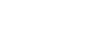
With the electronics industry deepening in complexity and dependence on critical components during times of shortage and regulatory change rising, it has become most important that PCB designers and manufacturers approach the development of printed circuit boards (PCBs) with adaptability and compliance in mind. Doing so requires meticulous attention to detail, especially when it comes to sourcing components.
With that in mind, traceable component sourcing, where the origin and journey of each component can be demonstrably tracked, has become an indispensable tool for PCB manufacturers.
With geopolitical conundrums causing supply chain disruption and a dearth in accessibility to certain natural resources, new initiatives related to ESG, and consumer awareness around the use of potentially harmful chemicals in electronics, global policymakers are working to change the way that the industry and mass demand impacts the planet. As a result, PCBs, which give life to every device, are now subject to a myriad of changing regulations that depend on their application. To name just a few:
To meet these regulations, companies must command a solid knowledge of component composition and have in place a robust system for tracking their provenance. Traditional, paper-based methods of documentation are now, ultimately, inadequate in the pursuit of transparency and traceability due to the complexities of regulations, especially REACH, which has extensive chemical registration requirements.
With that in mind, putting in place a digital system for traceable component sourcing is the route forward, and it offers a multitude of benefits for PCB manufacturers that extend beyond just regulatory compliance:
The benefits of digitalization aside, we’d be remiss not to point out that there are so many options available for PCB manufacturers that intend to achieve traceable component sourcing, and more opportunities to optimize the process come into existence every year. Below are three such technologies that form the foundation of traceable solutions.
A technology still in its infancy, blockchain, which offers an immutable digital record of component origin and movement throughout the supply chain, creates a cryptographically secure, distributed ledger that tracks every step a component takes from the raw material stage to its final destination in a PCB. Many leading companies, including Walmart, Coca-Cola, Ford, and Maersk, have now invested in blockchain to unlock this shared point of truth across their multinational supply chain networks.
Cloud-based systems—PLM and, to a lesser extent, ERP, for example—provide a centralized platform for the management of component data, which gives companies access to real-time tracking and reporting. These systems, which nearly 92% of digital leaders have adopted, are optimized for ease of use, with user-friendly interfaces that capture, store, and analyze component data and enable real-time visibility into the supply chain so that manufacturers can track component movement and identify potential issues when they crop up.
EDI, software that sits between siloes to facilitate communication, streamlines data exchange between manufacturers and suppliers so stakeholders can access accurate and consistent component information. Specifically advantageous for PCB manufacturers, this system can automate the exchange of data points like part numbers, material composition, and certifications—removing the risk of human error, which is common in manual data entry tasks.
The implementation of traceable sourcing practices is, unfortunately, not a simple flick-of-the-switch scenario. It will take a multi-pronged approach by companies, and while that might represent a substantial initial outlay, the eventual gains do outweigh the expense. Here are the key considerations:
Building strong relationships with reliable suppliers is definitely the foundation of a successful traceability program. If all parties are on board, that is. Companies should collaborate with suppliers who already prioritize ethical sourcing and maintain robust traceability systems, or if they have an abundance of resources, they should consider working with suppliers willing to invest in upscaling their efforts with the company’s assistance. When looking for suppliers, focus on those that can provide comprehensive documentation on component origin, certifications, and compliance with relevant regulations.
Data collection shouldn’t be siloed; with that in mind, establish clear protocols to capture and store the component data mentioned throughout this article (critical for RoHS compliance). By standardizing organizational-wide data collection, companies have consistency, which facilitates efficient analysis.
Leverage the appropriate technologies, including those listed above, to automate data collection and management. Investment in traceability tech streamlines the process and reduces the risk of human error; importantly, companies should look into solutions that integrate with existing manufacturing workflows and, as most are now using the ‘as-a-service’ model, offer scalability to accommodate future growth.
The regular auditing of suppliers and internal processes helps companies to ensure the integrity and effectiveness of the traceability—and, indeed, any collaborative—system. Suppliers and third-party vendors should provide the company with regular updates. However, companies should err on the side of caution and conduct regular on-site visits to facilities to check in on workplace conditions, internal procedures, and employees to identify any potential gaps, weaknesses, or issues that might bring their brand into contention with governing bodies and consumer discontent.
Unfortunately for companies that used to toe the line between ethical and unethical practices, traceable component sourcing is no longer a luxury but a necessity for PCB manufacturers that intend to remain compliant. If companies can embrace available technologies and implement robust sourcing practices, manufacturers can guarantee that their PCBs meet the highest standards of quality and safety while also safeguarding brand reputation and market position. It’s getting even more competitive out there, and while traceability initiatives might affect the bottom line at first, it’s important to remember that these changes aren’t just about meeting regulations; compliance will, in the end, give companies a strategic advantage through hard-earned consumer trust—something achievable only through transparent and responsible manufacturing practices in a world full of lesser products.