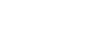
高速で移動する場合でも、高速プリント回路基板を設計する場合でも、適切な設計技法により、設計が意図したとおりに機能し、量産が可能になります。本ガイドでは、ほとんどの最新の回路基板に適用されるPCB設計とレイアウトの最も重要なガイドラインをいくつか集めました。特殊な設計については、追加の基板レイアウトガイドラインに従う必要がある場合がありますが、ここに示すPCBレイアウトガイドラインは、ほとんどの基板設計を開始するのに適しています。
ここに示すガイドラインは、配線、製造可能性、基本的なシグナルインテグリティ、およびアセンブリに役立ついくつかの重要な領域に焦点を当てています。
新しいプリント回路基板のデザインを開始する際に、プロジェクトを管理する重要なデザインルールを忘れがちです。デザインの早い段階で決定された場合、コンポーネントのシフトや再配線を後で行う必要がなくなる単純なクリアランスがいくつかあります。では、この情報はどこで入手できますか?
まず最初に、PCB設計基準の製造会社に相談することから始めます。優れた製造業者は、通常、その性能をオンラインで公開、または情報を文書の形で提供しています。Webサイト上に見当たらない場合は、メールを送信して性能内容を確認します。コンポーネントの配置を開始する前に、これを最初に行うことを推奨します。 作業中は、確認するために予定するスタックアップを提出するか、標準スタックアップデータを使用します。
機能のリストが見つかれば、これらを、作業する際の業界の信頼性基準と比較する必要があります(クラス 2 とクラス 3 、または特殊基準)。これらのポイントを決定した後は、製造可能性と信頼性を確保するために必要なより保守的なデザイン・レイアウト制限を選択することが推奨され、またこれらを基板デザインルールにエンコードできます。
レイアウトプロセスを進める際に、基板デザインルールを使用すると、製造およびアセンブリの問題につながるデザインエラーのほとんどをなくすことができます。基板デザインルールを設定した後、配置プロセスを開始できます。
PCBレイアウトデザイン・プロセスのコンポーネント配置段階は、アートと科学の両方であり、基板上で利用可能な主要なリアルエステイトについて戦略的に検討する必要があります。コンポーネントの配置の目的は、簡単に配線できるボードを作成することです。理想的には、できるだけ少ないレイヤトランジションを使用します。さらに、デザインはデザインルールに準拠し、必須コンポーネント配置を満たす必要があります。これらのポイントのバランスを取るのは困難ですが、単純なプロセスは、基板の設計者が次の要件を満たすコンポーネントを配置するのに役立ちます。
ポイント#1と#2に従った場合、ルート間のクロスオーバーをあまり行わずに、基板の残りの部分をレイアウトするのがはるかに簡単になります。さらに、基板のレイアウトには、そのような最新のルック・アンド・フィールがあります。このレイアウトでは、セントラル・プロセッサーが基板の外周にある他のすべてのコンポーネントにデータを供給します。
コンポーネントを配置することで、電源、グラウンド、信号トレースを配線し、信号がスムーズでトラブルのない移動経路を確保できるようになりました。ここでは、レイアウトプロセスのこの段階に留意する必要があるガイドラインをいくつか示します。
一般的に、電源とアースは 2つの内部層に配置されます。2層ボードの場合、これはそれほど簡単ではないため、 1つのレイヤに大きなグラウンドプレーンを配置してから、信号と電源トレースをもう1つのレイヤに配線します。4層回路基板のスタックアップと高いレイヤー数を使用する場合は、トレースをグラウンド配線するのではなく、GNDプレーンを使用することが推奨されます。電源に直接接続する必要があるコンポーネントの場合に、電源プレーンを使用しない場合は、各電源に共通のレールを使用することを推奨します。十分なトレースがあることを確認し(5~10Aで100ミルの場合は問題ありません)、パーツ間で電源ラインをデイジーチェーン接続しないでください。
一部の推奨事項では、プレーン層の配置は対称でなければならないとありますが、製造について厳重に必要というわけではありません。大型基板では、これは反りの可能性を減らすために必要になる場合がありますが、小さな基板では問題になりません。電源とグラウンドへのアクセスに焦点を当て、すべてのトレースが最も近いGNDプレーンに強いリターンパスカップリングを備えるようにしてから、PCB設計スタックアップで完全な対称性について配慮します。
