durch Entfernen der Thermal Pads auf dieser Via Wärme zur Massefläche geleitet. Dies ist besser, als die Wärme in der Nähe der Oberfläche einzuschließen. Wenn die Durchkontaktierungskomponenten allerdings mittels Wellenlöten auf der Leiterplatte montiert werden, kann das ein Problem darstellen, da in diesem Fall die Wärme in der Nähe der Oberfläche eingeschlossen bleiben muss.
Eine Wärmefalle ist eine PCB-Layout-Designfunktion, die sicherstellt, dass eine Leiterplatte in einem Wellenlötverfahren hergestellt werden kann. Sie ist also eine wichtige Voraussetzung für Durchkontaktierungskomponenten, die direkt mit den Flächen verbunden sind. Da es schwierig sein kann, die Prozesstemperaturen aufrechtzuerhalten, wenn es sich bei einer Durchkontaktierung um einen Lötpunkt direkt auf einer Fläche handelt, wird der Einsatz von Wärmefallen empfohlen, um die Aufrechterhaltung der Löttemperatur sicherzustellen. Die Idee hinter der Wärmefalle ist einfach: Sie verlangsamt die Geschwindigkeit, mit der die Wärme während des Lötens in die Fläche abgeleitet wird. So werden kalte Lötstellen vermieden.
Einige Designer werden Ihnen empfehlen, Wärmefallen für alle Vias oder Löcher zu verwenden, die mit einer internen Masse- oder Versorgungsfläche verbunden sind – selbst wenn es sich dabei nur um ein kleines Polygon handelt. Dieser Ratschlag ist jedoch oft zu weit gefasst. Ob Sie eine wärmeabführende Durchkontaktierung benötigen, hängt von der Größe der Kupferfläche oder des Polygons ab, die bzw. das eine Verbindung auf der internen Lage herstellt. Dies sollten Sie von Ihrem Hersteller prüfen lassen – und das noch bevor Sie die Produktion Ihrer Leiterplatte in Auftrag geben.
Es gibt einige Routing-Richtlinien zur Gruppierung und Trennung von Komponenten und Leiterbahnen, um ein einfaches Routing zu gewährleisten und dabei elektrische Störungen zu vermeiden. Diese Gruppierungsrichtlinien sind auch im Sinne des Wärmemanagements hilfreich, da Sie unter Umständen Hochleistungskomponenten voneinander trennen müssen.
Einige Komponenten werden am besten in einem zusammengefassten Bereich im PCB-Layout-Design platziert. Grund dafür ist, dass diese Komponenten möglicherweise Teil eines Schaltkreises sind, also nur miteinander verbunden werden müssen. Es ist also nicht notwendig, die Komponenten auf verschiedenen Seiten oder Bereichen der Leiterplatte zu platzieren. Beim PCB-Layout geht es dann um das Entwerfen und Anordnen einzelner Gruppen von Schaltungen, sodass diese mühelos anhand von Leiterbahnen miteinander verbunden werden können.
Viele Layouts verfügen gleichzeitig über analoge und digitale Bauteile. In diesem Fall muss verhindert werden, dass Störungen zwischen digitalen und analogen Komponenten auftreten. Vor Jahrzehnten wurde dies noch so gehandhabt, dass Masse- und Versorgungsflächen in verschiedene Bereiche aufgeteilt wurden. In modernen Leiterplattendesigns ist dieser Ansatz jedoch nicht mehr zielführend. Leider wird diese Vorgehensweise immer noch in Richtlinien zum Design von Leiterplatten vermittelt. Dadurch kommt es oft zu ungeeigneten Routing-Praktiken, die elektromagnetische Störungen verursachen.
Verwenden Sie stattdessen eine vollständige Massefläche unter Ihren Bauteilen und unterteilen Sie die Massefläche nicht physisch in einzelne Abschnitte. Achten Sie darauf, dass alle analogen Komponenten bei gleicher Frequenz gruppiert werden. Zudem sollten alle digitalen Komponenten in einem Bereich zusammengefasst werden. Das bedeutet, dass jeder Komponententyp einen anderen Bereich über der Massefläche im PCB-Layout-Design belegt. Die Massefläche sollte jedoch bei den meisten PCB-Designs einheitlich bleiben.
