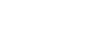
Most designers that work with a bench-top power supply are likely using an isolated regulated (switching) PSU that plugs into the wall. Everything needed to provide stable power at a specific DC or AC level, and with relatively low noise is built into the unit, and you as the designer don’t really have to do anything except connect some leads to the board. Unfortunately, real systems with integrated power sections, or even just power regulator modules you want to integrate into a larger system, aren’t so simple and need some custom design to ensure they operate correctly.
One important aspect of integrating a power supply into your system is setting up and connecting grounds correctly, even for isolated power supplies. If you’re integrating an isolated power supply onto a board with the rest of your major circuitry, you’ll still need to connect grounds in your system. These rules even apply in a PCB for an isolated DC charger or a DC power adapter as the design may need to be connected back to earth, depending on the application and safety concerns. Because bad ground connections can create noise problems, or even a safety hazard, let’s look at the best practices for creating ground connections in your power regulation section when converting AC to DC on your board.
Suppose you’re designing a system that needs to perform power conversion (AC to DC), regulation, and delivery to your circuits in your design. If you think about the practical construction of this system, there are three different possible choices to use for ground:
Power supplies built with transformer coupling, such as AC-DC converters, DC-DC switching converters, or combinations of these two systems, will be built with a transformer bridging these gaps in the PCB layout. The reason for this is simple: unless you’re only operating at low voltage and low current, you typically want isolation in the design to protect users from safety hazards.
These ground systems are not always over a single ground plane for a variety of reasons. This is true of switching power supplies, particularly more complex supplies like LLC resonant converters. The reason ground is so important is that it defines the voltage that a component measures when it operates in a system. When I write “voltage a component measures”, it means a 5 V signal defined over one ground region in a system may not be measured at 5V when measured over some other ground region in a system.
The reason we have two grounds that might include a potential difference is to create a secondary reference that does not expose the user to the input side, which might be a source of high current. We need to maintain this isolation while also providing some way to divert high frequency noise back to the input side and eventually earth. This is done with a capacitor across the two GND regions.
Fortunately, there is a simple solution: tie together the planes with capacitors. Y-rated capacitors are a good choice here for higher voltage/current designs. You can do this easily in your schematics: just locate the component you need for your capacitor, and then bridge the ground nets with a direct connection. The typical place to do this in the PCB layout is close to the transformer. A more complex method, although still valid in AC-DC conversion, is to use a capacitor between the power rail and the AC side of the system.
Note that this only applies to two ground regions on the board. We haven’t considered the chassis or earth just yet. However, there are some basic steps you can take to ensure the enclosure, board, and earth are properly tied together. Unfortunately, this is not so simple and requires thinking about how noise and currents play a role in the system, as well as whether they will create a safety hazard. Here are some resources for further reading to help you decide the best way to connect grounds while maintaining isolation.
If you want to implement a control algorithm for your power system, you will need to allow for feedback from the output back to the input so that the output power can be sensed. This means you need to physically run a line from the output of the side of the regulator back to the input side that contains the switching elements. The question is: what is the best way to provide if your output side is DC, but you want to maintain isolation?
The answer is to use an optocoupler. Placing a trace over the gap is not appropriate as the trace can receive external noise, and switching power supplies can produce a lot of noise. Transformer coupling is also unusable because you’re regulating DC. In the schematic below, the optocoupler is straddling the separation between the ground plane, so we’ve maintained the isolation we want in this supply.
Once you’ve placed your optocoupler, you can route the output to your supply controller. A microcontroller with a PWM output is a good choice for a custom power controller, although some companies make MOSFET gate driver controllers that have a feedback input and are configurable with some external resistors. If you’re designing very precise power regulation or you’re experimenting with control algorithms, this is a simple solution to implement output sensing. You can then use a standard control algorithm to adjust the frequency of your PWM controller to ensure maximum efficiency or to specifically track the desired power output.
The above discussion applies to a certain class of power supplies, known as Class 2 equipment. Is there any limit where you should not do this? As it turns out, the answer is "yes". The capacitor can allow some leakage current to reach the output side, and this level of leakage can be significant enough to create a safety problem. IEEE standards set a limit on this leakage to be <85 uA for non-medical Class 2 power supplies. The idea is to prevent interference while also preventing shock if the negative terminal is ever touched by the user.
In the event there is higher leakage via a capacitor between the two sides of the transformer, the alternative strategy is to use the chassis as a bridge between the two sides. The primary and secondary side can be bridged to the chassis with their own Y-type capacitors. This type of power supply is called a Class 1 power supply. In general, Y1-type capacitors are used in Class 2 equipment while Y2-type capacitors are used in Class 1 equipment. However, this might increase susceptibility to high-frequency common-mode noise, as discussed in this article.
When you need to create a PCB layout with connected grounds for your isolated power supply, use the complete set of layout and routing features in CircuitMaker. Users can build detailed schematics for power supplies and large digital circuits, and data can be instantly transferred into a new PCB layout. All CircuitMaker users also have access to a personal workspace on the Altium 365 platform, where they can upload and store design data in the cloud, and easily view projects via a web browser in a secure platform.
Start using CircuitMaker today and stay tuned for the new CircuitMaker Pro from Altium.