次に、回路図のネットに一致させるように信号トレースを接続します。PCBレイアウトのベストプラクティスでは、可能な場合はコンポーネント間に短い直接のトレースを配置することを推奨していますが、大型基板では必ずしも実用的ではない場合があります。コンポーネントの配置によって基板の片側に水平方向のトレース配線が強制される場合は、常に反対側にトレースを垂直に配線します。これは、多くの重要な2層PCB設計基準の1つです。
プリント回路基板の設計基準とPCBレイアウトガイドラインは、スタックアップのレイヤー数が増えるにつれて複雑になります。配線戦略では、各信号層を基準プレーンで分離しない限り、交互の層で水平と垂直の配線パターンを交互に使用する必要があります。特殊な用途用の非常に複雑な基板では、一般的に喧伝されている基板のベストプラクティスの多くが適用されなくなる可能性があり、用途に固有な基板設計ガイドラインに従う必要があります。
PCBレイアウト設計では、トレースを使用してコンポーネントを接続しますが、これらのトレースはどの程度の幅にする必要があるでしょうか。異なるネットに必要なトレース幅は、次の3つの要因によって決まります。
特定のインピーダンスや高電流を必要としないトレースの場合、大部分の低電流アナログおよびデジタル信号では、10ミルのトレース幅で十分です。0.3 Aを超えるプリント回路基板のトレースは、もっと幅を広げる必要がある場合があります。これを確認するには、IPC-2152ノモグラフ を使用して、必要な電流容量と温度上昇限度のPCB設計トレース幅を決定できます。
グラウンドプレーンは大きなヒートシンクとして機能し、基板全域に熱を均一に伝達します。したがって、特定のビアがグラウンドプレーンに接続されている場合、そのビアのサーマルリリーフパッドを省略すると、熱がグラウンドプレーンに伝導します。これは、熱が表面近くに閉じ込められるようにするよりも望ましい方法です。しかしながら、表面近くに熱を閉じ込めておく必要があるため、基板上でスルーホールコンポーネントをウエーブはんだ付けで組み立てる場合には、この問題が発生する可能性があります。
サーマルリリーフはPCBレイアウト機能の1つであり、基板をフロー半田付けプロセスで製造できるようにするため、またはプレーン層に直接接続されたスルーホールコンポーネントのために必要になる場合があります。スルーホールがはんだ面に直接接続されている場合は、プロセス温度を維持するのが困難な場合があるため、はんだ付け温度を維持するためにサーマルリリーフを使用することが推奨されます。サーマルリリーフの背景にある考え方はシンプルです。これは、はんだ付け中に熱がプレーン層に放散される速度を低下させるため、コールドジョイントの防止に役立ちます。
一部の設計者は、小さなポリゴンであっても、内部のグラウンドまたはパワープレーンに接続されているビアまたは穴にサーマルリリーフパターンを使用するように指示します。このアドバイスは一般化されすぎています。スルーホールコンポーネントでのサーマルビアの必要性は、銅箔プレーンまたはポリゴンのサイズによって異なり、内部レイヤーで接続を行います。基板の製造を開始する前に、製造業者に確認を依頼する必要があります。
電気的干渉を防ぎながら配線を容易にするために、コンポーネントとトレースをグループ化して、分離する方法に関するPCB設計基準の配線ガイドラインがいくつかあります。これらのグループ化ガイドラインは、高電力コンポーネントを分離する必要がある場合があるため、サーマルマネジメントにも役立ちます。
一部のコンポーネントは、 1つの領域にグループ化することで、PCBレイアウトに最適に配置されます。その理由は、これらが回路の一部である可能性があり、相互に対してのみ接続できるため、コンポーネントを基板の異なる側面またはエリアに配置する必要がないためです。PCBレイアウトが、回路の個々のグループを設計してレイアウトされるようになるので、トレースと簡単に接続できるようになります。
多くのレイアウトでは、アナログコンポーネントとデジタルコンポーネントがあり、デジタルコンポーネントがアナログコンポーネントに干渉しないようにする必要があります。何十年も前の方法では、GNDプレーンおよびパワープレーンを異なったリジョンに分割していましたが、これは最新の基板設計では有効な設計選択ではありません。残念ながら、これは多くの基板レイアウトガイドラインに残っており、EMIを発生させる多くの不適切な配線方法につながります。