Es ist auch sinnvoll, Komponenten, die viel Wärme ableiten, auf verschiedene Bereiche aufzuteilen. Durch die Trennung dieser Hochleistungsbauteile wird ein Ausgleich der Temperatur im gesamten PCB-Layout gewährleistet. So können Hotspots vermieden werden, in denen hohe Temperaturen von gruppierten Komponenten zusammenfließen. Ermitteln Sie dazu die Werte für den Wärmewiderstand im Datenblatt Ihrer Komponente und berechnen Sie den Temperaturanstieg anhand der geschätzten Wärmeableitung. Kühlkörper und Lüfter können eingesetzt werden, um die Temperaturen der Komponenten gering zu halten. Bei der Entwicklung einer Routing-Strategie müssen Sie unter Umständen sorgfältig abwägen, ob die Platzierung dieser Komponenten mit einer möglichst kurzen Leiterbahnlänge vereinbar ist – das kann durchaus eine Herausforderung darstellen.
Im letzten Schritt des Designprojekts geht es darum, die verbleibenden Teile für die Herstellung zusammenzufügen. Selbst wenn es sich dabei um einen aufwändigen und komplexen Prozess handelt – die doppelte und dreifache Prüfung Ihrer Arbeit auf Fehler in dieser finalen Phase kann zwischen Erfolg und Misserfolg in der Herstellung entscheiden.
Um diesen Qualitätskontrollprozess so einfach wie möglich zu gestalten, ist es ratsam zwei Arten von Prüftests durchzuführen: den Electrical Rule Check (ERC) – zur Prüfung der elektrischen Funktionstüchtigkeit des entworfenen Layouts – sowie den Design Rule Check (DRC), um zu überprüfen, ob alle festgelegten Einschränkungen eingehalten wurden. Im Rahmen dieser beiden Prozesse können Sie ganz einfach Abstands- und Leiterbahnbreiten, allgemeine Fertigungs- und elektrische High-Speed- sowie andere physikalische Anforderungen für Ihre spezielle Anwendung definieren. So gewährleisten Sie eine automatische Durchsetzung der PCB-Design-Layout-Richtlinien zur Prüfung und Validierung Ihres Layouts.
Oft wird dazu geraten, die Designregeln zum Ende der Leiterplattendesign-Phase zu prüfen, also im Zuge der Vorbereitung für die Fertigung. Mit der entsprechenden Designsoftware können Sie jedoch schon während des Designprozesses Prüfungen durchführen und so potenzielle Probleme im Design frühzeitig erkennen und schnell beheben. Wenn Ihre endgültigen ERC- und DRC-Ergebnisse fehlerfrei sind, empfiehlt es sich das Routing aller Signale zu prüfen und sicherzustellen, dass Sie nichts übersehen haben, indem Sie Ihren Schaltplan Draht für Draht durchgehen.
Das waren unsere wichtigsten Richtlinien zum Thema PCB-Layout, die für die meisten Leiterplattendesigns gelten. Obwohl die Liste der Empfehlungen kurz ist, unterstützen diese Richtlinien Sie dabei, in kürzester Zeit eine funktionale, herstellbare Leiterplatte zu entwerfen. Diese PCB-Design-Richtlinien kratzen natürlich lediglich an der Oberfläche, bilden aber eine solide Grundlage für die kontinuierliche Verbesserung sämtlicher Designpraktiken.
Wenn Sie sich für die beste PCB-Design-Software mit einer integrierten, regelbasierten Design-Engine interessieren, die Ihnen zur höchstmöglichen Präzision verhilft, empfehlen wir Ihnen die fortgeschrittenen Design-Tools in Altium Designer®. Wenn ein Design fertig ist und für die Fertigung freigegeben werden soll, vereinfacht die Altium 365™-Plattform Ihnen zudem die Zusammenarbeit und gemeinsame Bearbeitung von Projekten.
Wir haben nur an der Oberfläche dessen gekratzt, was mit Altium Designer auf Altium 365 möglich ist. Starten Sie noch heute Ihre kostenlose Testversion von Altium Designer und Altium 365.
Moderne Benutzeroberfläche
„Ich hatte bisher nicht viel mit 3D-PCB-Designtools zu tun. Ich verwende ALTIUM erst seit Kurzem, habe aber bereits festgestellt, dass das Design flexibler und starrer PCBs in 3D mit Altium viel einfacher von der Hand geht, als ich es mir vorgestellt habe. Der Austausch von 3D-PCB-Layout-Designdateien mit meinen Kolleginnen und Kollegen aus der Mechanik zur Überprüfung war nie einfacher!”
Kelly Dack, CID+ CIT
PCB-Designer/IPC-Ausbilder
Registrieren Sie sich jetzt und testen Sie Altium Designer noch heute.