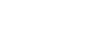
Intelligent placement of PCB layers nullifies RF energy and results in PCAs that pass EMC on their first pass. Read on to learn about the best PCB stacking techniques.
ALTIUM DESIGNER
Professional PCB design tool with proficient PCB signal layer and stack-up management.
Use inner layers with adjacent ground planes for clocks
When considering how to determine PCB layers stack-up, the best practice is to prioritize signal integrity. Signal integrity occurs when RF current generation is avoided with the careful organization of the layers. RF currents are generated through unwanted impedances built into the material giving an opportunity to generate common-mode currents. Common-mode currents are the primary source of RF energy. RF energy gets into the power distribution network or emits into free space as noise. Noise presents itself as reflections, ringing, or crosstalk.
The PCB layer stack-up may be designed to incorporate features useful to maintaining signal integrity. Maximum capacitive decoupling in the power distribution network is achieved by placing power planes directly adjacent to ground planes in the layer stack-up (see figure above). Signal planes or PCB stacking layers should always have a ground plane adjacent to the PCB stack-up. Including a ground plane next to each signal layer enhances flux cancellation and removes noise. Minimizing spacing between conductive PCB stacking layers increases flux cancellation.
The intentional routine continues the best practice layer stack-up design for signal integrity. High-speed traces are best-routed stripline to take maximum advantage of both shielding and of flux cancellation on the inner layers with adjacent ground planes. Less sensitive traces at low risk for coupling through the air are best-routed microstrip on the outer layers of the Printed Circuit Board. Further routing techniques incorporate an aspect ratio for chassis ties with ground stitches between each. Ground fill between traces on outer layers with plenty of ground stitches provides return paths and mitigates the creation of loop currents.
The root cause of noise in a PCB is the development of RF energy across unwanted impedances throughout the PCB stack-up. RF currents develop when unwanted impedances build within the Printed Circuit Board during design. Impedance builds as inductance on windings of inductors and on the leads of discrete such as resistors. Loops give the opportunity for switching currents to produce RF energy into the air.
Whether it’s a single standard PCB thickness board, multiple boards, multilayer PCB, or a design where your primary concerns are the PCB traces, holes, and pads involved, impedance can always be an issue. ICs and interfaces with other materials cause mismatches that build unwanted impedance also leading to the generation of RF currents. When unwanted impedance builds onto nets greater than that of air, RF energy takes the path of least resistance and emits into free space.
Finetune signal layer characteristics during the route
Mitigate RF energy with a floorplan that discourages unwanted impedances and unnecessary materials such as excessive copper weight thickness. Design the PCB stack-up layers to eliminate impedance buildup and shunt RF energy to the chassis. Route signals to ensure the return path is directly underneath the signal trace. Avoid making loops that generate impedance when fast-switching signals are present on a PCB. Evaluate PCB stacking techniques as buried vias are placed to ensure no discontinuities exist. Discontinuities produce slots in layer planes and can force return paths into loops that emit noise. Place decoupling capacitors on each component’s power rails to shunt switching signals to the ground. Place bypass capacitors on switching signals at connectors entering and leaving the design.
Design With RF Circuit Impedance in Mind so Your Designs Won’t Look Bird-Brained
Implement PCB Floorplanning: The First Step to PCB Design Integrity
Arrange power and ground layers adjacent to one another for clean power distribution throughout the PCB layer. Clean power distribution results from low-impedance capacitive decoupling when power and ground layers adjoin each other in the stack. Continue design integrity for the power distribution network throughout the layers by adding decoupling capacitors at each and every component power lead interfacing to the PCB layer stacking.
Designing around decoupling capacitors at each component power lead will provide energy for large digital networks that switch simultaneously. Proceed with power distribution integrity throughout the layers by adding decoupling capacitors at signal pins that undergo transitions during the clock. Decoupling and bypass capacitors provide enough energy to hold up intended signals during operation, preventing ground bounce and unintended injection of RF energy into the PCB layer stacking.
Adjust critical impedances for high-speed signals
Layer signal planes adjacent to ground planes prevent loops that generate RF energy. Loops cannot develop when return planes are located directly next to signal planes. Via placement is critical to avoid slots in the layer stack where signals may need to travel around slots thereby generating loops. In addition, high-speed signals develop flux in both the signal net and the return net.
This flux is equal and opposite, signal and return. Maximum cancellation occurs when high-speed signal and return are placed directly adjacent to one another. Cancellation of flux generated by high-speed signals must be accomplished to maintain electromagnetic compliance (EMC). Designing the layer stack to ensure return layers are adjacent to each and every signal layer results in electromagnetic compliance (EMC). EMC indicates the layer stack was designed to properly mitigate flux generation.
Use Layer Placement for Power Integrity in PCB Power Distribution Network
Use Transmission Line Calculators in PCB Design Nets and Layers
Design for Electromagnetic Compatibility (EMC) in PCB: Let Your Revels Never End
The Layer Stack Manager provides an elegant tool for PCB design guidelines and setting layer characteristics such as thickness. It is a visual tool set up as a table with direct access for Printed Circuit Board editing. Columns for the material definition of copper, prepreg, and core along with surface materials are specified here. The realization of high-speed design requirements that employ designed thicknesses is inserted here along with a definition of dielectric material.
The dielectric material for most Printed Circuit Boards today is FR4 and the Layer Stack Manager automatically inserts its dielectric constant into the stack manager. You may work in either Imperial or metric dimension units. Preset layer configurations are available to speed up your design work or you may load a previously configured stack from another design project. Drill pairs are accessible via a given navigation button. A separate radio button navigates to the Impedance Formula Editor.
Use the Impedance Formula Editor to control impedance for high-speed signals
Use built-in equations for calculating microstrip and stripline impedance for high-speed signals in your PCB layers. The built-in equations are located in the Impedance Formula Editor within the Layer Stack Manager. The built-in equations pull from material thickness and dielectric of nonconductive laminates and from copper characteristics given in the Layer Stack Manager. Radio boxes within the editor allow direct access to equation variables should your design require analysis for embedded microstrip or dual stripline.
Make life easy for PCB layout layer design using Schematic Design Rules
Enable accurate and error-free high-speed layout in your layers
Easily select and route specific net classes using Altium Design ActiveRoute
A printed circuit board is only as strong as its design, make sure that your software can get a board or boards out quickly and reliably through Gerber files accurately displaying PCB trace thickness, components, pads, and solder for heat dissipation. Don’t let your design suffer from board layouts that are inaccurate or have not been integrated properly between schematic board design and board layout.
Altium Designer is a powerful tool that gives you the Layer Stack Manager to set up stacked PCB layers for RF energy nullification. If you’re looking into how to determine PCB layers, use the Layer Stack Manager to minimize stray impedance buildup using the Impedance Formula Editor. Use the Editor to carefully design high-speed signals to eliminate unwanted impedances that develop RF energy. Altium Designer tools intelligently set stacked PCB layers and signal impedance so your PCA will pass EMC the first time.