代わりに、コンポーネントの下に完全なGNDプレーンを使用し、物理的にGNDプレーンをセクションに分割しないでください。アナログコンポーネントと他のアナログコンポーネントを同じ周波数で動作させます。また、デジタルコンポーネントは他のデジタルコンポーネントと一緒に保管してください。これを、各タイプのコンポーネントがPCBレイアウト設計のGNDプレーンの上の異なるリジョンを占有しているものとして視覚化できますが、GNDプレーンはほとんどの基板設計で均一に保つ必要があります。
また、基板上の多くの熱をさまざまなエリアに放散するコンポーネントを分離することも適切です。これらの高電力コンポーネントを分離する背景には、高温コンポーネントがグループ化されたレイアウトに大きなホットスポットを作成するのではなく、PCBレイアウトの周囲の温度を等しくするという考え方があります。これを行うには、まずコンポーネントのデータシートで 「熱抵抗」定格を見つけ、推定される熱放散からの温度上昇を計算します。ヒートシンクと冷却ファンを追加することで、コンポーネントの温度を下げておくことができます。配線方法を考案する際には、これらのコンポーネントの配置がトレースの長さを短くしないように慎重にバランスを取る必要があり、これは困難な場合があります。
製造のために残りのコンポーネントをまとめてフィットさせるために奮闘するので、デザインプロジェクトの終わり近くでは疲労困憊になりがちです。この段階で作業を二重または三重にチェックすることは、製造の成功と失敗を左右することを意味します。
この品質管理プロセスを支援するために、 Electrical Rules Check (ERC) と Design Rules Check (DRC) を使用して、設定した制約をすべて満たしていることを確認することが常に推奨されます。これらの2つのシステムを使用すると、ギャップ幅、トレース幅、一般的な製造要件、高速の電気的要件、および特定の用途のためのその他の物理的要件を簡単に定義できます。これにより、レイアウトを検証するためのPCB設計レイアウトレビューガイドラインが自動化されます。
多くの設計プロセスでは、製造準備中に設計フェーズの最後に設計基準チェックを実行することが推奨されると記載されていることに注意してください。適切な設計ソフトウェアを使用すると、設計プロセス全体でチェックを実行できます。これにより、設計上の潜在的な問題を早期に特定し、迅速に修正できます。最終的なERCとDRCでエラーのない結果が得られた場合は、すべての信号の配線をチェックし、一度に回路図の1本の配線で実行して、何も欠落していないことを確認することが推奨されます。
こちらは、ほとんどの回路基板設計に適用される当社の最上位のPCBレイアウトガイドラインです。推奨事項のリストは短いものですが、これらのガイドラインは、機能的で製造可能な基板を短時間で設計するのに役立ちます。これらのPCB設計ガイドラインは表面的なものに過ぎませんが、すべての設計作業において継続的な改善を行うための基礎となります。
正確さを保つための基準主導型設計エンジンが組み込まれた、最高のPCB基板設計ソフトウェアを使い始めたい場合には、Altium Designer®の高度な設計ツールを使用してください。設計が完了し、製造作業へ進む準備ができたら、Altium 365® プラットフォームを使用すると、プロジェクトでの共同作業と共有が簡単にできます。
ここでは、Altium 365とAltium Designerで何が可能か、その一部を紹介したに過ぎません。今すぐ、Altium Designerの無償評価版を始めてください。
モダンなインターフェイス
「以前は、多くの3D PCB設計機能はありませんでした。Altiumを使い始めてまだ日が浅いですが、 Altiumを使用して3Dでフレキシブル基板やリジッド基板を設計するのは、予想よりはるかに簡単だと言えます。3D PCBレイアウト設計ファイルをレビュー用機械的コーホートと交換するのは、これまでになく簡単です」
Kelly Dack、CID+ CIT
PCB設計者/IPCインストラクター
今すぐサインアップしてAltium Designerをお試しください。