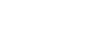
In this article, we will be discussing what PCB build-ups are, and which elements make up a typical PCB—all the way from the basics of PCB build-up, to pre-preg materials, core materials, and copper foils. Let’s get started!
Essentially, a PCB’s build-up is the physical construction of the printed circuit board and its layers made up from different types of materials, mainly copper and dielectric materials.
Adjacent to every copper layer, there is either air or some other sort of dielectric material. The build-up details the thicknesses and material types, and tells us and the manufacturer how we want our PCB to be constructed. For a typical build-up of a four-layer board, see below:
Primarily, we need to consider:
As always with PCB design, we want to consider manufacturability, and the importance of properly communicating with your PCB manufacturer of choice.
When it comes to choosing or deciding on a build-up, there are many other factors that come into play, such as what IPC class you might want, whether you are using high density interconnect (HDI), various aspects such as via aspect ratios, control impedance, surface finishes, and so forth.
A PCB’s layer count is defined by the product type, routing constraints, layout and routing density, package types, power delivery requirements, and so on. You would typically want to go with at least a four-layer board for most designs unless they are very simple (in which case you would choose a one or two-layer board). However, these days a four-layer board is fairly close in price to a two-layer board.
The layer count constrains the overall minimum thickness of the printed circuit board. Up to about eight or ten layers, you can get away with using a standard 1.6 mm thick printed circuit board. As soon as you approach twelve or more layers, your PCB is going to have to get thicker because of all those extra dielectric materials, copper layers, etc.
Pre-preg is a type of dielectric material—a layer of fiberglass impregnated with resin (for example, FR-4) adjacent to a copper layer. The main defining factors of a pre-preg are the dielectric constant or relative permittivity, and the thickness. There are many different types of pre-pregs, such as 1080 or 2116. These will have various available thicknesses (depending on your PCB manufacturer), and different dielectric constants.
The dielectric constants depend on the weave, on which direction you're routing, the frequency of your signals, and more. However, you will be able to get nominal dielectric constant quotes. For 2116 you might get 4.25, and for 7628 you might get 4.6.
In PCBs, there are also dielectric core materials. Cores have copper foils sandwiched on either side. PCB manufacturers will receive pre-made cores, where the copper foils have already been attached to the core dielectric material. As in the case with pre-pregs, cores are also defined by a dielectric constant, and this is usually around 4.6—but remember to check your PCB manufacturer's specifications!
Cores come in various standard sizes (thicknesses), for example 0.2 mm, 0.5 mm, 0.8 mm, and with various copper foil thicknesses on either side.
The final element in our build-up is a copper layer, comprised of thin copper foil. The layer is primarily defined by weight, typically given in ounces per square foot, or thickness given in microns.
Available copper weights and thicknesses depend on outer or inner layers. Inner layers will typically have a thin copper foil (a half or one ounce per square foot). For outer layers (top and bottom) of a PCB, copper foil weights can go up to extremes, such as 8 ounces per square foot.
Of course, the main deciding factor for copper foil thickness or weight is the current handling capability required. By increasing the copper’s thickness, for the same trace width, we are increasing the trace area, and this allows us to have a greater current handling capability for a given temperature rise.
For example, for a 1 mm outer layer trace (allowing a 20 degree Celsius temperature rise), we get 1.9 A capability for a half ounce per square foot copper foil, and for one ounce per square foot copper foil we get 3.2 A (less than double).
Given that we now know the basics of what makes up a PCB in terms of build-up, one of the most important parts is the actual manufacturability. Remember to stay in close contact with your PCB manufacturer of choice to see what options you have in terms of the parameters discussed in this article.
Remember to use Altium Designer’s built-in layer stack manager, which allows you to easily define and adjust your PCB design’s build-up, including pre-preg and core materials, as well as copper thicknesses.